KNF vacuum pumps and systems are used in scientific research at the university FAU in Nuremberg
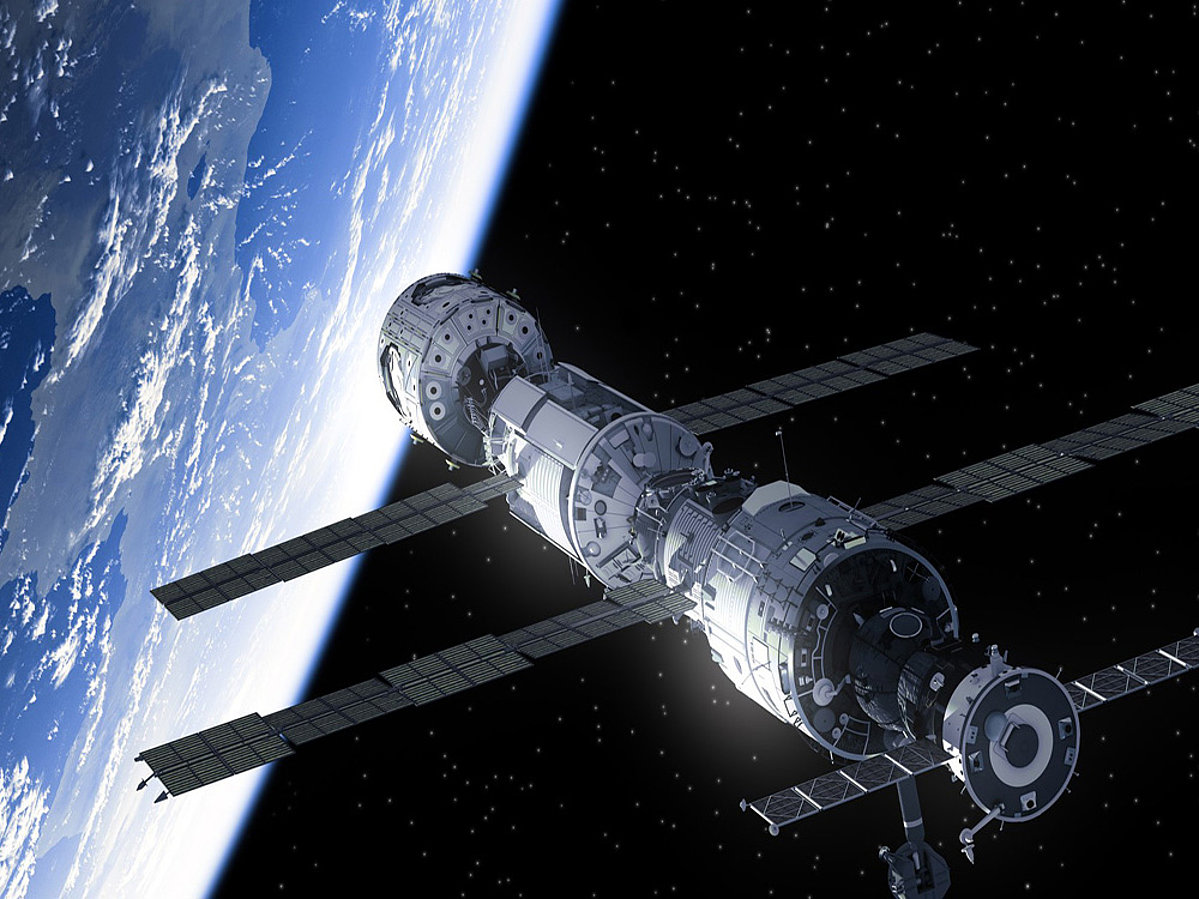
Every day six astronauts of the International Space Station (ISS) zoom through time and space at 28,000 kilometres per hour and circle around the Earth in the process. 16 times in 24 hours. The crew can only survive because their flying "living and working space" is designed for extreme conditions. The ISS offers the necessary stability, its shell and glazing protect against heat, cold and pressure loss and the utilities bring a little of the earthly living conditions into space. The survival of astronauts depends on the reliability of all systems and components.
Through a recommendation by a cooperation partner, we received an inquiry for a pump to be used for recycling used air in the ISS. The technical requirements for such a project are enormous and the cooperation and collaboration must match.
Our engineering team took on the challenge of working on the development of a fluid pump with Airbus Defence and Space for four years. Airbus Defence and Space is part of the Airbus Group, specializing in military aviation, military and civilian aerospace systems as well as sensors and communications technology for defence and security.
The pump for outer space use was finished in autumn 2018. Two copies of the pump were ultimately integrated into the new Life Support Rack. This unit, also known as the Advanced Closed Loop System (ACLS), has the task of recovering carbon dioxide from the air in the spacecraft and generating fresh oxygen for the crew through electrolysis. The new ACLS rack was installed in the ISS Destiny module by German ESA astronaut Alexander Gerst on 2 November 2018, when he was in command of the ISS.
The two diaphragm pumps used were part of an electrolyser that generated oxygen and hydrogen from water. The pumps delivered the supply water from a plastic bag into the ACLS. Oxygen was extracted by first converting the carbon dioxide from the cabin air into methane and water. This process required hydrogen which, in turn, was obtained by splitting water molecules and supplying energy. The electrolytic process extracted breathable oxygen from the water.
Thanks to oxygen recycling, 450 kilograms of water load are saved annually
Airbus expected the system was designed for a crew of three astronauts and saved 450 kilogrammes of additional water load per year. At a price of 33,000 euros per kilo of payload, the ACLS thus reduced costs by about 15 million euros. At full power the ACLS extracts 3 kilogrammes of CO2, supplies 2.5 kilogrammes of oxygen and produces 1.2 kilogrammes of water per day.
Extremely reliable components and systems were needed in space flight to ensure that all processes were always running safely. The demands on the design of the pump were correspondingly high. After all, at an altitude of 400 kilometers above the earth's surface, defective components cannot be replaced within an appropriately short period of time.
In this instance, the developers deliberately opted for a proven fluid pump that was also extremely small, powerful, durable and efficient on Earth. However, they received new specifications over and over during the 48 months. The engineering team was faced with the challenge of retaining the key components of the standard pump used, ensuring that it maintained its reliability), and simultaneously making significant structural changes to make the pump suitable for space. The pump was adapted several times: the housing was made of stainless steel, the vacuum ball bearing optimized and stainless-steel fittings were made for the fluid connections. Additionally, engineers had to tackle the problem of integrating a space-saving drive motor.
Such challenging tasks push the boundaries of what is constructively possible, which benefit our pump project assignments worldwide every year. Most are developing into a success story. The same is true for the space pump.