The best model for technology is the natural world. The heart is the mother of all pumps, and the lungs are effective compressors. Many thousands of years ago and by mere coincidence, humans managed to take their operating principles and apply them. It was the Egyptians who discovered the effectiveness of filling an animal hide bag with air and then releasing it to keep the embers from a fire glowing instead of constantly fanning them. In fact, the bellows seen in ancient murals is the first known human-made compressor in history.
The early inhabitants of Alexandria also knew what could be achieved with compressed air or water pressure alone. Impressive feats of engineering were invented there, such as Heron’s fountain, whose water flows almost endlessly as if by magic. While the fountain was nice to look at, it wasn’t until the era of the steam engine that the compressor offered a clear added benefit. And that may be an understatement – after all steam engines transformed the world.
The high-pressure steam engine developed by Denis Papin in 1690 was the first propulsion technology that drove a compressor to compress air and other gases without relying on muscle power. In the 18th century, steam engines were initially used in coal mining and later in the textile industry. Gradually they replaced watermills and windmills. Since the 20th century, compressors have proven indispensable in just about every industry. Over time, there was a demand for this technology to be updated for medicine and laboratory science in order to address the main disadvantage of piston or rotating compressors, which is that their drives must be continually lubricated. As a result, the transported air is not oil-free.

This prompted the development of the diaphragm compressor in the 1940s. With each down stroke the diaphragm pulls in air or liquids, and with each up stroke it pushes the medium into the outlet pipe. An intake and an output valve ensure that the direction of transfer is always the same. An eccentric connecting rod typically couples the diaphragm with an electric motor which drives the whole process. The diaphragm pump offers major advantages in that it requires no maintenance or lubrication and the transported air remains completely oil-free, since the medium compression chamber and drive mechanism are separated. The disadvantages are the diaphragm’s limited service life and low performance capacity. But in the 1960s, KNF embraced the diaphragm pump and began to refine it further.
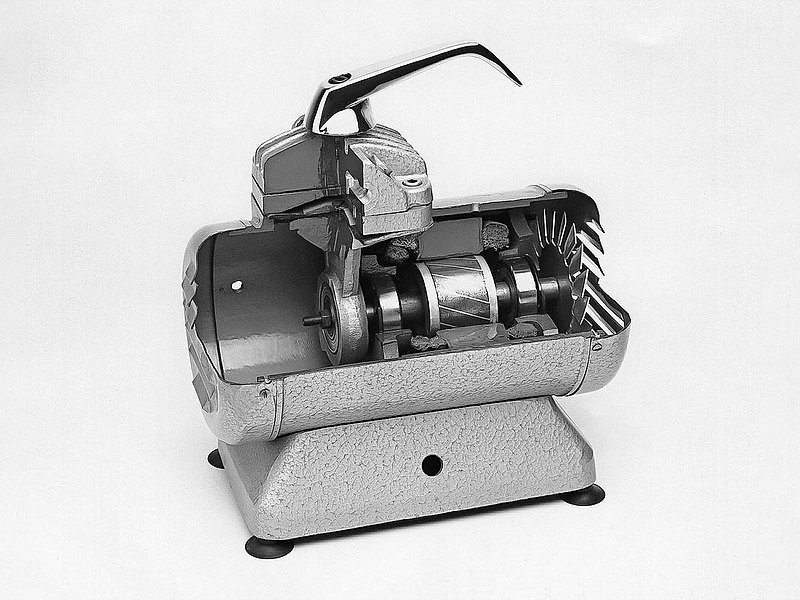

After months of experimentation and tirelessly running trial after trial, the company succeeded in better coordinating the pump and the connecting rod. This alleviated the stress on the diaphragm, thus increasing its service life. Improvements were seen in the maximum pressure of the vacuum as well. In 1966, Kurt Neuberger KG acquired its first patent. From then on, it was just a stream of further inventions and patents.
Today, KNF pumps are used in a broad range of sectors all over the world. They can be found in the food service industry, where they ensure that professional-grade coffeemakers froth milk properly. They recycle stale air on the International Space Station (ISS). And they are a critical component of many of the ventilators currently being used to save the lives of COVID-19 patients.