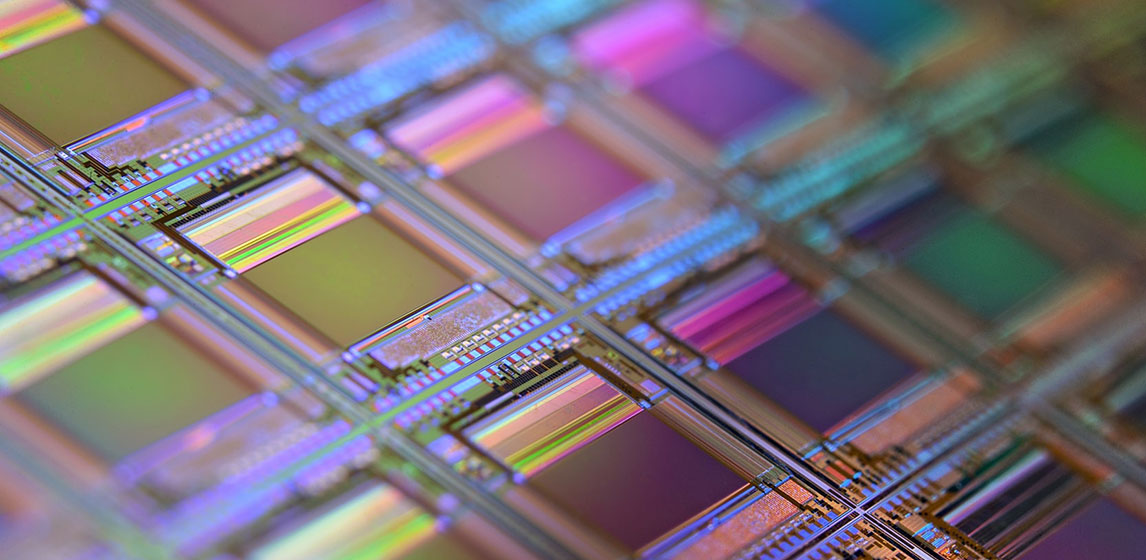
Semiconductor Industry: When Just Clean Is Not Clean Enough
The semiconductor industry creates true wonders of modern technology: containing millions of transistors at an incredibly small scale, microchips provide computing power and memory in our smartphones, tablet computers, refrigerator, cars and many more. As semiconductors are extremely small, their manufacturing takes place on a nanoscale, making the processes vulnerable to external influences like microscopic dirt particles or ionization. This is why Canon Nanotechnologies, Inc., a world-leading R&D company of nanotechnology for semiconductor manufacturing, chose to work with KNF. Together, the goal of producing fluid transfer pumps that can cope with these extreme demand was met.
The high fluid management demands of the semiconductor industry
Within the world of microelectronics, Canon Nanotechnologies is a leading R&D company of cutting-edge nanotechnology for semiconductor manufacturing. During the process developed by Canon Nanotechnologies, arrays of small drops of fluid are placed onto silicon wafers. This process is similar to the conventional inkjet process, but on an extremely small scale. It also involves a fluid that not only needs to be extremely pure but must not be ionized under any circumstances. These demanding requirements necessitate the usage of highly specialized equipment. Here, a special focus lies on the fluid transfer pumps that transport the liquid within this process.
Searching for the ideal fluid transfer pump
As the fluid needs to be ultra-pure and must not be ionized, the materials of the pumps need to be chosen carefully. At the time, Canon was using centrifugal pumps made of PTFE. While KNF diaphragm pumps already represented a better alternative to the centrifugal pumps in terms of flow rate and gentleness, KNF also aimed at using an even cleaner and completely ion-free material. This was due to the fact that Canon Nanotechnologies had been tightening the requirements on ion contamination in recent years. After extensive research, the usage of a polymer called PCTFE was proposed. This material had never been used in KNF pumps before.
Introducing a new material to the industry
When KNF advised to make use of this new material, Canon Nanotechnologies agreed to rigorous testing. This was necessary as the benefits of using this polymer were great in theory but needed to be proven in the real world. Canon Nanotechnologies extensively tested a material sample sent by KNF. After putting the PCTFE sample to proof for several months, the superiority of the new polymer over the previously used PTFE became clear. With this result, the development process of the custom-made pumps advanced.
Modular design approach accelerates development process
With the entirely new material approved, KNF then very quickly provided a first prototype within six months. This rapid development process was only possible because of an elaborate modular design approach. While PCTFE was a completely new material to be used for fluid transfer pumps, the rest of the pump could be developed by combining pump components, like motors and valves, that had already been tested and used in other configurations. This not only reduced development time significantly but also resulted in a reliable pump for the semiconductor industry that consists of pre-tested and industry-proven components.
75 Years: KNF Celebrates Company Anniversary
A treasure chest filled with memories, facts and stories. Learn more about KNF’s company history.
