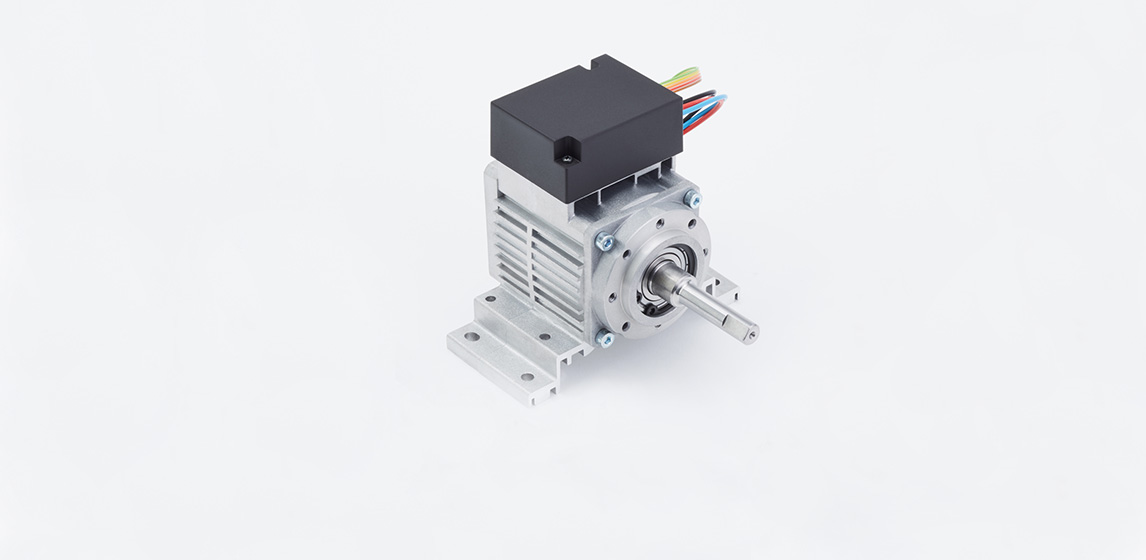
Digital Pump Customizing: Unlocking the True Potential of BLDC Motors
Tailoring a pump to the exact requirements of customers is the core business of KNF. When the choice is made to use a brushless direct current (BLDC) motor for a pump, sophisticated communication with the motor becomes possible. This allows for closed-loop communication between the controller and the motor, and opens up the possibility of digital pump customization.
Compared to normal DC motors, BLDC motors offer several advantages ranging from longer lifetime to higher efficiency and many more. When used in a pump, BLDC motors allow for electronic control and communication as well as digital pump customization. For some BLDC motor options, KNF has developed and defined its own control protocol which is transmitted via the serial digital interface Universal Asynchronous Receiver Transmitter (UART). In addition to this serial digital interface, the user can control the motor speed by a pulse-width modulation (PWM) signal or an analog control voltage.
BLDC Motor Status Always Accessible
By sending a signal to the motor, customers can start and stop the pump or adjust its speed without changing or disconnecting the operating voltage of the motor. Depending on the type of BLDC motor, communication with the motor enables receiving information such as motor speed, motor status, temperature, electrical current and error messages. This way, the customer can always monitor the operational status of the pump, and use the generated data for further processing.
Digital Pump Customization Opens Up Possibilities
In close collaboration with the customers, KNF tailors the entire pump exactly to their individual needs. With regard to the digital customization of BLDC motors, many parameters can be defined. The customizing options vary depending on the motor type used.
Examples include:
- Motor Speed Range
The motor speed range defines the permissible minimum and maximum motor speed. It is also possible to set the motor speed to a fixed value. The motor speed is regulated by the internal controller.
- Motor Speed Ramp
The motor speed ramp defines the maximum allowed acceleration of the motor. This can be used to avoid high electric loads caused by rapid changes in the motor speed.
- Threshold Values
Threshold values can be defined for maximum temperature, maximum electrical current and maximum locked-rotor period. This period defines the time allowed for the shaft to stand still when it should rotate. When one or more thresholds are exceeded the motor stops and issues an error.
- Starting Behavior
The starting behavior defines whether the motor starts running directly when an operating voltage is applied or only after a command has been received.
- Motor Speed Output
The motor speed output defines how the current motor speed is indicated at the “Motor Speed Output” (not UART). A PWM signal (default) or 6 or 60 pulses per revolution may be selected.
- Control Characteristic
When using the PWM signal or the analog control signal for setting the motor speed, a control characteristic must be defined via parameterization, the setting of unique motor parameters during initial motor programming. The control characteristic describes the relation between the PWM signal or the analog control signal and the motor speed. Therefore, a lower and upper limit for the PWM signal or the analog control signal must be defined. Below this lower limit for the input signal there are two possibilities: either the motor stops, or the motor turns at the defined minimum motor speed.
Get in touch to find out which digital customizing options are available for your pump.
75 Years: KNF Celebrates Company Anniversary
A treasure chest filled with memories, facts and stories. Learn more about KNF’s company history.
