The Perfect Drop of Ink Requires Teamwork
Drop-on-demand inkjet printers rely on the perfect interaction between valve and pump

When it comes to drop-on-demand printing, the print quality is dependent on each drop being ejected at the correct amount and at the right moment from the printhead onto the substrate. Reliable ink management is key.
The combination of Kendrion’s valve expertise and KNF’s durable diaphragm pumps creates suitable solutions for this task.
Pressure and vacuum for essential functions of industrial inkjet printers
When it comes to creating a printed object, the ink goes through three important steps: First of all, the ink has to be transferred from the storage tank to the header tank on the printhead, where the ink then needs to be dispensed through nozzles onto the substrate. Thirdly, as dried ink interferes with the printing quality, ink residues need to be purged from the nozzles.
All these steps are controlled by pressure and vacuum, which are generated by KNF pumps and applied via fluid isolation solenoid valves by Kendrion.

Requirements for valves and diaphragm pumps in drop-on-demand inkjet printing
Industrial drop-on-demand printing has the advantages of being highly flexible and producing high-quality prints on a wide range of surfaces. To make the most of these advantages, Kendrion offers fluid isolation valves of the model series 97 while KNF’s pumps guarantee a long service life, even for use of pigment ink. By selecting the proper material, their chemical resistance can be adapted to the ink’s composition.
As KNF’s maintenance-free pumps run oil-free, they do not contaminate the ink. Kendrion’s fluid isolation valves as well as KNF’s pumps are compact, fully rinseable and can be easily installed and removed. The components’ low weight is particularly advantageous when installed directly on the printhead.
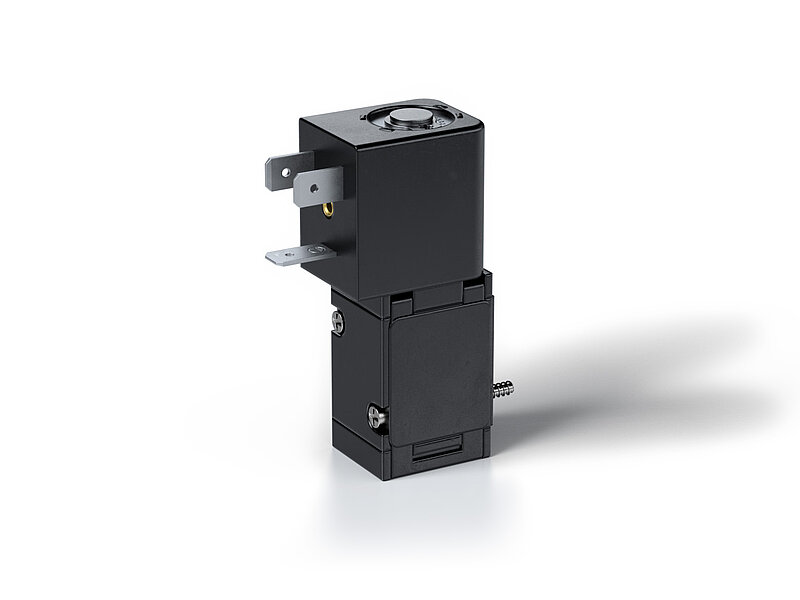
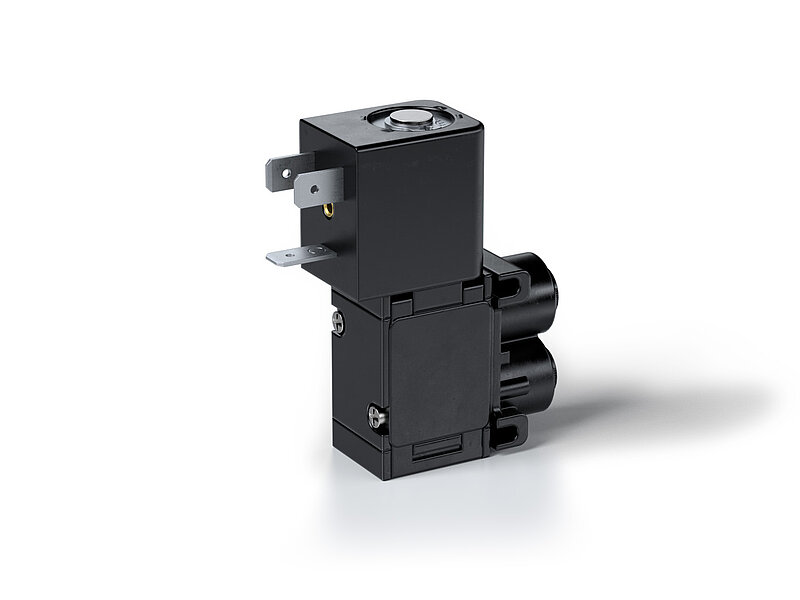
Inkjet ink from the supply to the header tank at the printhead
One basic requirement for good inkjet printing is a sufficiently full header tank. Kendrion’s and KNF’s components work hand in hand to ensure the header is continuously filled. When the fluid isolation valve on the header tank opens, the pumps switch on and gently pump the ink with low pulsation from the supply tank through the hose to the header tank. The hose can be up to several meters long. Once the header tank is full, the valve closes and the KNF pump switches off. The reciprocal action of the valve opening, the pump switching on and the valve closing follows a pre-determined filling strategy and can be variably adjusted.
