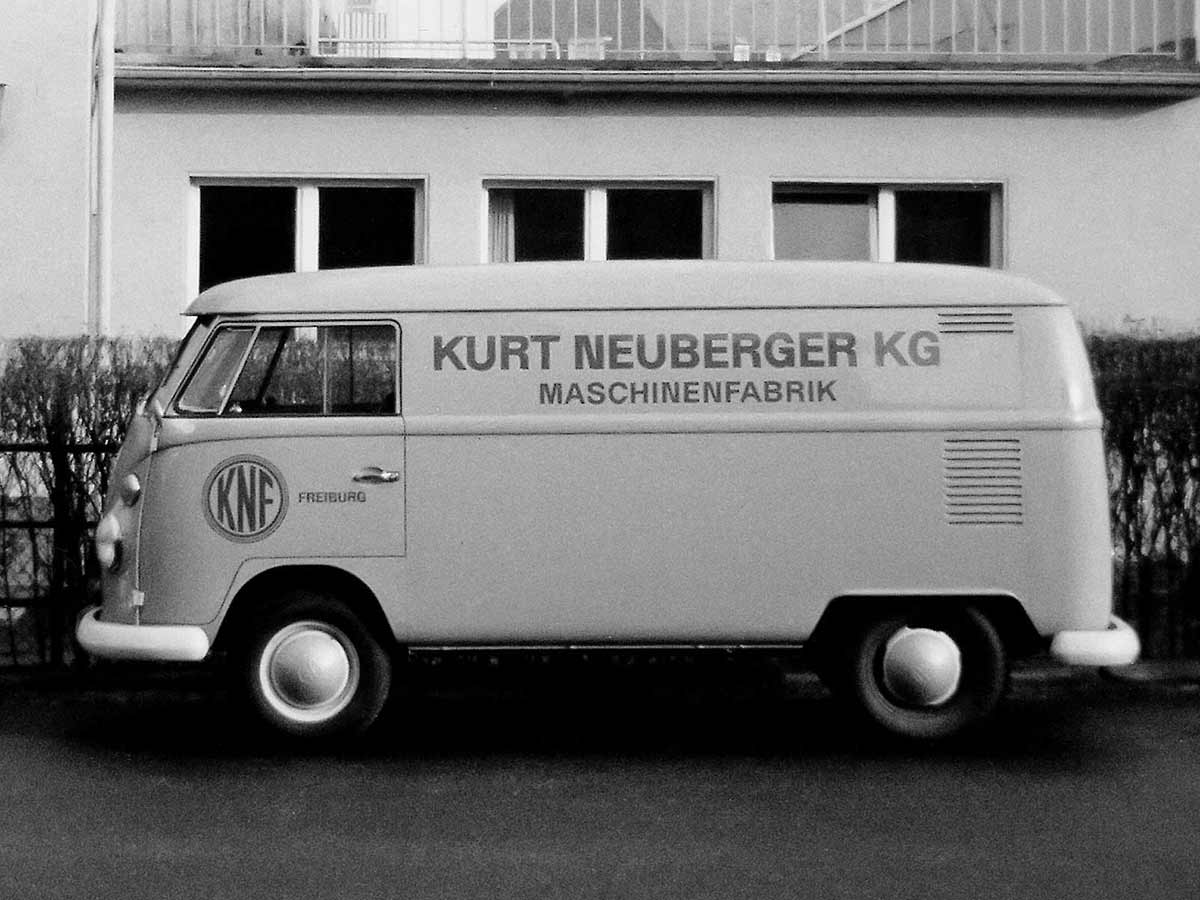
The Turning Point. Erich Becker Joins KNF
By the early 1960s, the situation at Neuberger KG seemed hopeless. The motor repair business slowly ground to a halt and the tools manufacturing enterprise was beset by more and more problems, resulting in a lack of long-term prospects. But this all changed when Erich Becker joined the company. The previously self-employed engineer recognized that the company had hit a dead end, but he also found a way out. The only way to avoid bankruptcy lay in refocusing on a completely new product and fully realigning the company’s mission. Despite the difficult situation, Becker joined Neuberger KG as a partner and set off in search of a new basis for the business. This is how he encountered diaphragm pumps. But it was not easy to turn this idea into a profitable enterprise.
Freiburg, 1962. Customer complaints pile high atop Erich Becker’s desk. One of his first tasks at KNF is to get a handle on problems in thread cutting machine production. As he becomes more involved in the business, he realizes with greater clarity that Neuberger KG neither has the financial means nor the space needed to succeed with machine tools in the long run. “We need to manufacture something small,” he thinks. “A product that won’t require any repairs and only weighs up to 5 or 6 kilograms so that it’s easy to ship.”
