KNF pumps recycle air on board of the ISS
KNF Pumps in 3D Sand Printing
Smart Slab developed in an innovative architectural project by researchers at ETH Zurich
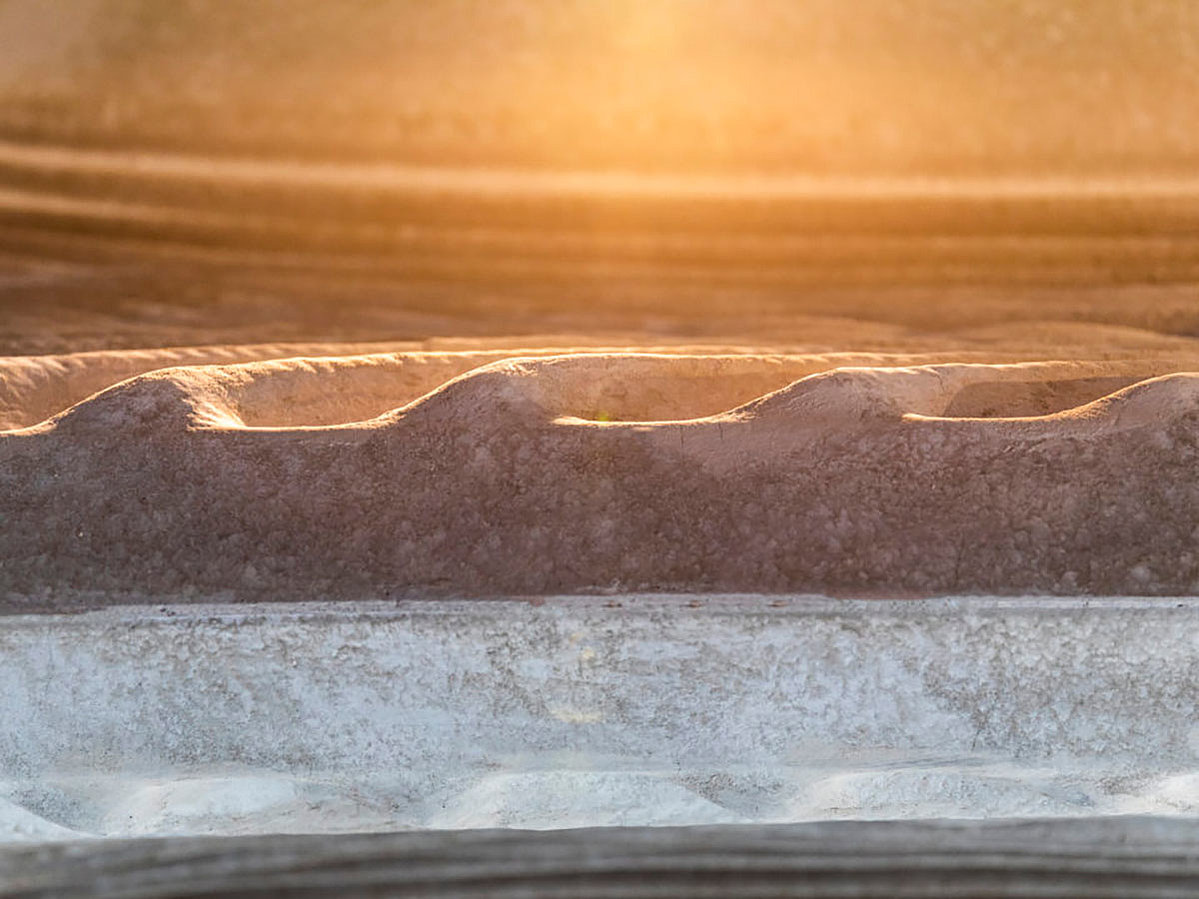
Researchers at ETH Zurich are producing a lightweight, intelligent concrete ceiling as part of the Smart Slab architectural project. The Swiss university is using an innovative manufacturing method to create the slab’s formwork with a 3D sand printer from Voxeljet AG, Friedberg (Germany), fitted with KNF pumps.
