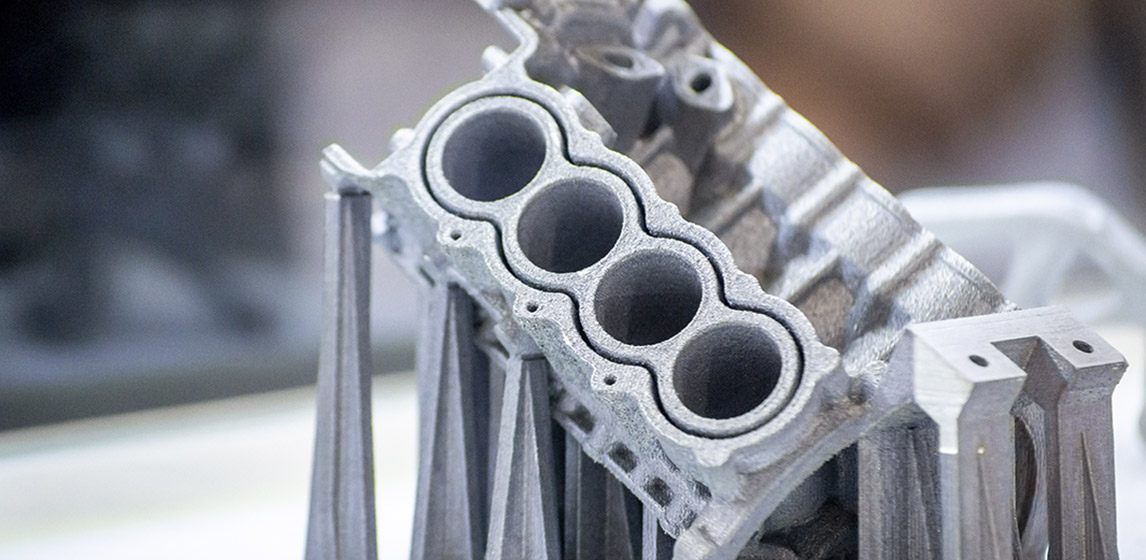
Du prototype à la production en série
Initialement développée en vue d’accélérer la fabrication de prototypes, l’impression 3D s’avère désormais être un procédé fiable pour la production à grande échelle. Ce n’est que récemment que les fabricants ont envisagé l’impression 3D comme étant une alternative aux méthodes de production conventionnelles en raison des améliorations en matière de vitesse de production, d’intégrité structurelle et de coûts. Le Metal Binder Jetting (MBJ) ouvre désormais de nouvelles voies quant à l’utilisation de l’impression 3D au sein des industries qui ont besoin de produire en grand volume. Dans l’article de blog suivant, vous en apprendrez davantage sur l’histoire du procédé Metal Binder Jetting et sur le rôle essentiel joué par les pompes à membrane KNF.
Développement récent de l’impression 3D
La nouvelle tendance est au développement de l’impression 3D bien au-delà de la fabrication à petite échelle. Elle s’étend désormais à la production en série. Le nombre en croissance constante des acteurs du secteur de la fabrication additive peut expliquer cette tendance. Avec pour objectif commun d’industrialiser l’impression 3D, ces entreprises ont été à l’origine d’innovations dans le développement du matériel d’impression. Ceci a permis de mettre au point des systèmes d’impression 3D plus sophistiqués à un prix abordable pour les fabricants. Parmi les nombreuses technologies disponibles ayant fait leurs preuves, le Metal Binder Jetting a récemment attiré l’attention de l’industrie.
Tendance : Le Metal Binder Jetting
Le Metal Binder Jetting est en train de devenir l’une des technologies incontournables de l’impression 3D métal. Les vitesses d’impression élevées et la production de composants complexes constituent les précieux facteurs de différenciation de cette technologie. Un nombre croissant d’entreprises ont reconnu le potentiel de Metal Binder Jetting et travaillent intensément pour tirer parti des possibilités qu’elle offre. Le Metal Binder Jetting offre une alternative rapide et rentable en matière de fabrication additive aux fabricants d’applications actuellement irréalisables par des technologies d’impression 3D métal. Il s’agit d’une évolution importante, en particulier pour les applications telles que le prototypage médical, la production automobile, ainsi que dans la dentisterie et autres fabrications diverses. Les entreprises de ces secteurs peuvent désormais se permettre d’imprimer leurs propres composants, ce qui leur épargne des coûts de fabrication élevés de leurs équipements spécialisés.
