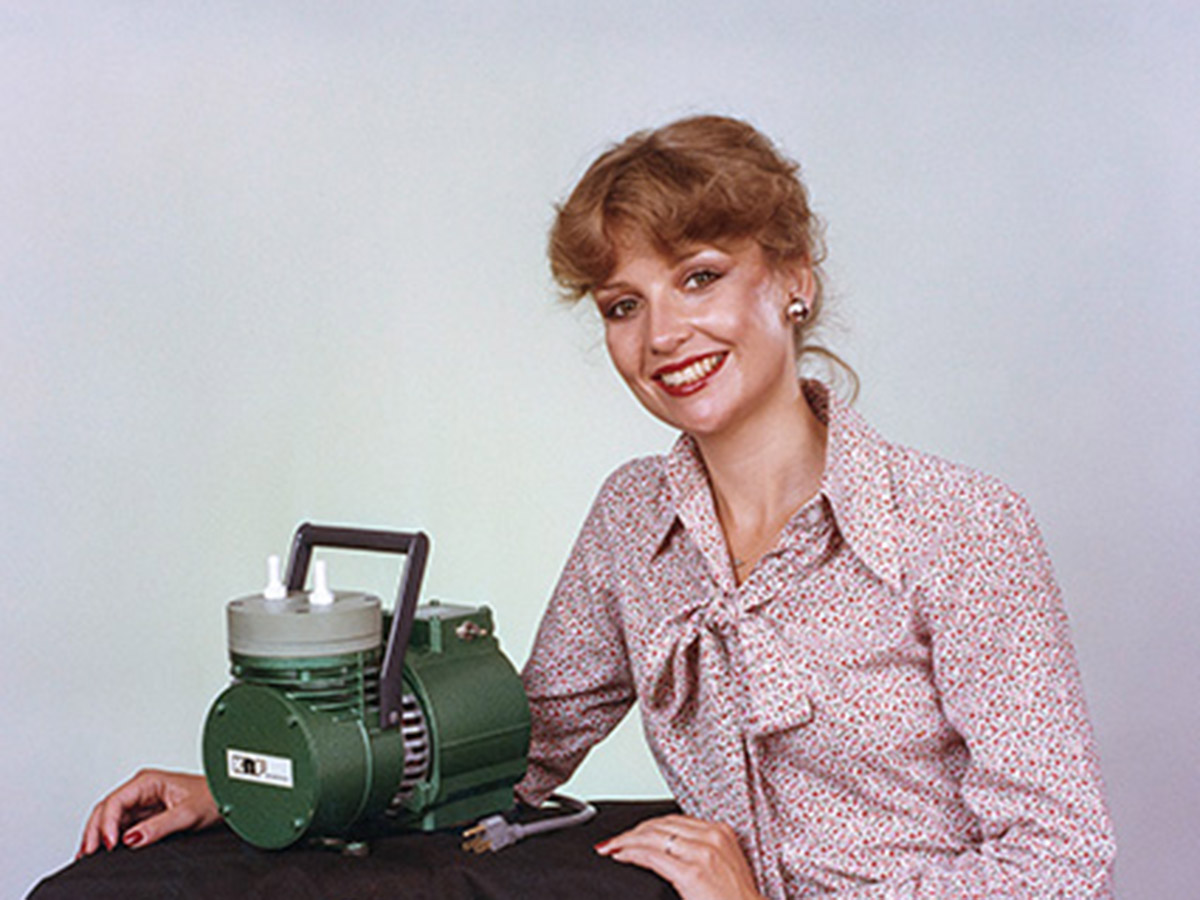
Full PTFE Pumps: Designed for Use With All Gases
Over the last 50 years, KNF and its products have become integral in laboratories worldwide. When the young company registers its first patent in the 1960s, the scientific world is still uncharted territory for KNF. But that changes soon.
The launch of the full PTFE pump in the late 1970s marks a milestone in this journey for KNF. It is the first laboratory pump suitable for universal use. Before this, KNF’s pumps had stainless steel heads and fluororubber diaphragms. However, a specific stainless steel alloy is always needed depending on the solvent to which the pump is exposed. And matters become even more complicated whenever mixtures of aggressive gases have to be transferred.
