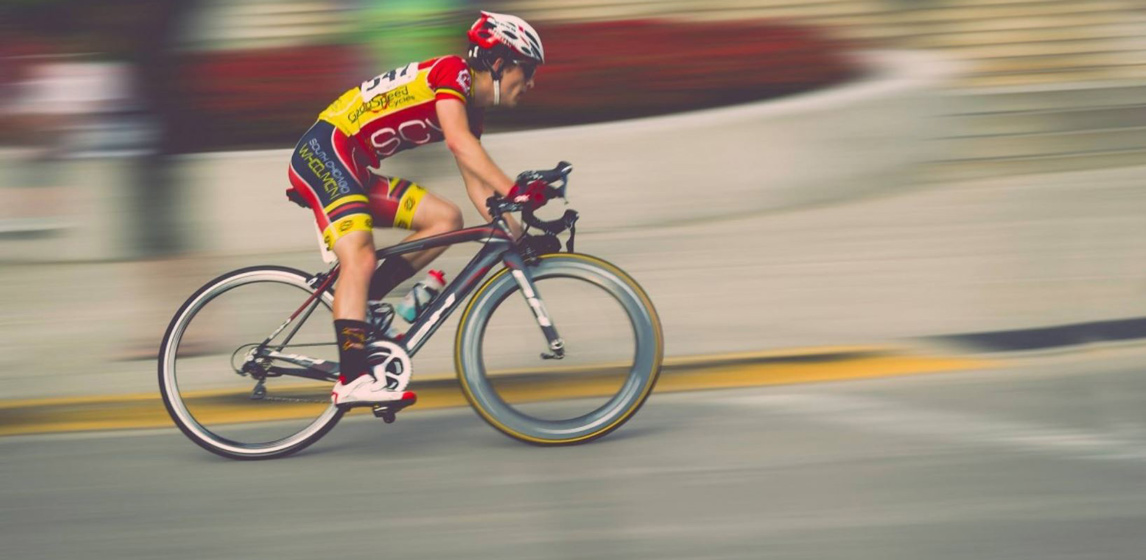
Longer Operating Times in Continuous Inkjet Printing
Continuous Inkjet technology is used exclusively in industry and professional printing systems. The process, where there is no direct contact between the print head and the surface to be printed, is too complex and expensive for private use such as in a home office. In simple terms, the continuous inkjet (CIJ) process uses a high-pressure pump to transport a jet of ink into a nozzle. A piezoelectric transducer splits the jet into a wave of microdroplets which leave the nozzle at up to 5.0 bar. Complex electronics for charging and deflection ensure that the ink droplets reach their target.
The droplets not needed for printing text are channeled into a collector by means of negative pressure and returned to the ink bottle by means of a gutter pump. The process is ideal for printing on very uneven materials. Cable ID codes or expiration dates on cans, bottles and other packaging demonstrate possible uses for the CIJ process.
Gear pumps struggle with ink containing pigment concentrations
Gear pumps are often unable to operate dry and are not always self-priming. In addition, the movement of the gears means there is always a risk of mechanical wear, especially when pigmented inks are used. The grinding of pigment between the gears can cause them to become worn, leading to an increased flow rate and eventually to pump failure. The pigmented ink can also be damaged through contamination of dust generated from the gears. This can result in higher maintenance and production costs. Another critical point in the gear pumping process is the shear forces generated by the gears, potentially compromising the mechanical properties of the ink and negatively impacting the print quality.
Diaphragm pumps ensure a reliable and low-maintenance process
Due to its design, the diaphragm pump technology generates only low abrasives. The membrane, whose movements run smoothly like a massage, protects the sensitive liquids resulting in process stability and less maintenance. Since diaphragm pumps do not require mechanical seals and are nevertheless absolutely leak-proof, their operating times and service lives are correspondingly long and result in lower costs. This is due to the fact that mechanical seals require much more frequent maintenance if the wear part has to be replaced. The pump is dismantled during maintenance and tested on the test bench after assembly. This is connected to costs and downtime. The abrasion in the CIJ can over time also affect other parts of the pump. Then it needs to be investigated if a repair is still worthwhile or the entire pump must be replaced.
Different ink compositions may contain additives, which can decompose the diaphragm, connections or pipes as well as other parts of the pump. This places high demands on the chemical resistance of the materials used in the pump and influences their selection significantly. For designing the right pump, we recommend, exchanging as much information as possible with our experts regarding ink compositions and process specifications in general.
75 Years: KNF Celebrates Company Anniversary
A treasure chest filled with memories, facts and stories. Learn more about KNF’s company history.
Anniversary Blog