Comment fonctionne « le Metal Binder Jetting » ?
Dans le processus du Metal Binder Jetting, des couches de métal en poudre sont jointes par le dépôt sélectif d’un liant liquide. Alors que d’autres techniques additives utilisent une source de chaleur pour lier les matériaux entre eux, le Metal Binder Jetting ne dépend pas de la chaleur lors du processus initial de construction. Le processus commence par la répartition d’une fine couche de poudre métallique tout en utilisant des têtes d’impression dirigées vers des gouttelettes de liant injectées dans le lit de poudre. Une nouvelle couche de métal en poudre est déposée sur le dessus, encore et encore, jusqu’à ce que l’objet soit terminé. Cela peut servir à imprimer une grande pièce, ou un ensemble de pièces empilées les unes sur les autres.
Avec l’amélioration de la technologie et l’augmentation des vitesses, l’acheminement du liant à la tête d’impression n’a jamais été aussi important. Le placement précis du liant sur chaque couche est essentiel pour maintenir l’intégrité de la pièce finale.
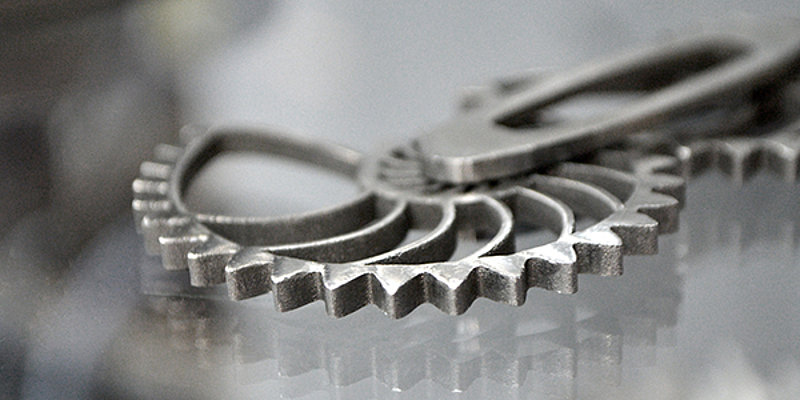
À quel moment les pompes KNF entrent-elles en jeu
L’utilisation du Metal Binder Jetting peut sembler simple, mais les fabricants de matériel d’impression s’attachent aux détails pour garantir des résultats optimaux ; cela inclut également le bon choix des composants pour leur équipement. Les pompes à membrane pour gaz et liquides KNF se sont révélées être des composants fiables pour toute une série de fonctions dans le cadre du processus d’injection de liant sur lit de poudre. Cela comprend la recirculation, le dégazage et le transfert du liant liquide, ainsi que le remplissage ou l’évacuation du liquide de démoulage pendant le processus de post-impression. Lors du transfert du liant vers la barre d’impression, les pompes KNF assurent un débit régulier avec de faibles pulsations afin de réduire la cavitation et la formation de bulles d’air dans le support.
KNF a développé une nouvelle série FP et FK de pompes à membrane pour liquide à faible pulsation ciblant ces types d’applications d’impression. En outre, KNF répond individuellement aux besoins de ses clients dans le domaine de l’impression de fabrication additive en adaptant leurs pompes standard à chaque projet. Les clients bénéficient de la flexibilité grâce à une gamme de matériaux, de moteurs et d’options de connexion mécanique, y compris des options pour porter des substances agressives à des températures élevées.
Garder l’avenir en ligne de mire
À l’avenir, les fabricants de matériel d’impression continueront à perfectionner le Metal Binder Jetting, ce qui stimulera l’innovation dans le développement de matériel d’impression 3D. En fin de compte, la technologie pourra ainsi gagner une part précieuse du marché manufacturier global. Dans ce processus, KNF se tient aux côtés de ses clients, en proposant des solutions de pompes sur mesure, offrant à la fois la longévité, la résistance chimique et la précision de fonctionnement.
75 ans : KNF célèbre l'anniversaire de son entreprise
Un coffre à trésors rempli de souvenirs, de faits marquants et d’histoires. En savoir plus sur l’histoire de la société KNF.
