KNF N 1400 diaphragm pump for drying hydrogen
Testing, Measuring and Analyzing Electrolyzers
KNF pumps on electrolyzer test stations make the production and quality of hydrogen reliable
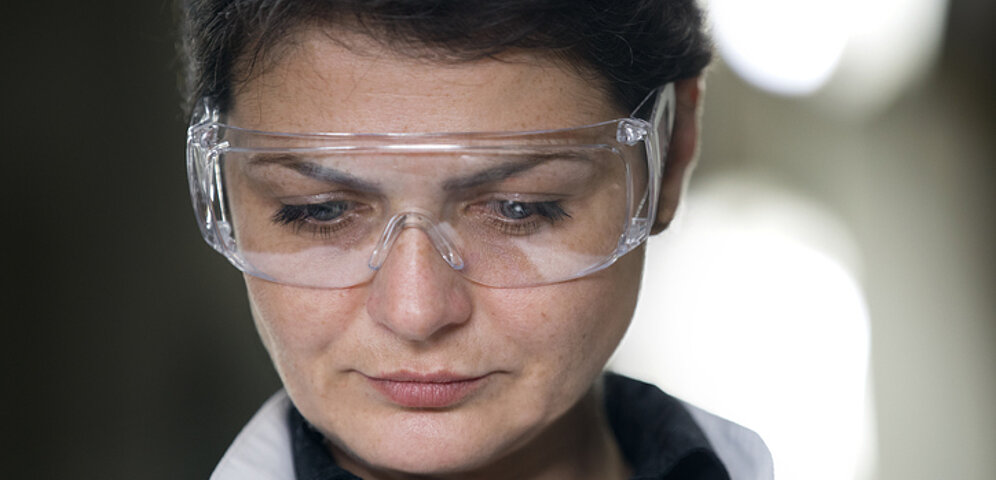
When it comes to testing, qualifying and validating the performance and quality of electrolyzers, HORIBA FuelCon GmbH is one of the first ports of call worldwide.
Combining competence, high-grade analysis and measurement technology with bespoke test systems is what made HORIBA FuelCon a market leader.
The company uses several KNF liquid pumps and gas pumps on its test stations.
KNF pumps help to ensure that the electrolyzers on the test system operate without disruption, enable high cycle rates for the automated test cycles, and extract sample gas to determine the quality of the process and the hydrogen.
Test stations for PEM, SOE, and AEL electrolysis
Electrolysis is the process of splitting water into its elements of hydrogen and oxygen in an electrolyzer. There are various methods for the electrolysis of water, which differ in the electrolytes used, the operating temperature and the structure of the electrolytic cell.
In PEM (proton-exchange membrane) electrolysis, pure water is supplied to the electrolyzer’s anode and split by a catalyst. While oxygen is created on the anode side, hydrogen ions are conducted through a solid polymer membrane to the cathode side, where they form hydrogen molecules.
Solid-oxide electrolysis (SOE) involves water steam at temperatures of around 900°C.
In the third method, alkaline water electrolysis (AEL), hydrogen is produced on the cathode side, while oxygen ions are transported to the anode side through an alkaline solution.
While the methods differ, they all share some basic principles: The quality and function must be guaranteed and reproducible. Water or water steam, as well as oxygen and hydrogen, need to be transported.
However, each method places different requirements on the sensor and control technology of the electrolyzer test station. HORIBA FuelCon develops and manufactures test sytems for all electrolysis methods. The station design meets the requirements of each method for reliable and reproducible testing of functions and operation strategies.
