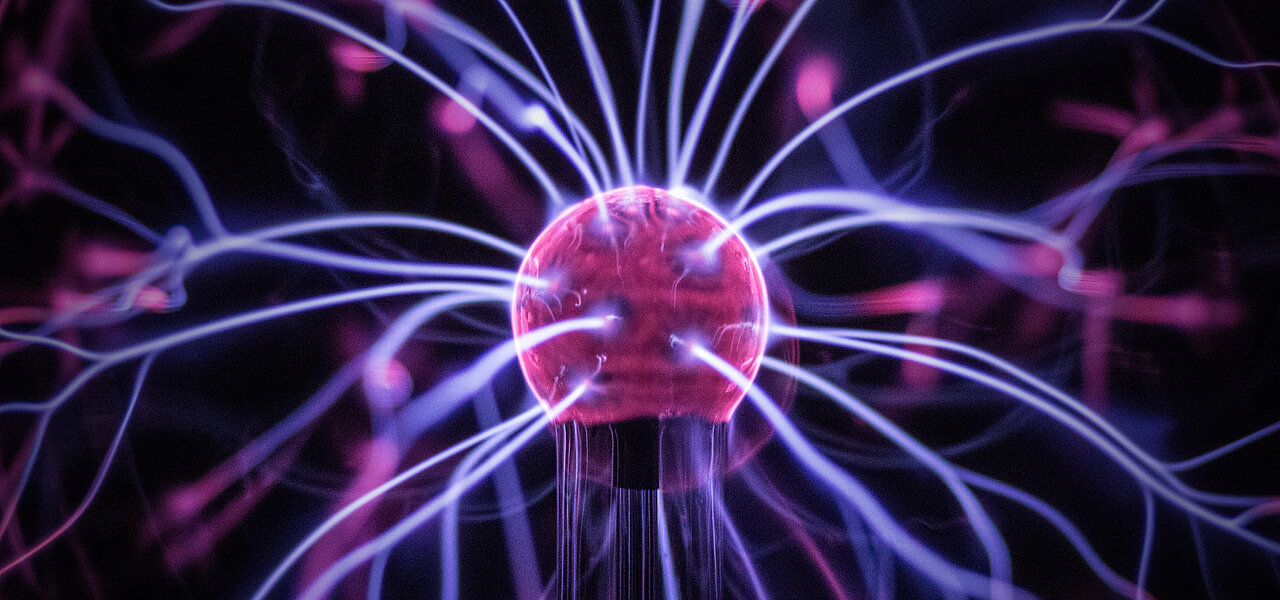
How KNF Diaphragm Pumps Enhance Noble Gas Recovery
Noble gas recovery not only helps conserve natural resources but also reduces the environmental impact of their production. By recovering and reusing these gases, industries can minimize waste and reduce their dependence on new gas sources. Beyond the financial benefits, this can contribute to their overall sustainability.
Sources of Noble Gases
Noble gases such as helium, neon, argon, krypton, xenon, and radon are extremely rare in the Earth's atmosphere. Most helium, for example, comes from natural gas fields where it is a by-product of natural gas extraction, while neon, argon, and krypton come from the by-products of air liquefaction. The even rarer xenon and radon are typically obtained from nuclear reactions. Recovering these valuable gases is a complex and challenging process due to their low concentrations and complex purification requirements.
Noble gases are typically found in trace amounts, often less than 1% of air, and require highly efficient capture and purification techniques. Their chemical inertness adds to the difficulty, making separation from other gases a complex task. Given the energy-intensive nature of some of these processes, the recovery can also be very costly.
From Cryogenic Distillation to Membrane Separation: Exploring Noble Gas Recovery
Various techniques are used by industry and laboratories to efficiently recover noble gases. These techniques typically involve a combination of physical and chemical processes to extract and purify these valuable gases. The following is a selection of the methods available:
- Cryogenic distillation: A common noble gas recovery process, cryogenic distillation uses the different boiling points of gases to separate them. First, air is cooled to a liquid using cryostats and then fractionally distilled to isolate gases such as helium, which has a lower boiling point than other gases. While effective on a large scale, this method is very energy intensive and requires sophisticated equipment.
