The coffee machine manufacturer Eversys relies on KNF solutions for perfect milk foam
Ultra-Clean Supply Pumps and Return Pumps for the Semiconductor Industry
KNF develops extreme pumps for extreme conditions in close cooperation with Canon Nanotechnologies, Inc.
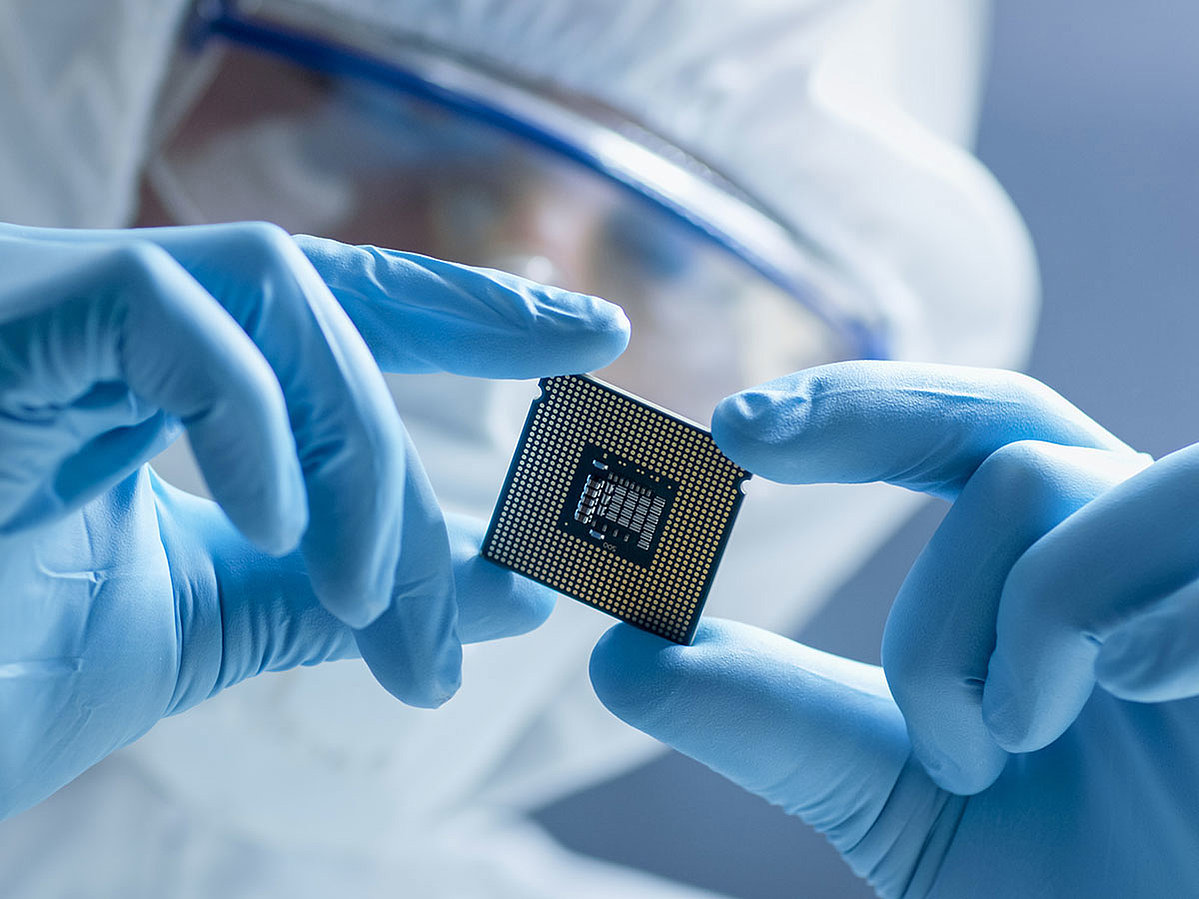
Supply pumps and return pumps by KNF play an important role in the semiconductor industry. In close cooperation with Canon Nanotechnologies, Inc., KNF has developed a custom-made pump that fulfills the extremely high demands of this industry. Utilizing a special ionization-resistant material, KNF was able to provide extremely clean pumps for handling ultra-pure fluids that also require little maintenance and allow for economic operation.
Microelectronics have come a long way. Computers from past decades filled entire rooms and cost a fortune but are today exceeded in terms of computing power by everyday consumer electronics like smartphones or tablet computers. This development is based on a number of technological advancements. The downsizing of semiconductors is undoubtedly one of the most important ones. Within the semiconductor industry, Canon Nanotechnologies is the market and technology leader for high-resolution, low cost-of-ownership nanoimprint lithography systems. Here, special pumps by KNF play an important role.
Dispensing process for silicon wafer
The special imprint process is developed by Canon Nanotechnologies. During this process, arrays of small drops of fluid are placed precisely and directly onto a silicon wafer. This dispensing process can be compared to inkjet dispensing. In the next step, a transparent template is placed directly onto the fluid. Due to its optimized viscosity, the liquid then fills capillaries in the glass creating the desired pattern. With the use of UV light, the liquid cures and remains hardened on the silicon wafer.
