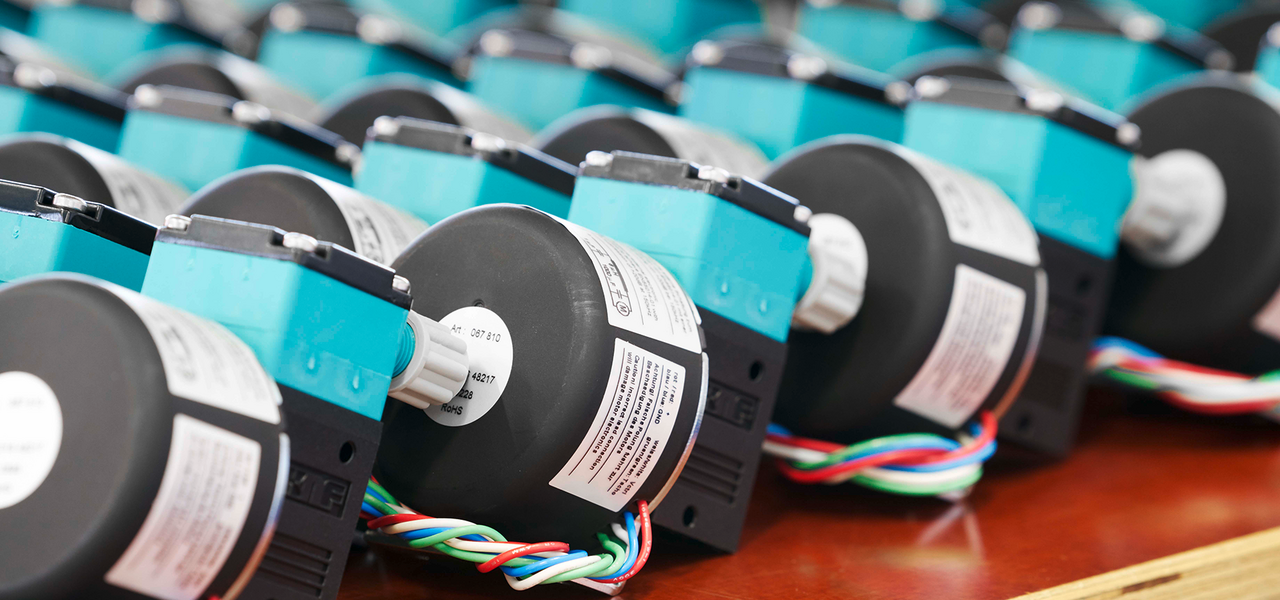
How Does a Membrane Pump Work?
High-performance membrane pumps operate by harnessing the power of a flexible diaphragm to move liquids or gases. Using these pumps ensures the safe handling of corrosive and sensitive fluids and makes them suitable for various applications. Looking at the inner workings of membrane pumps and exploring their functional principles, maintenance requirements, and essential characteristics, we will provide valuable insights into how they operate to meet the diverse demands of modern industries.
What Is a Membrane Pump?
A membrane pump, also known as a diaphragm pump, is a compact, durable, and low-maintenance positive displacement pump that uses the return action of a flexible membrane or diaphragm to move liquids and gases or to generate a vacuum or pressure. Unlike other pump types, membrane pumps do not rely on other mechanical parts that come into contact with the transferred media except for the valves. Instead, they use the diaphragm's upward and downward stroke action to draw and discharge liquid or gas.
What Is the Function of the Diaphragm in a Membrane Pump?
The diaphragm in a membrane pump serves a critical function as it acts as a dynamic seal between the liquid or gas being pumped and the pump drive as well as the environment. It also minimizes leakage to near zero. The diaphragm also makes membrane pumps ideal for handling corrosive, abrasive, or sensitive fluids, as the risk of contamination or damage to the pump components is significantly reduced.
The Functional Principle of Membrane Pumps
Membrane pumps operate on a simple yet effective principle where the pumping process involves two strokes: the downward stroke is the suction stroke, and the upward stroke is the discharge stroke.
- Downward stroke: During the downward stroke, the diaphragm moves away from the inlet, creating a pressure in the pump chamber which is lower than the inlet pressure. This vacuum causes the inlet valve to open, allowing the liquid or gas to be drawn into the chamber through the inlet valve. As this happens, the outlet valve remains closed, preventing backflow of the media from the outlet side.
- Upward stroke: To move the media out from the pump chamber, the upward stroke moves the diaphragm towards the outlet, pressurizing the media in the chamber. This pressure causes the inlet valve to close to prevent backflow while the outlet valve opens, letting the pressurized media out.
