
What Is Pump Cavitation and How to Avoid It?
Pump cavitation, often experienced in fluid systems, can cause excessive vibrations, noise, and damage to pump components, affecting pump performance. It can also alter the transferred media which may affect its quality. We will explore the details of pump cavitation, particularly its damaging effects on pumps and reduced flow or pressure. Understanding this issue is essential to prevent cavitation and maintain maximum system efficiency while avoiding damage and pump repair or replacement.
An Introduction to Pump Cavitation
Cavitation occurs when changes in pump pressure lead to the intense formation and collapse of vapor bubbles in a liquid. The high-energy collapse of these tiny bubbles generates heat and shock waves that can lead to a range of issues. These can include reduced pump efficiency, increased noise, mechanical wear, and damage to the pump housing, the diaphragm, and other components such as seals.
In pump systems, cavitation happens when the local pressure drops below the pumped liquid’s vapor pressure, such as during high-speed flow or in areas of turbulence. Controlled pressure and flow, along with advanced pump design, are essential to reducing or eliminating the effects of pump cavitation and maintaining the integrity and efficiency of the pump system.
Diaphragm Pumps: A Key to Sensitive Fluid Handling
Diaphragm pumps are excellent for handling multiple fluid types, and this can be particularly relevant for applications where sensitivity is crucial. These versatile pumps can handle a wide range of fluids, from corrosive, abrasive, and low-viscosity substances to delicate liquids susceptible to degradation.
Changes in the liquid mixture can affect pump performance and system integrity. KNF has developed diaphragm pumps that use special BLDC (brushless DC) technology to offer precise pump control and performance. This means the pump’s flow rate can be matched to the fluid being handled. Gentle handling also helps protect the pump and components from wear or damage.
The Impact of Pump Cavitation on Sensitive Substances
By design and due to the precise control of the pump’s performance, diaphragm pumps are a premium pump choice for handling sensitive, abrasive, and shear-sensitive media. However, cavitation, even in advanced diaphragm pump systems, can impact the quality and integrity of any substance being pumped.
Cavitation damage is particularly significant in the pharmaceutical, food processing, and ink manufacturing industries, where maintaining liquid quality is essential. Ink manufacturing, for instance, relies heavily on a diaphragm pump’s precision handling and distribution of pigmented inks. Cavitation can introduce tiny bubbles or cause shear forces that disrupt the ink's uniformity, leading to inconsistencies in color or texture. Similarly, in pharmaceuticals, instability caused by cavitation can compromise the success and stability of drug formulations. Food processing industries face similar challenges, where cavitation can affect product texture, flavor, and shelf life.
With the sensitivity of these substances, industries need to implement strategies to minimize cavitation effects in their pump systems. This process may involve optimizing pump settings and flow rates, choosing appropriate pump materials, or incorporating additional filtration processes. By addressing the impact of cavitation bubbles on liquid quality, industries can uphold the necessary standards for product consistency, performance, and customer satisfaction.
Preventing Cavitation in Diaphragm Pumps
Preventing cavitation damage in diaphragm pumps is vital for maintaining good operational efficiency, meeting the pump’s performance curve, and protecting sensitive substances. One of many effective methods is to ensure that the pump operates within specified atmospheric pressure limits, avoiding conditions where the suction pressure drops below the vapor pressure of the liquid. This can be done by increasing the pressure upstream from the pump.
Proper pump sizing and speed control are also essential, as using a larger pump running at lower speeds can help maintain sufficient suction pressure and reduce the risk of cavitation. Regular maintenance, including inspecting the pump, cleaning pump components, and monitoring fluid quality and temperature, also plays a crucial role in preventing cavitation inside the pump.
Smooth Flow pump technology: Smooth Flow technology can prevent cavitation in diaphragm pumps. This specialized design prioritizes low pulsations and pressure fluctuations, promoting a consistent and steady liquid flow. By minimizing disruptions in flow, Smooth Flow pumps reduce the formation of vapor bubbles, reducing the risk of cavitation.