He is closer to finding the solution than he thinks. At that time, Neuberger KG is already relying on wage labor to assemble diaphragm pumps used in medical aspiration and suction units as well as in Jacuzzis. As chance would have it, the company Wall is looking for a new manufacturing location, and KNF has production capacity available. Later on, Neuberger KG is given the option to purchase the company. For Erich Becker, the advantages offered by diaphragm pumps are crystal clear: They run maintenance- and oil-free, they are lightweight, and they can be used in many different areas, for instance in laboratory science or industry. However, he initially faces a whole new set of issues. Shortly after acquiring the pump manufacturing company, Erich Becker’s desk is once again filled with customer complaints. So he is forced to fundamentally rethink the pumps’ design.
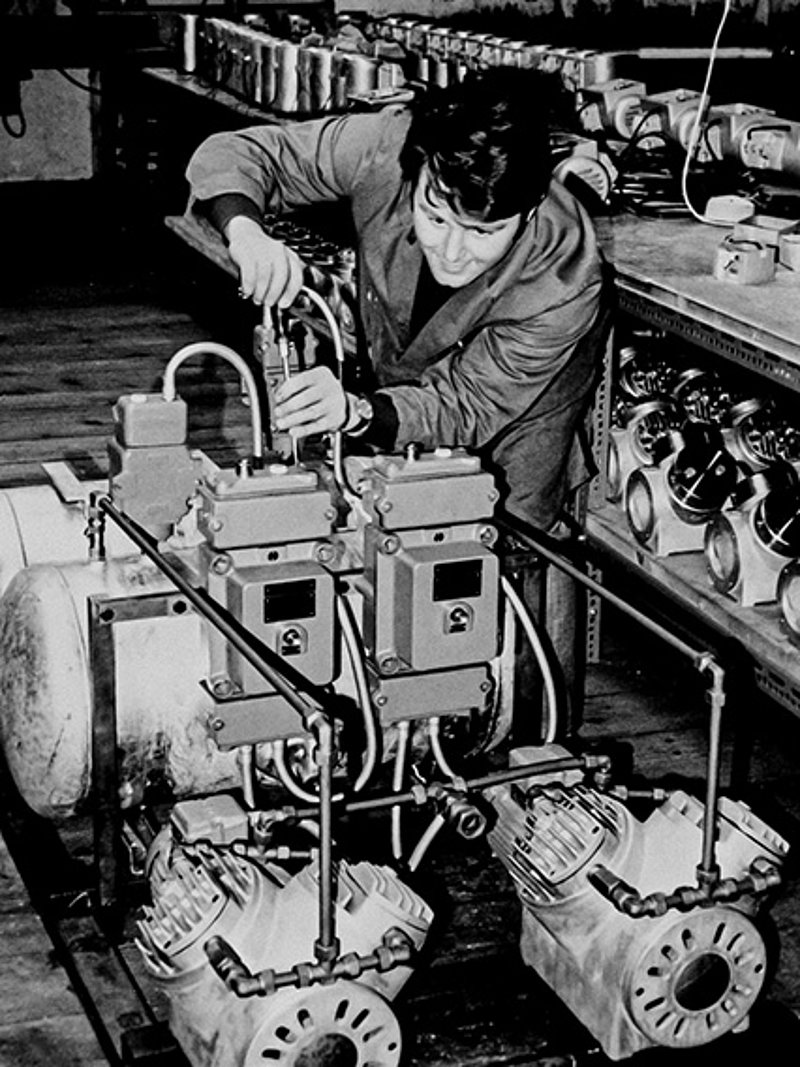
In a shed behind the main business premises on Habsburgerstrasse, Erich Becker sets to work with Heinz Riedlinger tinkering and designing new solutions. In the end, they manage to minimize the stress on the diaphragm, thereby improving the service life – one of the greatest weaknesses of diaphragm pumps. The new version also significantly outperforms previous models. After implementing several other clever technical tricks, KNF obtains its first patent in 1966. And soon enough, the company introduces its own pump series: the AEROMAT series.
