Les pompes KNF recyclent l'air à bord de l'ISS
Les pompes KNF pour l’impression 3D au sable
Le Smart Slab développé par les chercheurs de l’EPF de Zurich dans le cadre d’un projet architectural innovant
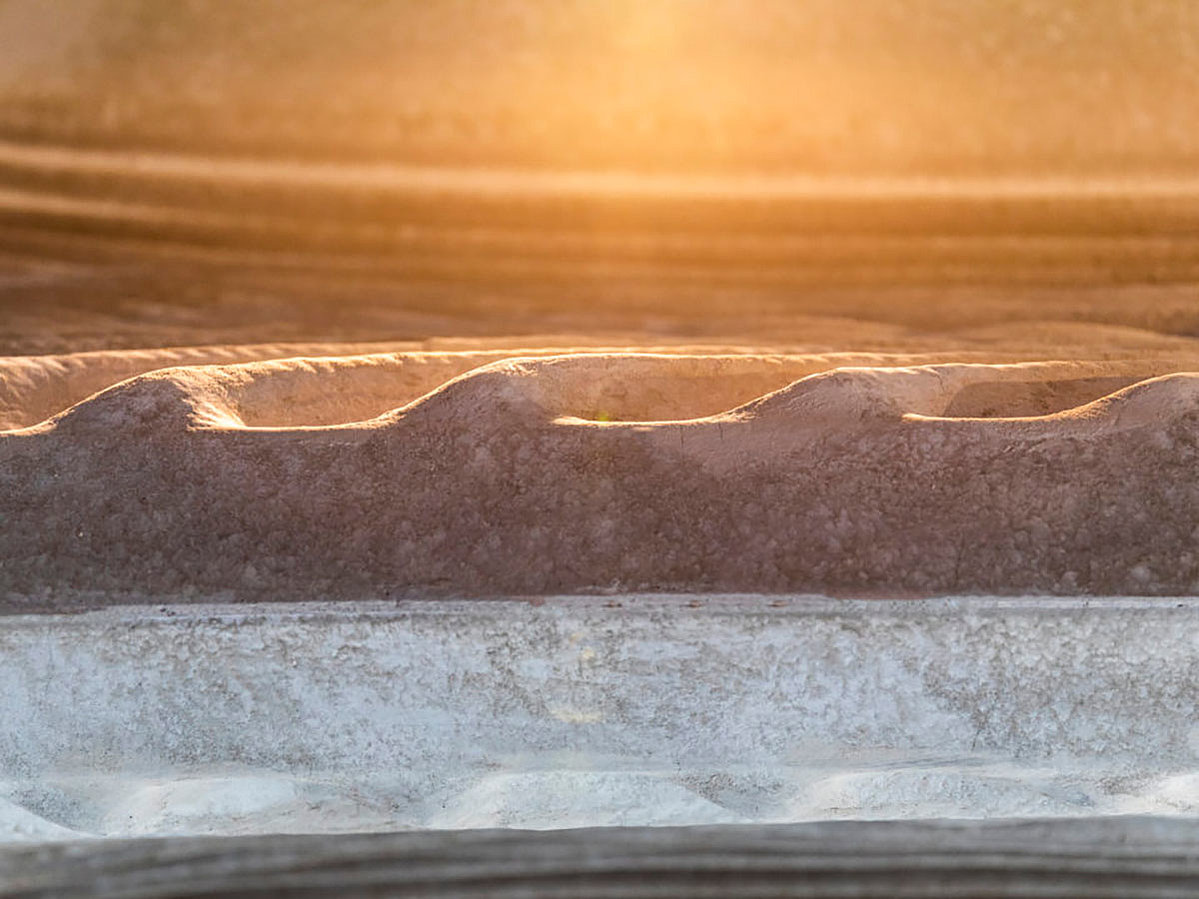
Les chercheurs de l’EPF de Zurich fabriquent un plafond en béton léger et intelligent dans le cadre du projet architectural Smart Slab. L’université suisse utilise une méthode de fabrication innovante pour créer le coffrage de la dalle à l’aide d’une imprimante 3D au sable de l’entreprise Voxeljet AG basée à Friedberg en Allemagne. L’imprimante est équipée de pompes KNF.
Les avantages de la production numérique
Le plafond intelligent Smart Slab associe les avantages structurels du béton et la liberté de création de l’impression 3D. Cette méthode de production numérique est bien plus économique et écologique que la construction de plafonds massifs. En son point le plus fin, le Smart Slab mesure à peine 20 millimètres sans perdre de sa stabilité. Il pèse 50 % de moins qu’un plafond conventionnel, d’où une consommation de matériau moindre. Cela fait baisser les coûts de fabrication et diminue l’empreinte carbone.