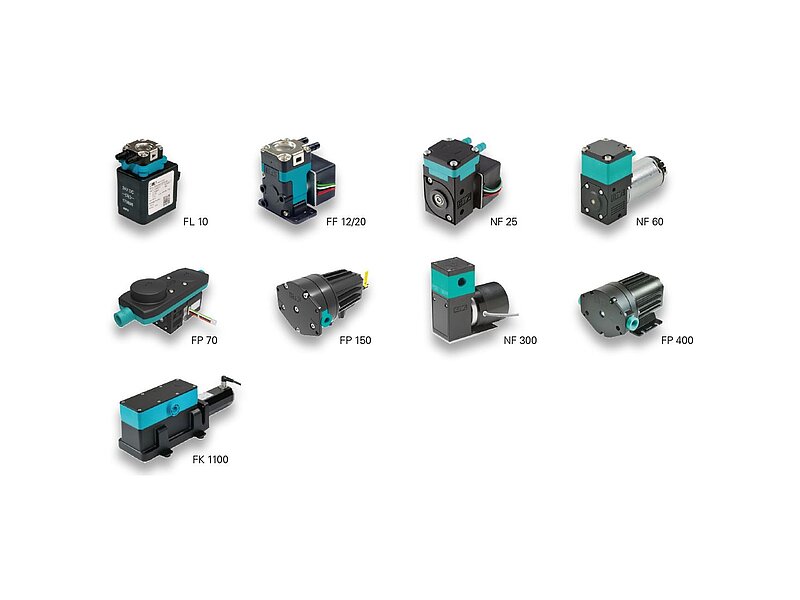
Meniscus pressure for the right drop shape
Kendrion’s model series 97 fluid isolation valves and KNF’s diaphragm pumps work hand in hand, demonstrating the highest degree of dynamism at the printhead. This is where the perfect drop shape is created. The meniscus pressure on the inkjet printhead is essential for the process. The precise balance between overpressure and underpressure causes the right amount of ink to be dispensed from the nozzle at the right moment, so that a perfect drop shape is placed onto the substrate. Kendrion’s FluidBoard® is an innovative system for connecting plates that perfectly fulfills the requirements of high leak tightness. FluidBoard® and fluid isolation valves by Kendrion and KNF’s micro gas pump are finely tuned to one another, working as a unit that is adjusted by pressure parameters.