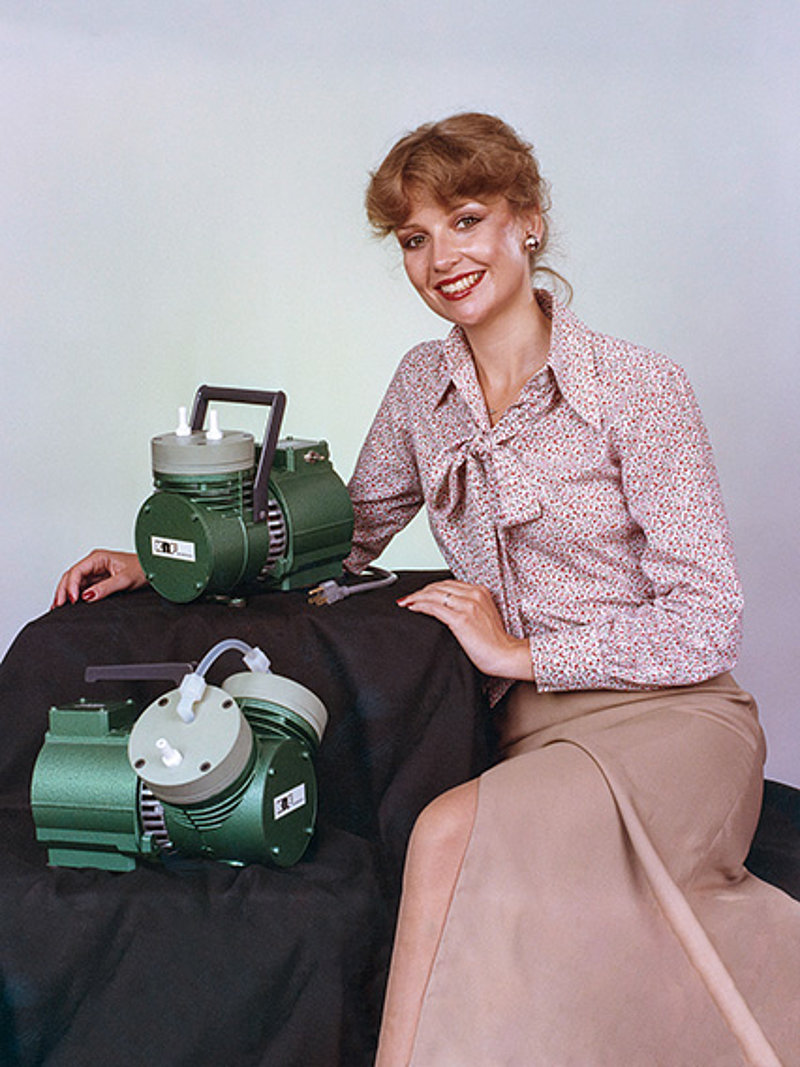
PTFE (polytetrafluoroethylene, which is commonly known by the brand name Teflon), on the other hand, can safely come into contact with all gases. This plastic is used in dentistry, industry and domestically as a coating for saucepans. It is therefore most renowned for its non-stick properties – there are virtually no materials that adhere to Teflon. But PTFE is also very inert. Even extremely aggressive acids like aqua regia are unable to break down the strong bond between its carbon and fluorine atoms. This makes PTFE ideal for laboratory use.
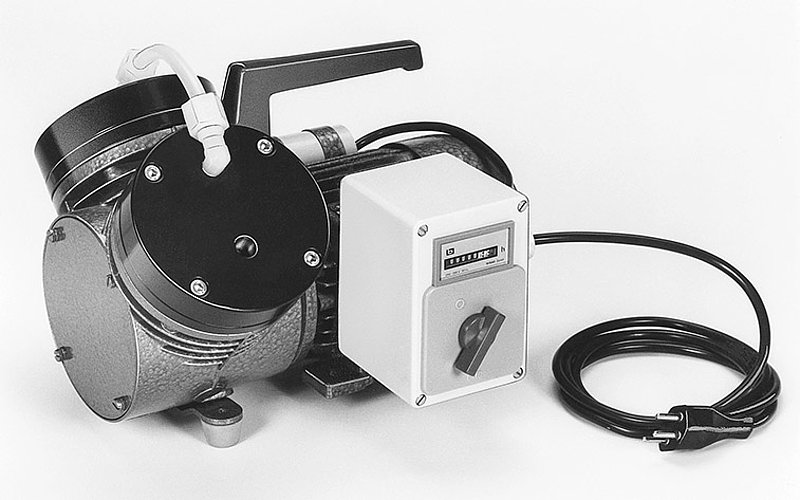
But KNF has to perform a long series of tests before the universally chemically resistant diaphragm pump finally conquers the laboratory market. The full PTFE pump has to share the stage with KNF’s then-new molded diaphragm, which the company also develops at the end of the 1970s. Compared to the flat diaphragms used previously, these molded diaphragms create a better vacuum by minimizing the space between the diaphragm and the pump head plate. The retainer plate used on both sides is replaced by a vulcanized steel component, and the manufacturing process alone gives the diaphragm a streamlined shape. By providing the ideal balance between softness and rigidity, the molded diaphragm takes the vacuum power to a whole new level. It, too, is coated with PTFE – and gets vulcanized later.
KNF sets new standards by using molded diaphragms and applying PTFE to all pump head components coming into contact with the media. Full PTFE pumps still provide optimum chemical resistance today. Laboratory pumps have never stopped evolving. With their improved performance, smaller footprint, new design and intuitive operation, the latest LABOPORT models have come a long way from their bulky, hammertone green predecessors of the 1970s and 1980s. Stylish, quiet and ideally suited to laboratory requirements, today’s versions of these pumps are completely at home in this environment.
KNF Blog Knowledge Flows
Follow the latest trends and stories on how diaphragm pump technology drives evolution in the market.
