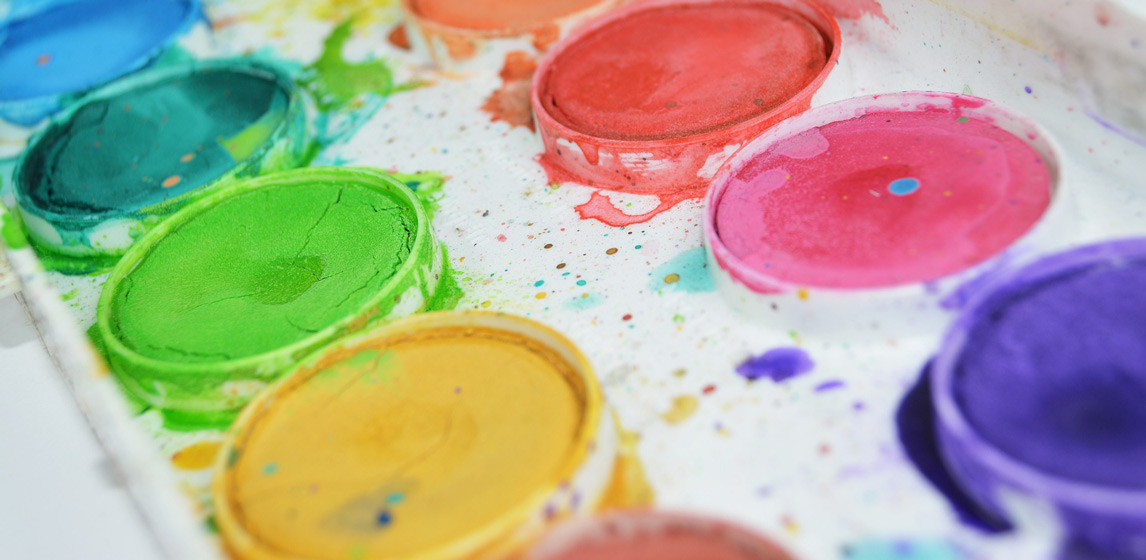
Water Moves to the Front in Inkjet Printing
Water-based ink technology is advancing. There are two main reasons for this development: the common solvent-based inks contain many volatile organic compounds (VOC) which are environmentally harmful and can cause health issues for employees both during manufacturing and printing. Therefore, in many countries, such as China, fines are levied for VOC emissions. That is one reason, why ink and printer manufacturers increasingly turn to water-based inks which leads to new research among manufacturers of printer components – such as the pump.
Using water-based ink, the curing process is one of the greatest challenges
In addition to the environmental aspect, there are several functional reasons favoring the new ink. Water-based ink is ideal for all applications where the substrates are porous, such as food packaging – such as cardboard and corrugated cardboard – or textiles. In these applications, the curing process, the greatest challenge for water-based inks, is well-supported because the water is absorbed by the porous material and the pigments remain at the surface. The result is an excellent image quality.
One major challenge is printing on non-porous substrates, such as foil. If the ink does not dry quickly enough, the colors mingle and create fuzzy, blurred images. By using special additives in the water-based inks the curing process can be improved. Thus, it is now possible, to print on flexible food packaging using water-based ink (e.g. for pasta packaging).
The result of this robust ink layer on the flexible substrate is presentable and cheaper than printing with solvent-based ink, with the added benefit of being environmentally friendly.
