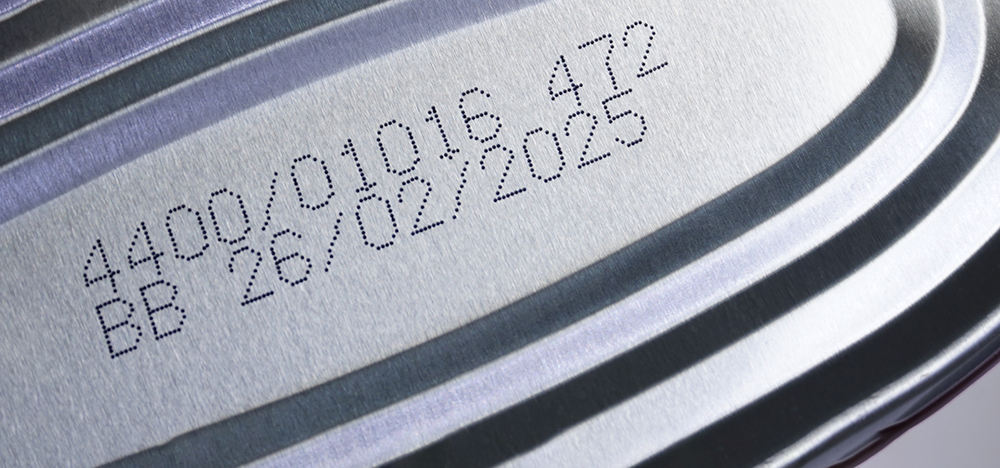
Continuous Inkjet Pumps Enable the Next Generation of Printing Systems
Continuous Inkjet (CIJ) systems print information like best-before dates, serial numbers or batch codes on various surfaces like cardboard, plastic, glass or metal in many industries worldwide. For this important task, they rely on several pumps. In the past, this has often been a mix of gear pumps and diaphragm pumps. Since the diaphragm pump technology has made great advances reducing their pulsation levels, they can now be used in all applications of such a system, offering many economic and technical advantages.
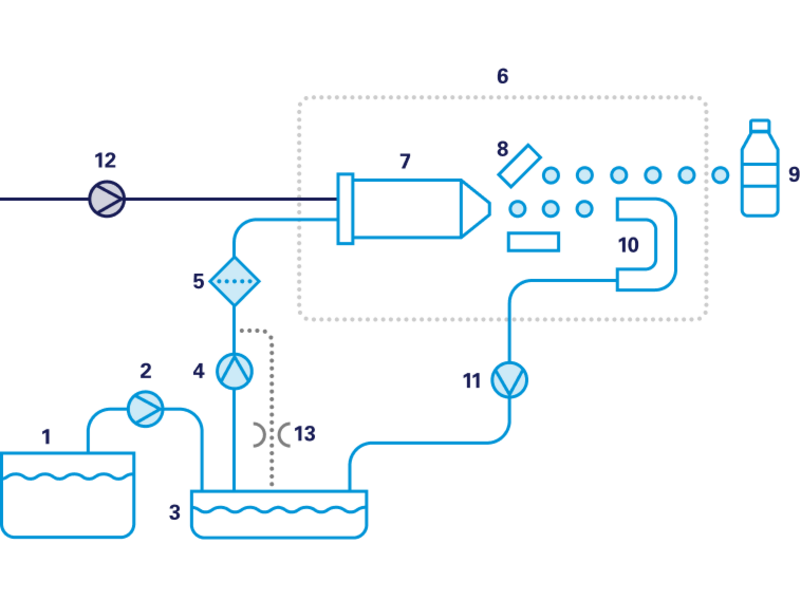
Continuous Inkjet Systems Rely on Many Pumps
CIJ systems rely on a number of different pumps. Normally the ink and the solvent are transferred from large containers (1) via a bulk delivery pump (2) to a reservoir (3). From there, the ink is transferred to the printhead (6) via a pressure pump (4). Between the pressure pump (4) and the printhead (6), a damper (5) is used to reduce pulsation. In the printhead, the ink flows through the nozzle (7) creating a continuous array of small ink drops which can individually be charged. Charged drops are then deflected via electrodes (8) and hit the object that is supposed to be printed on (9).
Drops that are not charged fly in a straight line into the gutter (10) from where the ink is recirculated to the reservoir (3) via a gutter pump (11). In order to prevent the ink from drying out and therefore damaging the system when turned off, continuous inkjet systems are also equipped with a solvent pump (12) that delivers solvent to the nozzle to clear it from ink residues.
Disadvantages of Gear Pumps in CIJ systems
In the past, many of the pumps mentioned in continuous inkjet systems were gear pumps because they used to produce less pulsation than diaphragm pumps. This has changed dramatically in recent years as KNF has pushed the boundaries of its unique Smooth Flow Technology. Modern KNF diaphragm liquid pumps can run with very low pulsation levels which means that often the bypass and dampener can be left out, allowing for significant simplification of the entire printing system.
Most gear pumps also create cavitation which may damage inks and produces bubbles in the ink. In addition, their self-priming capability is below that of diaphragm pumps and most gear pumps are not really dry-run safe – not speaking of the danger gear pumps pose to pollute the ink with particles that come from gear abrasion. In systems using a gear pump as a pressure pump (4), normally also a bypass orifice (13) is needed that feeds ink back to the reservoir when the flow becomes too high due to the inferior controllability and pulsation of the gear pump.
Diaphragm Pumps – The Future of Continuous Inkjet Systems
With the new generation of KNF Smooth Flow Pumps, all pumping tasks in a CIJ system can be done by diaphragm pumps. When such pump is used as the pressure pump (4), the orifice bypass (13) becomes obsolete due to the superior controllability and the low pulsation of the Smooth Flow Pump. Depending on the specific system design, even the damper (5) might become obsolete. This reduces the system complexity and saves costs.
For all other pump jobs, many CIJ system manufacturers already rely on diaphragm pumps due to their superior properties. They are self-priming, can run dry safely and produce almost no cavitation. In addition, they are extremely robust and offer a long service life and low maintenance. Their cleanliness and chemical resistance is another significant advantage for using them as continuous inkjet pumps.
Discover our inkjet expertise!
75 Years: KNF Celebrates Company Anniversary
A treasure chest filled with memories, facts and stories. Learn more about KNF’s company history.
Anniversary Blog