Frankfurt, Germany
At Formnext (November 16–19, 2021, Frankfurt, Germany), KNF will be represented at booth E110 in hall 12.0, where the company will showcase two new versatile and reliable liquid pumps for binder delivery.
It’s all about additive manufacturing and 3D printing at Formnext. From November 16–19, 2021, suppliers and manufacturers will finally come together again in person at Messe Frankfurt, where they will have the opportunity to meet with users and customers. KNF looks forward to welcoming interested visitors and presenting two innovations at the exhibition in hall 12.0, booth E110.
FP 70 and FP 1.150 are part of KNF’s smooth flow pump series and combine the advantages of gear and centrifugal pumps with those of diaphragm pump technology: low pulsation, self-priming, dry-running. Both have been practically designed to supply printheads in all printing systems that use jetting technologies. As a result, all kinds of binders can be fed gently and reliably into the 3D printing process. The chemically resistant design by virtue of materials such as EPDM, PTFE or even FFKM enables use in a variety of situations.
KNF FP 70 Pump: Reduced Component Needs in 3D Printing Systems
The KNF FP 70 pump achieves a flow rate of up to 850 ml/min and is developed for an operation of up to 2 bar (29.4 psig) pressure. Furthermore, the patented 4-point-valves ensure the reliable self-priming of the pump. Thus, no additional priming pump is required for filling and draining the system.
Thanks to the integration of pulsation dampening technology, there is no need for additional pulsation dampening elements and tubing when using the KNF FP 70. This means that the pump can operate with particularly low pulsation even where space is limited.
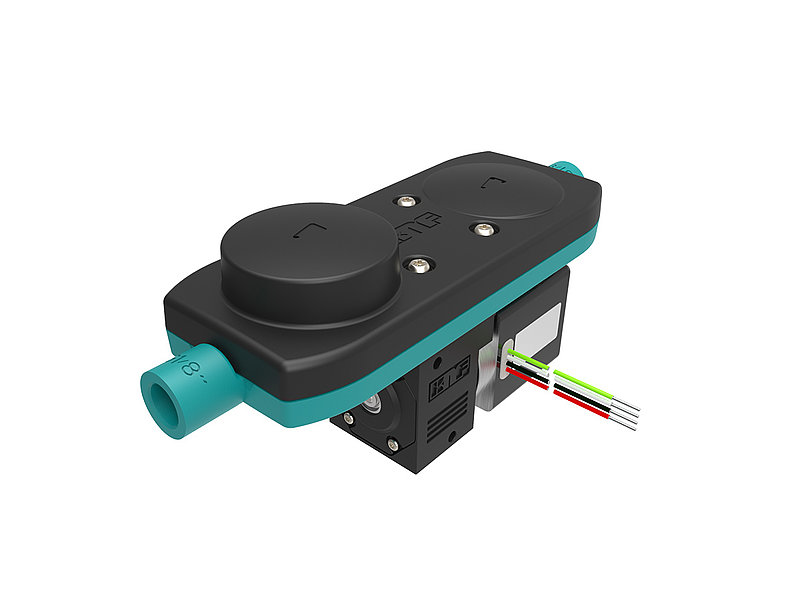
Customizable Binder Supply Without Bubble Formation for Printing Systems Using Jetting Technologies
The low pulsation pump technology used in the KNF FP 70 improves the pump’s efficiency, as pressure resistance in the tubing is reduced and flow performance is significantly enhanced. This can be a crucial factor if small tubing is used. It also reduces bubble formation, which helps to keep the liquid properties in a steady state and therefore increases process reliability.
The system’s requirements also come first when selecting the motor: the smooth flow pump can be equipped with motors of different performance classes, and their parameters can be precisely customized.
FP 1.150: Durable Binder Pump for 3D Printing Systems With Long Feed Lines
With a maximum flow rate of 1.1 l/min and a suction height of up to 2.3 mH2O (6.66 inHg), the addition to the FP 150 pump series offers a powerful maximum operating pressure of 6 bar rel. (87.02 psig).
By interlacing the flow and the pulses generated by each of the 5 diaphragms, a very high and yet smooth flow is achieved in the diaphragm liquid pump. This helps to efficiently transfer liquids through long tubing with smaller diameters, since smooth flow pumps reduce pressure loss. It also minimizes vibration of the tubes, which can be bothersome to the process.
The underlying design principle using 5-diaphragm technology ensures that the binder is supplied particularly gently and with little shearing force.
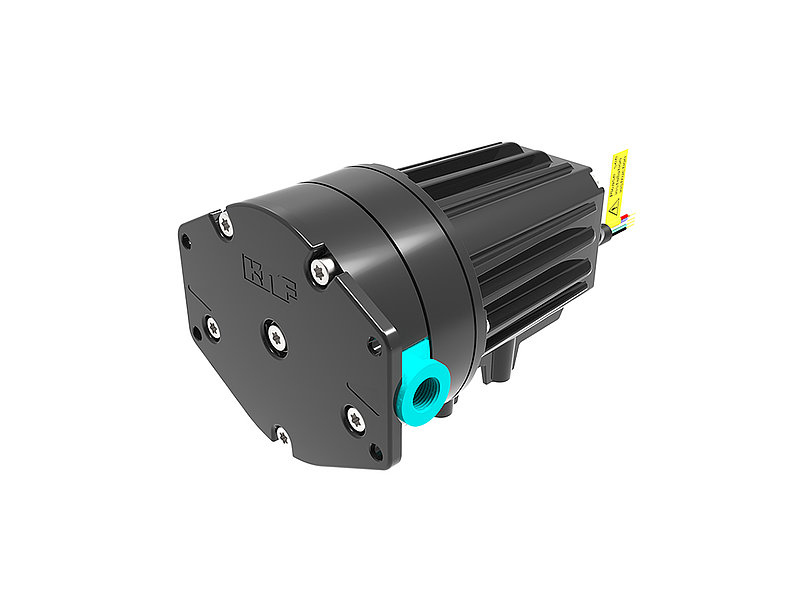