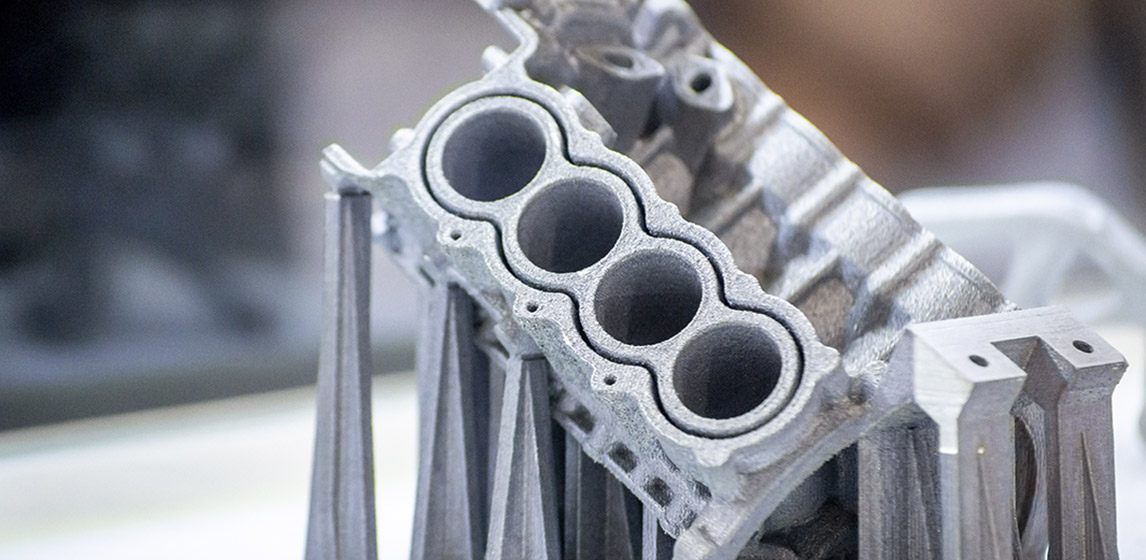
From Prototyping to Mass Production
Originally developed for rapid prototyping, 3D printing has become a reliable process for large-scale production. Only recently did manufacturers consider 3D printing as an alternative to conventional production methods due to the improvements in production speed, structural integrity and costs. As one subsegment within the available additive manufacturing technologies, metal binder jetting has the potential to unlock new paths for the use of 3D printing in industries with a demand for high-volume production. In the following blog post you will learn more about the background of metal binder jetting process and the key role played by KNF diaphragm pumps.
Recent development in 3D printing
There has been an emerging trend of expanding 3D printing beyond small-scale manufacturing into mass production. This trend has been championed by a continuously growing number of players in additive manufacturing. With the common goal of industrializing 3D printing, these companies have driven innovations in the development of printing hardware, resulting in more sophisticated 3D printing systems at an affordable price for manufacturers.
Key trend: metal binder jetting
Metal binder jetting is becoming one of the key technologies among metal 3D printing. High printing speeds and complex component production are the valuable differentiators of the technology. A growing number of companies have recognized the potential of metal binder jetting and are working intensely to take advantage of the opportunities it offers. Metal binder jetting provides manufacturers of applications currently infeasible with metal 3D printing technologies with a fast and cost-efficient alternative in additive manufacturing. This is an impactful development, particularly for high-throughput market applications such as medical prototyping, automotive production, tooling, dental and manufacturing. Companies within these markets can now afford to print their own components sparing them from the high manufacturing costs of their specialized equipment.
How does metal binder jetting work?
In the process of metal binder jetting, layers of powdered metal are joined by the selective deposition of a liquid binder. While other additive techniques use a heat source to bond materials together, binder jetting doesn’t rely on heat during the initial process of construction. The process begins with the distribution of a thin layer of metal powder while using print heads directed to jet binder droplets into the powder bed. A new layer of powdered metal is laid down on top over and again until the object is completed. This can be done to print one large part, or an array of parts stacked on top of one another.
As technology is improving and speeds are increasing, the delivery of the binder to the printhead has never been more important. The accurate placement of the binder onto each layer is critical to hold the final part together. The subsequent sintering process fuses the metal powder and binder under the influence of heat. This results in precise components in accordance with tolerance specifications.
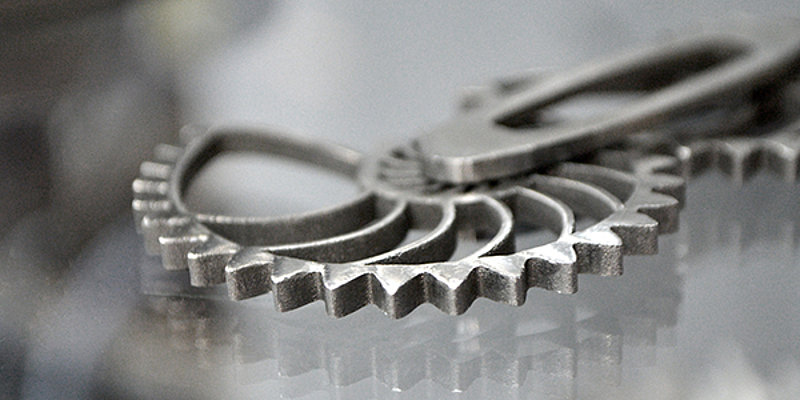
Where KNF pumps come into play
Metal binder jetting technology may seem straightforward, but the focus of printing hardware manufacturers is on the details to ensure optimum results – this also includes the right choice of components for their equipment. KNF diaphragm gas and liquid pumps have proven to be reliable components for a range of functions within the metal binder jetting process. This includes the recirculation, degassing and transfer of the binder fluid, as well as filling or evacuating debinder fluid during the post-printing process. In the transfer of binder to the print bar, KNF pumps ensure smooth flow with low pulsation in order to reduce cavitation and the formation of air bubbles in the media.
KNF has developed a new FP and FK series of low-pulsation diaphragm liquid pumps targeting these types of printing applications. In addition, KNF responds individually to the needs of its customers in the additive manufacturing printing field by customizing their standard pumps for each project. Flexibility is offered to customers through a range of materials, motors, and mechanical connection options, including options for moving aggressive media at elevated temperatures.
Keeping an eye on the future
In the future, manufacturers of printing hardware will continue to refine metal binder jetting, driving innovation in the development of 3D printing equipment. Ultimately, this will help the technology gain a valuable share of the overall manufacturing market. In this process, KNF stands by the side of their customers, providing customized pump solutions, offering long service life, chemical resistance and precise operation.
75 Years: KNF Celebrates Company Anniversary
A treasure chest filled with memories, facts and stories. Learn more about KNF’s company history.