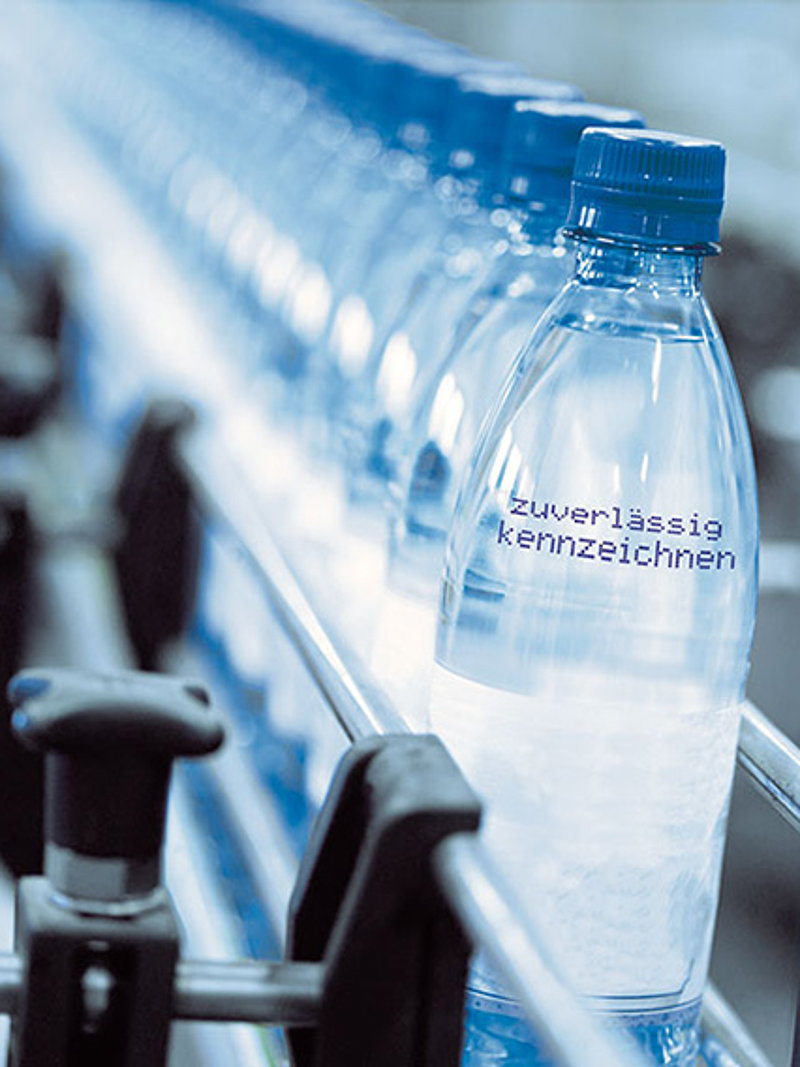
When abrasive material is created by the internal printing equipment components, it could damage the ink and compromise the results
The use of water-based inks places greater demands than ever on the printer components, in particularly the pumps. These pumps ensure a readily available supply of ink through a system of vacuum and pressure.
Unlike oil-based inks, water-based inks do not provide lubrication within the pump. Therefore, all pump types with moving mechanical seals, such as gear pumps and piston, could be damaged by transporting water-based ink. With a lack of lubrication, abrasion and heat build-up, the pump starts leaking and may stop working. The pump malfunction may cause the properties of the precisely “formulated” ink to change and due to the heat generated, the curing process may even be triggered early. In a diaphragm pump, all these risks are reduced. Its functionality does not require a mechanical seal and it can therefore be safely run dry without creating dangerous abrasive materials.
Although called water-based inks, many inks still contain chemicals required to improve the curing process. Engineers consider the chemical resistance of the available pump material combinations to achieve the best pump configuration for the inks available on the market. Extensive testing and customer knowledge contribute to the creation of the best pump for the specific application.
Water-based inks often are prone to air bubbles in the ink. The diaphragm pump, when optimized for vacuum, is ideal for “degassing” the ink, a term for removing unnecessary air from the ink. When transferring the ink, due to the lack of a mechanical seal, only minor mechanical forces are exerted onto the ink thus reducing cavitation and eliminating the cause of air bubbles. The diaphragm pump works with a “massaging” movement, like the heart when transporting blood. Conversely, gear pumps create a rather crushing movement and the resulting shear forces lead to greater stress on the ink.
In summary, diaphragm pumps offer numerous advantages when using water-based ink and can make the printing process stable, safe and durable.
75 Years: KNF Celebrates Company Anniversary
A treasure chest filled with memories, facts and stories. Learn more about KNF’s company history.
Anniversary Blog