Les origines du projet
Le Smart Slab a été développé à l’EPF de Zurich sous la direction de Benjamin Dillenburger, maître de conférences en technologies de construction numériques. Il s’agit d’un des éléments clés de l’unité d’habitation DFAB House. Il a été installé à l’été 2018 dans le bâtiment de recherche et d’innovation NEST de l’EMPA (Laboratoire fédéral d’essai des matériaux et de recherche) et de l’EAWAG (Institut fédéral de recherche sur l’eau) à Dübendorf. Le plafond d’une surface de 80 m2 pour un poids de 15 tonnes se compose de onze segments en béton qui relient le sous-sol à la structure supérieure en bois à deux niveaux.
Aussi peu de béton que possible
Les chercheurs du projet Smart Slab ont utilisé l’impression 3D pour fabriquer non pas les éléments de construction eux-mêmes, mais le coffrage, autrement dit l’empreinte négative. Ils ont travaillé avec une imprimante 3D au sable grand format de Voxeljet. Celle-ci comprend deux pompes à membrane pour liquides KNF, l’une étant chargée de fournir le liant froid (NF 60 KT DC) et l’autre d’éliminer le matériau brut excédentaire (NF 60 KT DC). La fabrication du coffrage est l’étape qui demande le plus de travail dans la construction en béton, notamment pour les composants non standards.
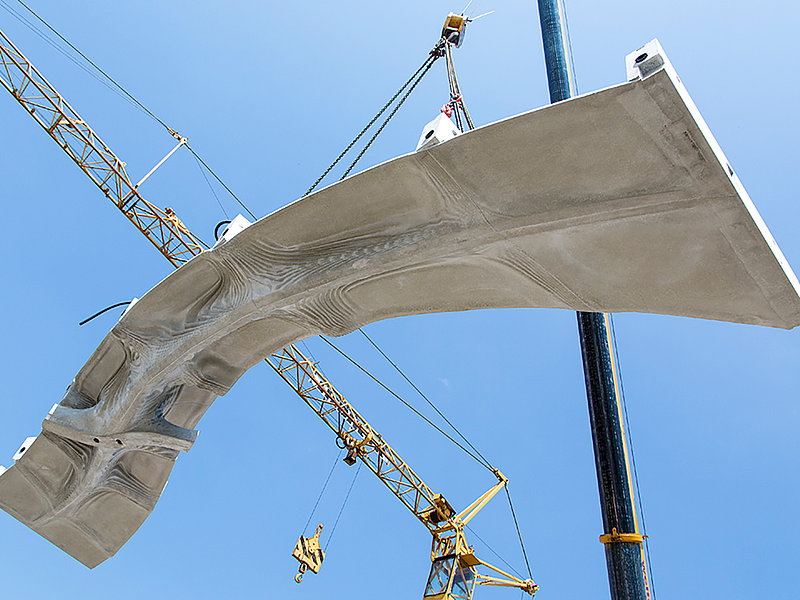
Fabrication d’une simple pression sur un bouton
Une fois la conception sur ordinateur terminée, les partenaires industriels des chercheurs de Smart Slab sont passés à l’action. L’un a produit le coffrage avec une imprimante 3D au sable haute résolution, alors que l’autre a utilisé des découpeuses laser CNC pour créer le coffrage en bois. Cela donne sa forme à la face supérieure du Smart Slab et prévoit aussi des cavités pour réduire la quantité de matériau employé, alléger la structure et faire de la place aux fils électriques. Les deux types de coffrage ont ensuite été réunis par la troisième entreprise partenaire pour le bétonnage. Elle a tout d’abord injecté le béton fibré dans le coffrage imprimé au sable afin de produire la surface finement striée de la coque inférieure en béton, puis elle a coulé le reste du Smart Slab à l’aide du coffrage en bois.
Des résultats impressionnants grâce à la planification en amont
Après deux semaines de prise, les onze segments individuels en béton étaient prêts à être transportés à la DFAB House. La planification et la préfabrication méticuleuses ainsi que le choix de partenaires spécialisés et de technologies fiables ont permis la réalisation du projet sans retard. « Ce fut très impressionnant de voir sur le chantier à quel point nos éléments s’imbriquaient parfaitement entre eux et avec les composants existants de la DFAB House, se souvient Benjamin Dillenburger. Cette réussite n’aurait pas été possible sans l’excellente coopération interdisciplinaire avec nos partenaires. »