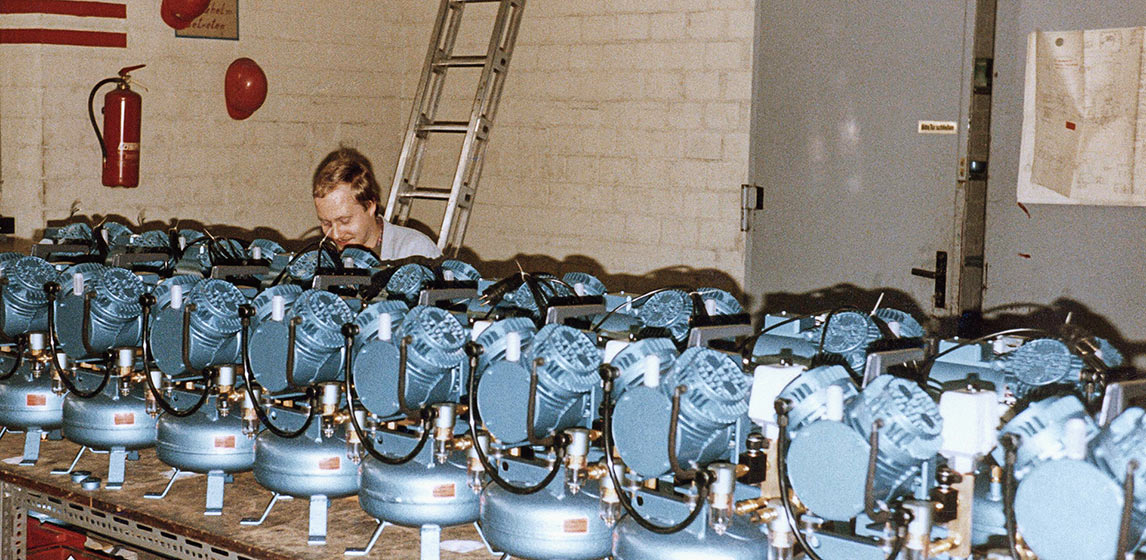
The “Tiny Lunar Module” simpliport
In the early 1970s, the dramatic Apollo 13 mission is fresh in everyone’s minds. At the time, KNF’s new portable compressed air system “simpliport” gets nicknamed the “tiny lunar module” by the trade press – with its compact design and three rubber feet, it is reminiscent of the Apollo 13’s lunar module Aquarius, which had helped to ensure the astronauts’ safe return to Earth.
This is actually quite an apt comparison for the compact compressed air system unveiled to the public by KNF in 1971. The system is equipped with a KNF diaphragm compressor to allow it to produce oil-free compressed air. Its name “simpliport” is chosen to reflect how easy it is to set up, operate and transport.
The device features a 5-liter compressed air container and various diaphragm compressors, which can be adapted depending on the intended use. It is put into operation using a 5-meter connection cable and a safety plug. Small but powerful, “simpliport” has everything a compressed air system could need: an adjustable pressure monitor, an automated relief valve, a combined intake filter and silencer, a manometer, a safety valve, non-return valve and stopcock, and a motor protection switch make the small pump a highly sought-after product.
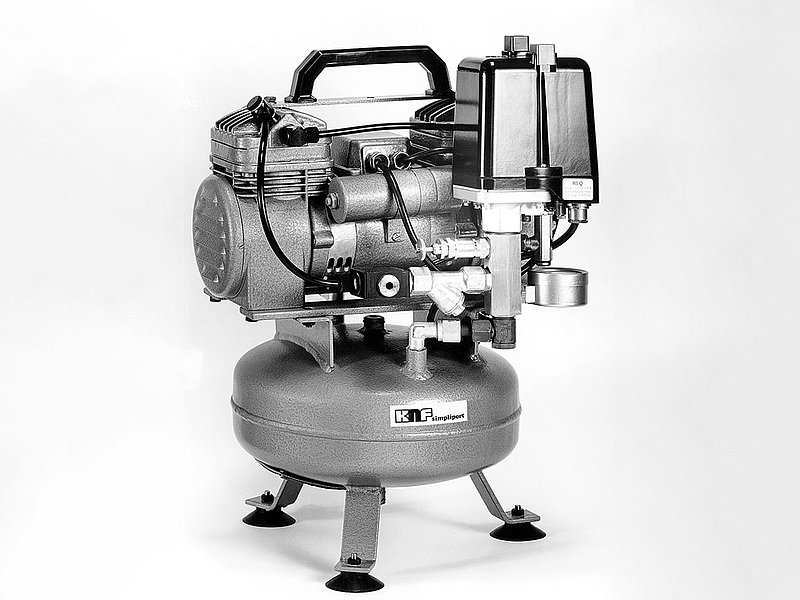
It is perfectly designed for the laboratory sector, where low flow rates, fast portability and the ability to adapt flexibly to different test setups are essential. But “simpliport” is also ideal for use in manufacturing. For example, the small, portable, maintenance-free system can reliably support the operation of paint spraying equipment or supply compressed air to pneumatic controllers and regulators. What’s more, “simpliport” is good value for money and economical to operate.
The “simpliport” system is also very well received by the book printing and image reproduction technology sectors at the time. The halftone printing technique commonly used back then is a relief printing method like stamp printing and requires plastic stereotypes to be manufactured using a wash-out process. This involves partly exposing a photopolymer plastic plate to light so that the unexposed sections can be washed out with solvents. To ensure that the residual polymer material can be completely removed after the drying process, the plate has to be dried and cleaned using oil-free compressed air. Requiring precision and flexibility, this is the exact type of challenging task for which “simpliport” is perfectly suited.
KNF Blog Knowledge Flows
Follow the latest trends and stories on how diaphragm pump technology drives evolution in the market.