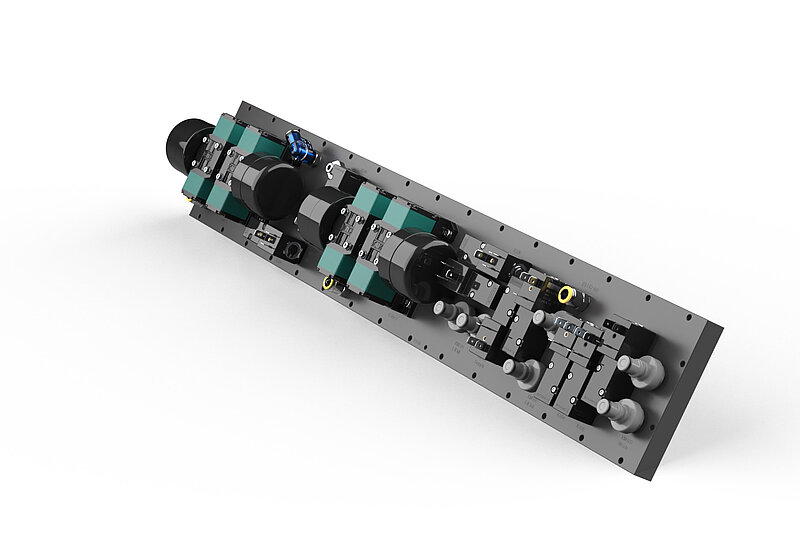
Fast-paced timing for a high inkjet printing speed
Once the overpressure has transferred the desired ink volume from the header tank, the ink must be prevented from flowing uncontrollably from the printhead due to gravity. This is where KNF micro gas pump come in by creating underpressure. The vacuum leads to a curved shape of the drop, the so-called meniscus.
The interaction between perfectly timed fluid isolation solenoid valves with minimal power consumption and meniscus pumps is precision work – a difference of 1–2 mbar will determine whether a drop leaves the nozzle. Kendrion’s valve timing accommodates the high pressure dynamics of drop-on-demand printing.
The micro diaphragm pumps with brushless motors from KNF’s Digital Customization series are particularly well-suited for this task. The continuous measuring of a pressure sensor helps control the motor as it steadily increases the rotational speed until the set point and the associated valve setting is reached. This start ramp can be parametrized variably. This also applies to other operating conditions, such as a pause in printing, in which the motor speed is curtailed to save energy without losing the meniscus-generating vacuum.
There are different technical methods to achieve the meniscus effect. KNF pumps support all technical methods that exist in the market.

Purging for clean ink channels and nozzles on the inkjet printhead
Dried ink interferes with the print quality. Purging is essential for cleaning channels and nozzles to ensure that, in the next printing process, ink drops can form and land on the print substrate without obstruction.
The KNF diaphragm pump creates overpressure towards the printhead. Once the Kendrion fluid isolation valve opens, the overpressure acts outwards through the printhead nozzles, ejecting any ink residues.
The FluidBoard® by Kendrion creates a two-dimensional, completely free channel design, connecting the KNF diaphragm pump and the Kendrion fluid isolation solenoid valve with various other interfaces of the unit. This ensures the optimal rinseability of the entire system in any operating state.
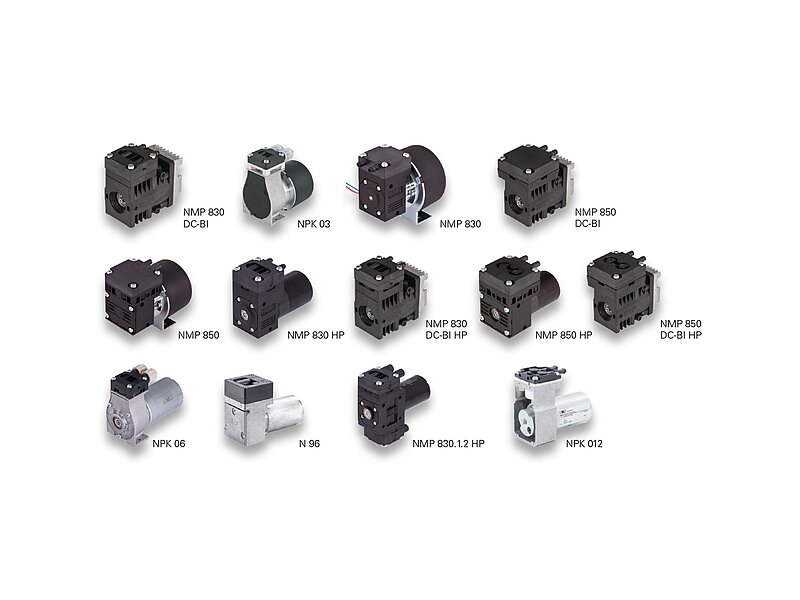