Le pompe KNF riciclano l'aria a bordo dell’SSI
Pompe KNF per stampa 3D a sabbia
Smart Slab è stato sviluppato in un progetto architettonico innovativo dai ricercatori del Politecnico ETH di Zurigo.
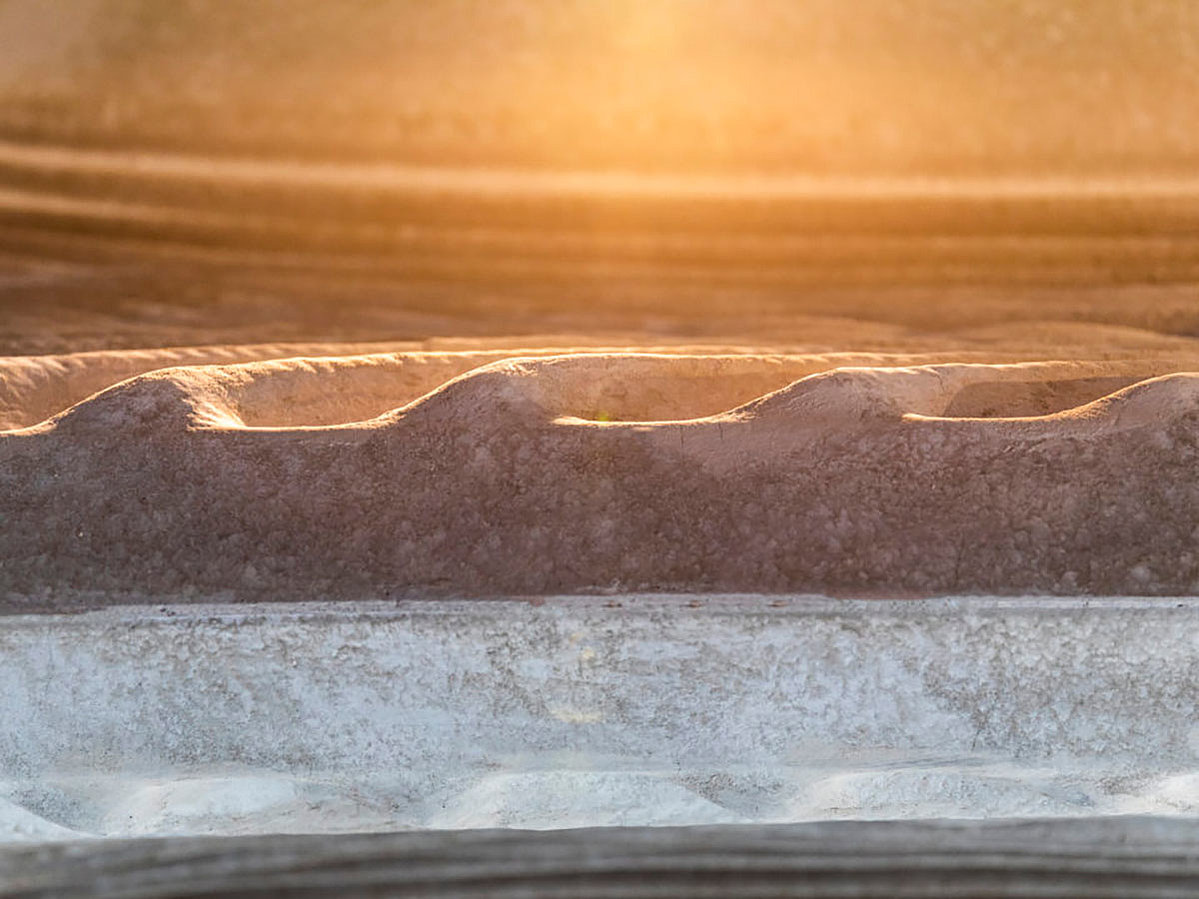
I ricercatori del Politecnico di Zurigo stanno realizzando un soffitto in cemento leggero intelligente nell'ambito del progetto architettonico Smart Slab. Per creare la cassaforma del pannello, l'università svizzera utilizza un metodo di produzione innovativo con una stampante 3D a sabbia della Voxeljet AG di Friedberg (Germania), dotata di pompe KNF.
I vantaggi della produzione digitale
Il soffitto intelligente Smart Slab combina la resistenza strutturale del cemento con le flessibili possibilità di progettazione della stampa 3D. Questo metodo di produzione digitale è molto più efficiente in termini di costi e rispettoso dell'ambiente rispetto alla costruzione di soffitti tradizionali. Nel suo punto più sottile, il pannello Smart Slab misura appena 20 millimetri, senza compromessi in termini di stabilità. Ciò significa che l’ago della bilancia indica un peso inferiore al 50 % rispetto a un soffitto convenzionale, con conseguente minor consumo di materiale, riduzione dei costi di produzione, ma anche dell'impronta di carbonio.