- Adsorption: Adsorbents such as activated carbon and zeolites are used to selectively remove noble gases from gas mixtures. Due to their high affinity, they bind to noble gases while allowing other gases to pass through. As the gas mixture flows through an adsorbent bed, the noble gases are retained and later released and purified by heating. Although this process has the advantage of low energy consumption and operating costs, it requires careful selection of the adsorbent and optimal operating conditions for efficiency.
- Membrane separation: A technique well suited for the recovery of noble gases from low concentration mixtures, membrane separation involves semi-permeable membranes made of polymers or ceramics that selectively filter gases based on molecular size. Noble gases diffuse through these membranes faster than other gases, allowing them to be separated and recovered. The process is favored for its simplicity, compact design, and ability to operate continuously, although it may not be ideal for high concentration applications.
- Evacuation: This method uses vacuum pumps to remove residual gas from cylinders by efficiently evacuating them to vacuum levels. While the amount of gas recovered from a single cylinder may be minimal, the cumulative effect becomes significant when evacuating multiple vessels. Although simple, this approach ensures optimal utilization of noble gases that would otherwise be lost.
Diaphragm Pumps for Precision Gas Recovery
Two-stage diaphragm pumps such as the KNF N 630.15 are particularly advantageous for noble gas recovery. They combine efficient and reliable performance under demanding conditions with the flexibility to handle a wide range of volumes, pressures and gas compositions. Furthermore, they are highly versatile and customizable, suitable for both small- and large-scale applications, while their compact design and inherent gas tightness minimize leakage. To ensure this, an additional helium leak test is performed on these pumps prior to shipment.
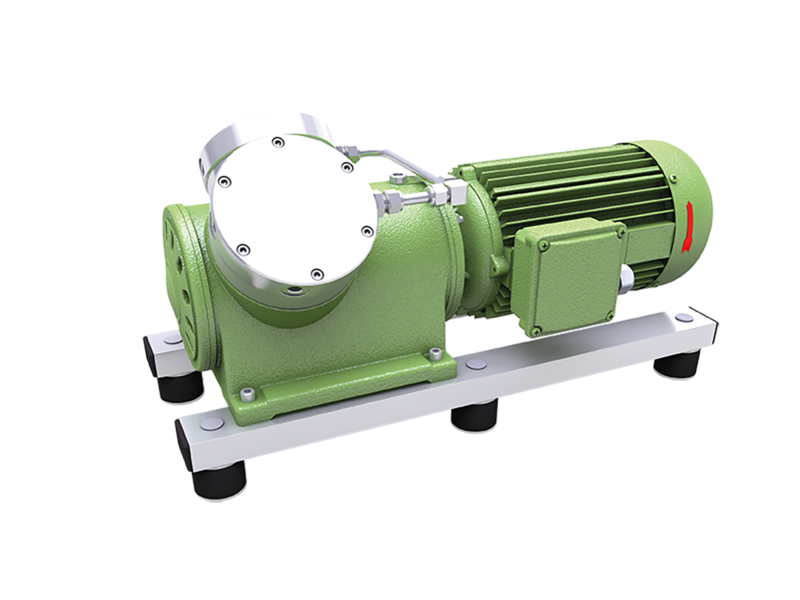
KNF diaphragm pumps and compressors effectively meet the challenges of gas compression, where mechanical energy is converted into heat. This is especially true for noble gases, which generate more heat due to their higher isentropic exponent. To maintain the integrity and efficiency of noble gas recovery, KNF pumps can be customized with features such as pump head water cooling, inlet gas temperature reduction, and integration of temperature sensors into the intermediate plates, all of which contribute to better heat management during compression.
With extensive experience in heat management for compression processes and in improving the integrity and efficiency of noble gas recovery, KNF provides detailed engineer-to-engineer consultation to find the ideal solution for even the most challenging applications.
Contact us to find the best pump solution for your application!
75 Years: KNF Celebrates Company Anniversary
A treasure chest filled with memories, facts and stories. Learn more about KNF’s company history.