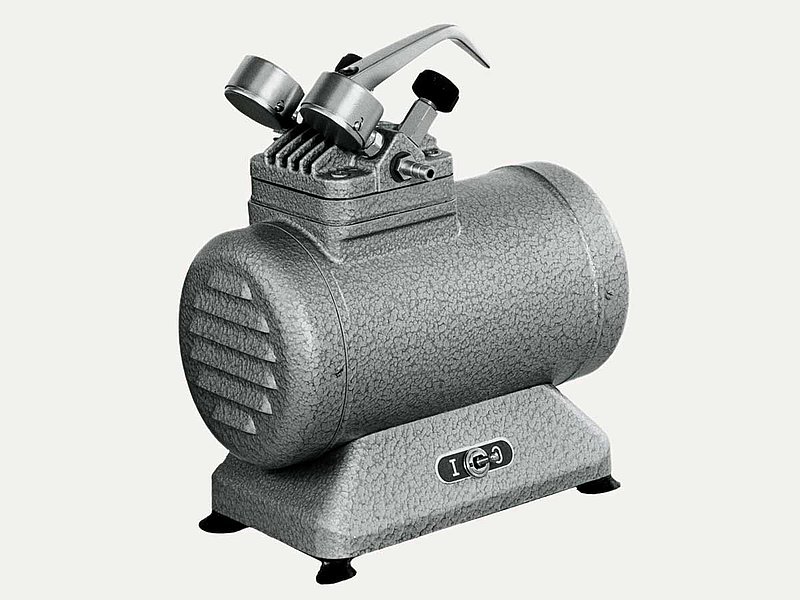
In 1966, Kurt Neuberger passes away and Erich Becker takes over as the company’s sole managing director. “The main goal at the time was to keep the company alive,” Erich Becker recalls, thinking back on this period of radical change. “This gave way to our next objective of firmly establishing the diaphragm pump in the industrial sector.” But the company is met with great skepticism. Erich Becker hopes to break into to the laboratory business with the first AL15 vacuum pump. Yet the start is difficult and finances become ever tighter.
Nearly every Sunday – the beginning of a long workweek for Erich Becker – he gets in his car and drives many miles all over the country. He canvasses laboratory equipment distributors, presents his pumps, collects information and generates contacts. He and his employees celebrate every contract that comes in, no matter how small. However, there simply is not enough money, not even for the pumps’ packaging. In order to keep operations moving, Alexander Gagg – a dedicated employee – regularly drives his VW station wagon to a pharmaceutical company to gather its cardboard waste and wood shavings for reuse. This means that the first KNF pumps are sometimes packaged in small boxes and sometimes in larger ones, depending on what Alexander Gagg finds on his collection route.
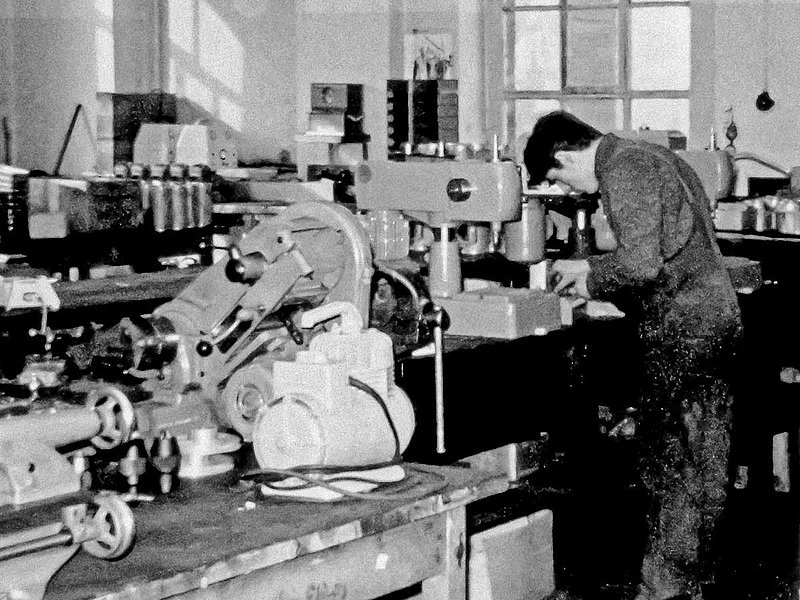
Meanwhile, Erich Becker and Heinz Riedlinger continue working to optimize the pumps. And their efforts are not in vain: The N25 Picco pump, which features a transfer capacity of 20 liters per minute and an ultimate vacuum of 20 millibar, achieves a breakthrough in the laboratory sector, in many cases replacing the popular water jet pump.
Even the long-awaited breakthrough into the industrial sector is not too far off.
KNF Blog Knowledge Flows
Follow the latest trends and stories on how diaphragm pump technology drives evolution in the market.
Knowledge Flows