Compared to the conventional lithography process for a semiconductor device, this process offers several advantages. Normally, the photo resist is spun onto the wafer and then a photomask is used to create the desired pattern. However, the usage of a conventional photomask poses optical limitations to the size of the produced nanostructure. Plus, the spin coating process causes a lot of waste by spinning off >99% of the photo resist.
When standard supply and return pumps are not enough
By eliminating spin coating and by establishing the careful and controlled placement of arrays of drops, the process by Canon Nanotechnologies requires pumps that transport the fluid within the system. As handling the fluid requires special precautions and as the entire process takes place under extremely clean conditions, the components used in this process require much care. This is especially true for the pumps involved. In total, the process relies on several pumps. While a supply pump and a return pump deliver and return the fluid to the dispensing head, a fill pump and a drain pump deliver fluid to and drain fluid from a reservoir tank.
Before KNF pumps were used for these tasks, Canon Nanotechnologies relied on centrifugal pumps made entirely of PTFE. But not only were they rather expensive, they also did not meet the specific performance requirements. Not content with the status quo Canon Nanotechnologies searched for a reliable partner to develop a pump system that better aligned with their needs. Finally, they found what they were looking for in KNF. This was the starting point of a long-standing close relationship between the two companies.
Searching for the best pump material possible
Searching for the ideal supply pump and return pump, diaphragm pumps quickly evolved as the solution of choice. Being extremely reliable and requiring minimal maintenance, this pump type also moves fluids in a very gentle, clean, and safe manner. In addition, with diaphragm pumps from KNF, the desired low but steady flow rate needed for the process could be achieved. The compact build was another considerable advantage.
KNF started searching for the ideal pump build material. Most importantly, the material needed to be completely ion-free. Also, it had to be extremely clean since even particles as small as sub 20nm can destroy the pattern. These extreme requirements narrowed the choice down to PCTFE. While its properties were excellent on paper, it was not a standard material used by KNF. “We are extremely careful when selecting new materials,” explains Paul Shaver, Director of Sales and MARCOM at Canon Nanotechnologies. KNF, therefore, sent material samples to Canon Nanotechnologies for rigorous testing, ultimately resulting in the approval of the new material.
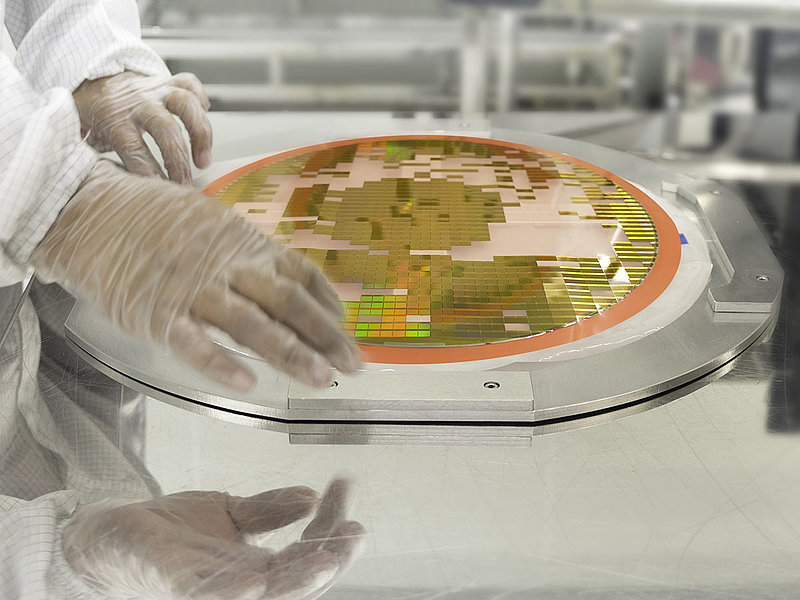
Modular design enables quick customization
KNF developed an optimized solution, meeting Canon Nanotechnologies’ requirements, using PCTFE for the improved pump head. Building upon KNF’s diaphragm technology expertise, KNF was able to ensure that the wetted path of the fluid was free of ionization as well. KNF understands that one size doesn’t fit all. The unique modular design of our solutions allows our engineers to assemble each pump from individual key components. KNF always collaborates closely with our customers throughout the entire development process – from the initial idea to the final result – to create the smartest solution for each specific application.
New supply and return pumps increased reliability while reducing costs
The custom-made KNF supply and return pumps soon proved their advantages over the previously used pumps. The pumps increased performance, in terms of cleanliness and flow rate, made the process more reliable and therefore cost-effective. Another significant advantage was that the new pumps offer the same (if not better) reliability than the previous design. Improved reliability is a significant factor since the process takes place under extremely clean conditions, making maintenance difficult, time-consuming, and therefore costly. “Maximizing uptime is a key advantage of our equipment,” summarizes Paul Shaver on production requirements. For customers of Canon Nanotechnologies, these gains directly translate into a lowered cost of ownership.
Decades of expertise gained in successful collaboration with leading manufacturers in a broad range of markets enables KNF to understand and deliver the components required to meet these cutting-edge applications. Our KNF experts are happy to answer your questions regarding your specific application. Get in touch.