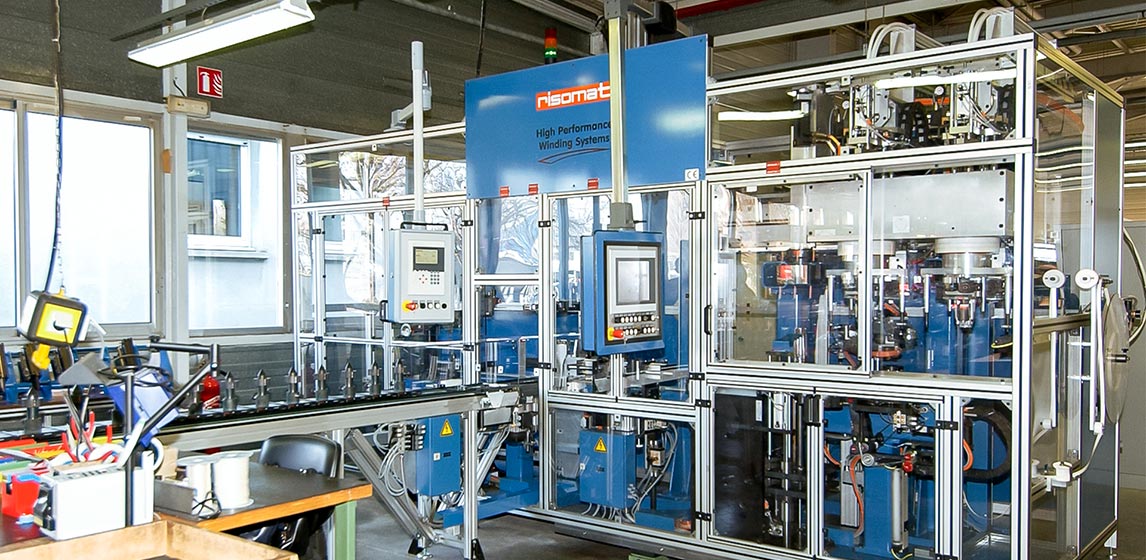
Les moteurs KNF
Les pompes ne peuvent pas fonctionner sans système d’entraînement. Celui-ci doit si possible être flexible, sans défaut et durer longtemps. Ainsi, depuis le début de la fabrication des pompes et compresseurs à membrane, des moteurs électriques sont utilisés. Dès les années 70, KNF les produit en France pour l’ensemble du groupe. Pour des raisons tout à fait pratiques, KNF a décidé de développer ses propres compétences dans le domaine des moteurs. En effet, les prix de référence pour les petites quantités requises sont trop élevés, ou bien, il est tout simplement difficile d’obtenir des moteurs en petite quantité. KNF France fabrique des bobines, des stators et des moteurs. Le « stator » désigne la partie fixe du moteur, y compris le carter. Au début, tout doit être fabriqué manuellement et 15 à 20 minutes sont nécessaires pour obtenir un seul stator.
En 1993, la première machine de frettage permet de maintenir ensemble les têtes de bobine en haut et en bas ; l’année 2000 marque l’arrivée de la première machine à enrouler les bobines de fil. En 2003, après trois années de planification conceptuelle, le centre de bobinage entre en service. La machine gigantesque fonctionne 18 heures par jour et produit toutes les minutes des stators de qualité constante. Ainsi, par une simple pression sur un bouton, 400 enroulements différents de 6 tailles et 30 diamètres de fils possibles sont fabriqués. Par rapport à la modification compliquée dans le cas d’un changement de modèle, cela représente une grande avancée : le centre de bobinage est quant à lui adapté en moins d’une heure. Cela signifie que les pièces ne doivent plus être fabriquées en plus grand nombre que nécessaire et stockées. Le réglage du système d’entraînement en fonction des besoins du client ne pose aucun problème, la production est plus efficace et plus flexible même en cas de petites quantités.

Le moteur sans balais présente de nombreux avantages. Il peut être parfaitement réglé de façon électronique. Il est compact, puissant et très efficace en matière d’énergie. De plus, sa durée de vie est longue. Il réunit les avantages d’un moteur à courant alternatif et d’un moteur à courant continu conventionnel. La priorité de l’équipe chargée des moteurs chez KNF est actuellement le moteur digital sans balais.
Digital Customization signifie que la nouvelle génération de moteurs est personnalisable. Elle peut être adaptée de façon flexible aux exigences spécifiques, et ce, si nécessaire, par l’utilisateur lui-même ! La capacité de paramétrage des moteurs est unique. L’utilisateur est tout à fait libre de créer les profils de fonctionnement pour les pompes à membrane, de façon extrêmement complexe et tout à fait individuelle. Digital Customization permet de commander simplement les signaux numériques par une gestion précise des valeurs cibles. Par exemple, une panne survient. D’ordinaire, la pompe se désactive. Mais en raison de la programmation de la pompe, une stratégie alternative est choisie. La pompe adapte son comportement à la source de perturbation qu’elle compense. L’appareil reste en fonctionnement. Le débit de la pompe peut par exemple être défini en tant que valeur cible non modifiable, de sorte que cette valeur cible soit ensuite atteinte, indépendamment du comportement technique.
KNF Blog Knowledge Flows
Suivez les dernières tendances sur la façon dont la technologie des pompes à membrane fait évoluer le marché.