The benefits of digital production
The Smart Slab intelligent ceiling combines the structural strengths of concrete with the flexible design possibilities of 3D printing. This digital production method is much more cost-efficient and environmentally friendly than the construction of solid ceilings. At its thinnest, the Smart Slab measures just 20 millimeters, without losing any stability. This means it tips the scales at less than 50 percent of the weight of a conventional ceiling, resulting in lower material consumption – which not only cuts manufacturing costs but also makes for a smaller carbon footprint.
The roots of the project
The Smart Slab was developed at ETH Zurich under the instruction of Benjamin Dillenburger, assistant professor for digital construction technologies. It is one of the core elements of the DFAB House residential unit and was installed in the NEST research and innovation building of Empa and Eawag in Dübendorf in summer 2018. Consisting of eleven concrete segments which connect the basement with the two-story wooden structure above, the ceiling measures 80 m2 and weighs 15 metric tons.
As little concrete as possible
The Smart Slab researchers used 3D printing to produce not the construction elements themselves, but their formwork – i.e. the negative mold. They worked with a large-format 3D sand printer from Voxeljet. This contains two KNF membrane liquid pumps, each of which is responsible for supplying cold binder (NF 60 KT DC) and removing excess raw material (NF 60 KT DC). The production of the formwork is the most labor-intensive step in concrete construction, especially for non-standard components.
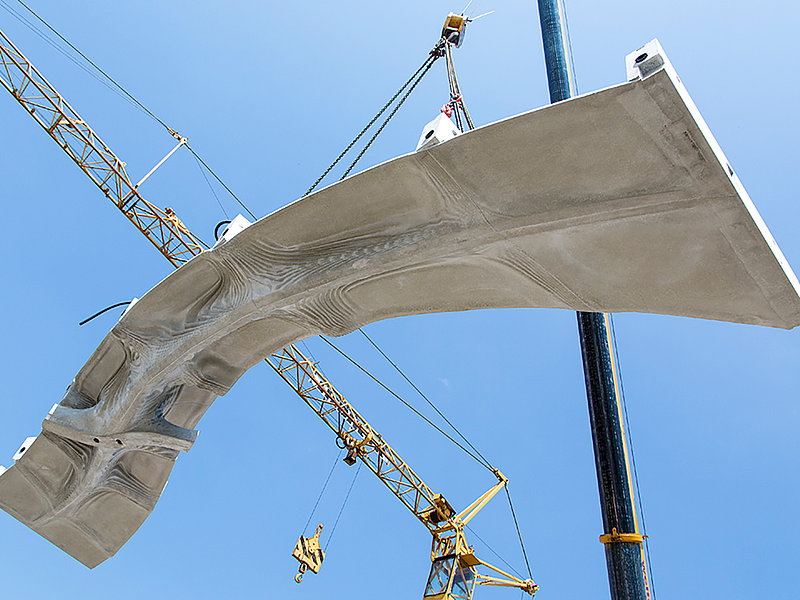
Production at the push of a button
After the computer planning was completed, the Smart Slab researchers’ industrial partners sprang into action. One produced the high-resolution 3D sand pressure formwork, while another used CNC laser cutters to create the wooden formwork. This gives the upper side of the Smart Slab its shape and also includes cavities to reduce material use and weight and make space for electrical cables. The two types of formwork then came together at the third partner company for concreting. This company first injected the fiber-reinforced concrete into the sand pressure formwork to produce the finely ribbed surface of the lower concrete shell, and then cast the rest of the Smart Slab using the wooden formwork.
Strong results thanks to pre-planning
After two weeks of curing, the eleven individual concrete segments were ready for transportation to the DFAB House. The meticulous planning and pre-fabrication, as well as the choice of expert partners and reliable technologies, ensured that the project was completed successfully without any delays. “It was overwhelming to see how seamlessly our elements fitted with one another on the construction site and with the existing components of the DFAB House,” says Dillenburger. “This wouldn’t have been possible without the outstanding interdisciplinary cooperation with our partners.”