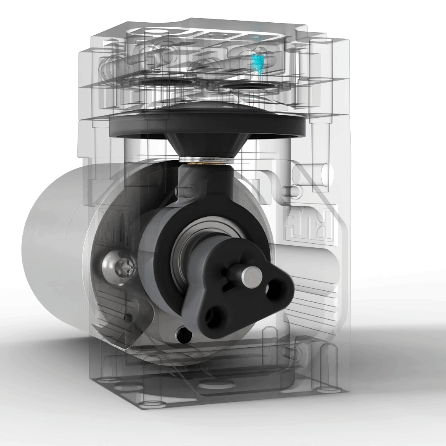
Applications for Membrane Pumps
With their exceptional features, high precision, and long service life, membrane pumps have widespread applications in various industries, including medical, chemical, food and beverage, pharmaceutical, energy, inkjet printing, and analytical instrumentation.
Among these industries, the capability of handling a wide range of sensitive, aggressive, or corrosive chemicals is one of the primary uses of membrane pump technology. The ability of membrane pumps to create a reliable vacuum and resist chemical corrosion and abrasion also makes them a valuable asset in laboratory applications including rotary evaporation, filtration, and solid-phase extraction, ensuring the safety and integrity of the pumping process.
However, the use of membrane pumps is not limited to these industries. Membrane pumps are versatile and valuable tools, and their widespread adoption across other sectors can be credited to ensuring the smooth and efficient supply and transfer of liquids and gases with complete precision, reliability, and safety while safeguarding the integrity of the media they handle.
The Characteristics of Membrane Pumps
Alongside their compact design, membrane pumps have a range of unique characteristics that set them apart from other pump types, making them a popular choice for a wide range of industrial applications. Their design and operational features also contribute to their exceptional performance and reliability.
Understanding these distinctive features will offer insights into why membrane pumps are the preferred choice for various liquid and gas-handling challenges across different industries. We will explore these characteristics in more detail to understand the extent of the membrane pump’s capabilities.
- Self-priming: The pump design means they can prime themselves to generate pressure and start pumping without manual priming.
- Dry run safe: Pumps that transfer liquids can operate for long periods without sufficient liquid, or even when dry, without causing damage.
- Oil-free functioning: Oil used in any pump parts is kept separate from the pump parts that come into contact with the media to avoid contamination and ensure clean use.
- Chemical resistance: Membrane pump head parts and diaphragms as well as valves can be made from various materials to ensure compatibility with almost all chemicals.
- High gas tightness: Even without a secondary membrane, membrane pumps are inherently gas tight. To further reduce the risk of gas leakage, a safety membrane can be fitted in case of damage to the primary membrane.
One of the key characteristics of membrane pumps is the pulsating flow they generate due to the reciprocating action of the membrane. However, excessive pulsation can lead to vibrations or noise that may be undesirable in certain applications or cause system damage. To address this issue, membrane pumps can be fitted with multiple pump heads and/or pulsation dampeners and silencers.
Multiple pump heads can be used in a single pump to minimize the pulsation. By alternating the motion of the membranes, the fluid flow can be made smoother, reducing the pulsation effect. Additionally, pulsation dampeners can be installed on the suction side as well as on the pressure side of the pump.
Choosing the Right Membrane Pump
Selecting the right membrane pump for a specific application is a decision that can significantly impact operational efficiency and overall performance. With a wide range of pump types, each designed for specific needs, making an informed choice requires careful consideration of factors, including:
- Liquid characteristics: Assess the chemical compatibility, viscosity, and level of particulates in the liquid to ensure the pump and design are suitable. In some cases, a viscous fluid pump may be better suited to achieve the required flow rate.
- Gas characteristics: Gases also require a thorough understanding of their characteristics. For example, the requirements placed on the membrane pump can vary depending on the gas type, its isentropic exponent, its density, its humidity or its temperature.
- Flow rate and pressure: Determine the required flow rate and pressure to select a membrane pump that can meet the application's demands.
- Environmental factors: The environmental factors a membrane pump encounters vary from application to application. For example, it may be important to consider temperature, pressure, space limitations, and the presence of volatile atmospheres to select a pump that can operate safely and efficiently in that environment
Membrane Pump Knowledge and Support From KNF
Membrane pumps are a high-performance, effective, and reliable asset for various industries. Understanding how they work, their unique characteristics, and their maintenance needs, will help select the correct membrane pump for specific applications, ensuring optimal performance and longevity.
As manufacturers of high-quality membrane pumps for OEM use, process applications, and laboratory environments, our KNF technical experts have extensive expertise to help customers better understand these pumps.
If you have questions or need technical advice on finding the right pump for your application needs, contact us today.
75 Years: KNF Celebrates Company Anniversary
A treasure chest filled with memories, facts and stories. Learn more about KNF’s company history.