Le radici del progetto
Lo Smart Slab è stato sviluppato al Politecnico di Zurigo sotto la guida di Benjamin Dillenburger, Assistant Professor in tecnologie digitali di costruzione. Rappresenta uno degli elementi centrali dell'unità residenziale DFAB House ed è stato installato nell'edificio di ricerca e innovazione NEST dell'Empa e dell'Eawag a Dübendorf nell'estate del 2018. Composto da undici segmenti in cemento che collegano il piano inferiore con la struttura in legno a due piani sovrastante, il soffitto misura 80 metri quadrati e pesa 15 tonnellate.
Meno cemento possibile
I ricercatori Smart Slab hanno utilizzato la stampa 3D per produrre non gli elementi costruttivi in sé, ma la loro cassaforma, ovvero lo stampo negativo. Hanno lavorato con una stampante 3D a sabbia di grande formato della Voxeljet. Essa contiene due pompe per liquidi a membrana KNF, una garantisce l'alimentazione del legante freddo (NF 60 KT DC IP65) mentre l'altra rimuove la materia prima in eccesso (NF 60 KT DC). La produzione della cassaforma è la fase più impegnativa nella costruzione di cemento, soprattutto per i componenti non standard.
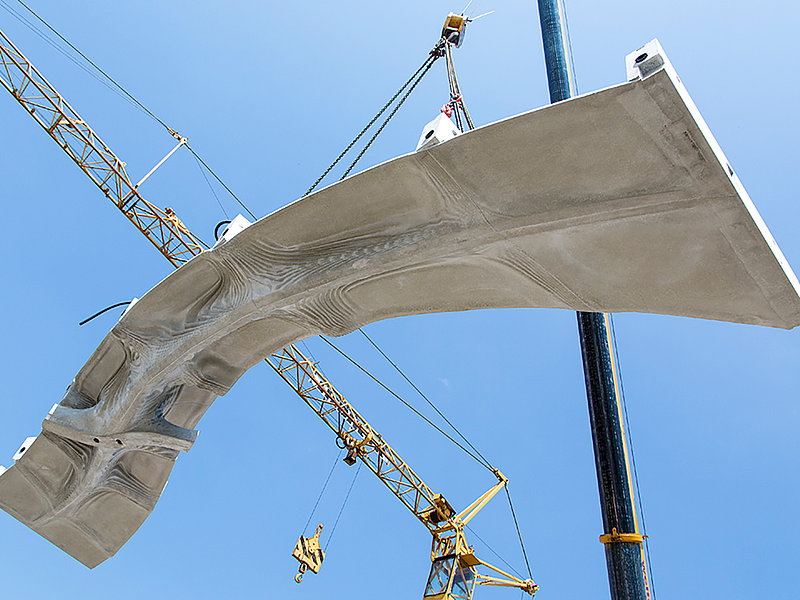
Per produrre basta premere un pulsante
Dopo il completamento della progettazione a computer, i partner industriali dei ricercatori Smart Slab sono entrati in azione. Uno ha prodotto la cassaforma in sabbia pressata 3D ad alta risoluzione, mentre un altro ha utilizzato frese laser CNC per creare la cassaforma in legno. Quest’ultima dà la forma al lato superiore della Smart Slab e comprende anche delle cavità per ridurre l'uso e il peso del materiale e per alloggiare i cavi elettrici. I due tipi di casseforme sono poi stati riuniti dalla terza azienda partner, che prima ha iniettato il calcestruzzo fibrorinforzato nella cassaforma in sabbia per produrre la superficie finemente nervata del guscio inferiore in calcestruzzo e poi ha colato il resto del calcestruzzo della Smart Slab utilizzando la cassaforma in legno.
Ottimi risultati grazie alla pre-progettazione
Dopo due settimane di indurimento, gli undici singoli segmenti di calcestruzzo erano pronti per il trasporto alla DFAB House. La meticolosa pianificazione e pre-fabbricazione, così come la scelta di partner esperti e di tecnologie affidabili, hanno permesso di completare il progetto con successo e senza ritardi. “È stato spettacolare vedere sul cantiere come i nostri elementi si integrano perfettamente tra loro e con i componenti esistenti della DFAB House”, ha affermato Dillenburger. “Dobbiamo questo in parte alla straordinaria collaborazione interdisciplinare con i nostri partner.”