Optimal speed control: Another strategy to prevent cavitation is to choose a larger pump that operates at lower speeds. Lower operating speeds contribute to maintaining suction pressure above the vapor pressure of the liquid being pumped. This process reduces pressure drops within the pump, helping to reduce or prevent cavitation.
Diaphragm movement optimization: Selecting a diaphragm pump with a smaller eccentric offers another possibility for cavitation prevention. By minimizing the diaphragm's movement during pump operation, this design reduces the occurrence of pressure fluctuations that can cause cavitation. Notably, this feature benefits applications where precise fluid handling is essential, ensuring stable and reliable pump performance while minimizing the risk of cavitation issues. However, using a smaller eccentric will also lead to reduced pressure and flow rate performance.
By implementing these preventive measures, industries can minimize the detrimental effects of cavitation increases on pump performance and ensure the reliable operation of liquid systems. However, bespoke pump designs offer a custom approach to help avoid cavitation damage by addressing specific end-user requirements and effectively minimizing cavitation risks.
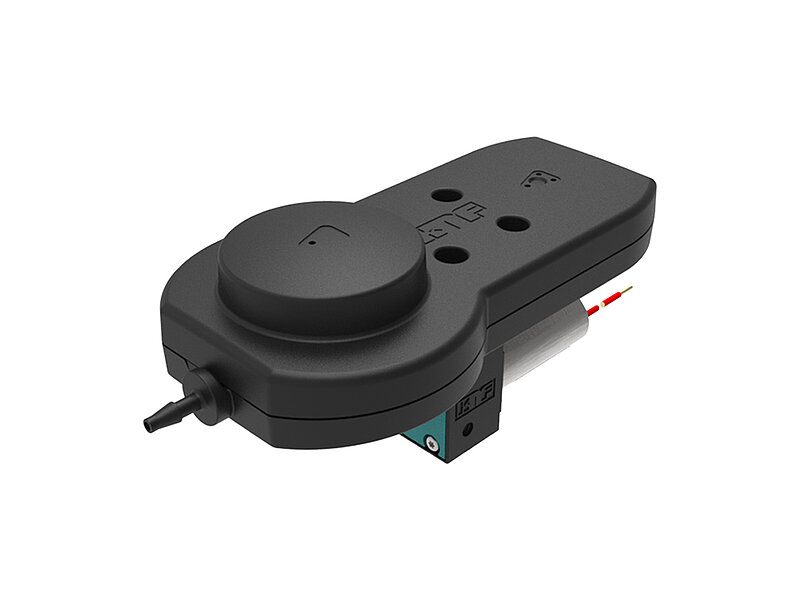
Superior Design and Technology by KNF
As the technology leader in diaphragm pump technology, KNF uses a superior modular design concept, advanced technology, and quality engineering to ensure fully customizable, durable, and user-friendly pumps that perform optimally while preventing pump cavitation risks in almost all application-specific pumping systems.
KNF prioritizes precise pump sizing to match specific application requirements. By accurately determining flow rates, fluid pressure conditions, and fluid properties, KNF ensures that pumps can operate within optimal parameters, reducing the likelihood of cavitation while maximizing the efficiency and reliability of the pump system.
Pump Cavitation Knowledge From KNF
Understanding pump cavitation is vital to maintaining fluid system efficiency. Prioritizing high-quality fluid handling practices, including proper pump sizing, material selection, and regular maintenance, is essential. By implementing these strategies, industries can minimize cavitation-related issues and ensure the reliable operation of fluid systems over the long term.
KNF pumps use state-of-the-art advanced engineering, design, and technology to mitigate cavitation risks effectively. However, while KNF pumps do not suffer damage by cavitation, sensitive liquids, and vapor pressure can be affected. As a manufacturer of high-quality positive displacement pumps, our KNF experts have the knowledge and experience to help all customers better understand pump cavitation, its effects, and how to minimize them for specific applications.
If you have questions or need technical advice for your pump system, contact us today.
75 Years: KNF Celebrates Company Anniversary
A treasure chest filled with memories, facts and stories. Learn more about KNF’s company history.