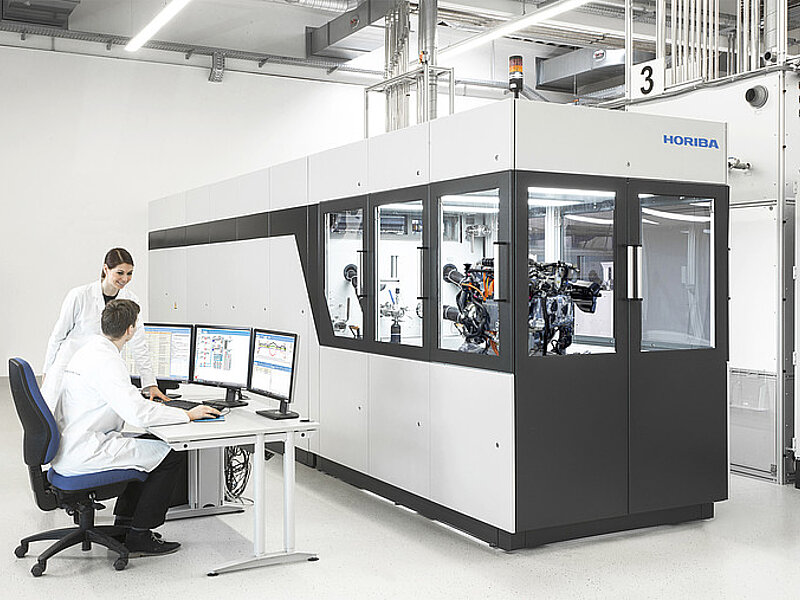
Flexible HORIBA FuelCon test systems for a wide range of services
HORIBA FuelCon test systems offer flexible solutions for applications and tests with electrical power requirements between 10 W and 5 MW, up to 16,000 A current intensity, up to 1,200 V voltage and up to 100 bar pressure.
These test stations use cutting-edge analytics for robust, reliable and highly accurate measurements thanks to high-quality components. Part of the secret of the success of HORIBA FuelCon stations is the longevity of their components. KNF pumps meet these requirements particularly well, which is one reason they are used for customized test systems.
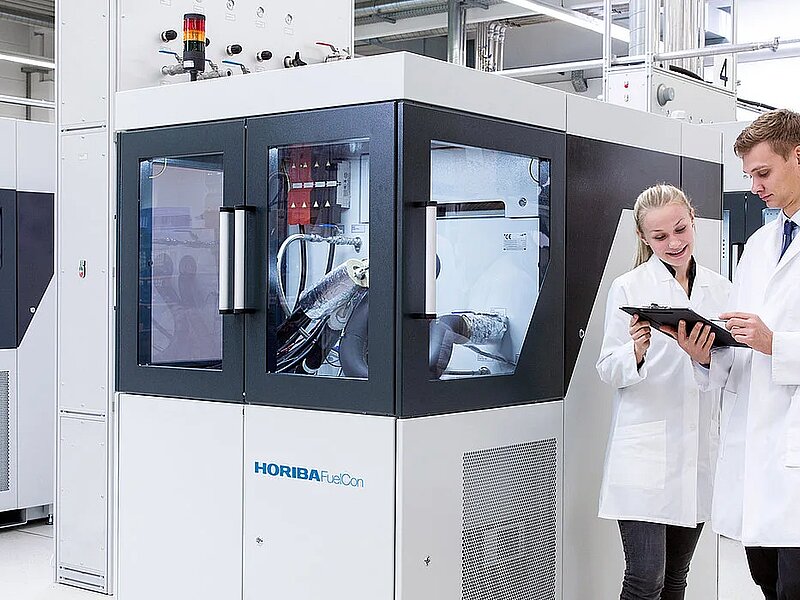
Durable KNF pumps for electrolyzer test systems
Testing the function and operation strategy of an electrolyzer means subjecting it to real-life performance parameters, but it also entails assessing their limits by simulating extreme conditions. The exact test parameters are specified by the customer.
An electrolyzer test system is decisive for permanently improving electrolysis processes and testing their quality and functions. Longevity is imperative and therefore a key selection criterion for test system components.
KNF liquid pumps transfer water to the electrolyzer in the test system
Fault-free operation is essential for testing electrolyzers. The continuous supply with deionized water plays a big part in this. HORIBA FuelCon uses two KNF NF 1.300 series liquid pumps for the water supply.
One of these pumps transfers the non-deionized water into the humidifier/tank against a maximum system pressure of 5 bar. The liquid pump must be capable of starting against this level of pressure.
The other pump transfers deionized water into the electrolyzer, ensuring the controlled replenishment and continuously compensating the water consumption caused by electrolysis. To this end, the pump runs for ten seconds every minute.
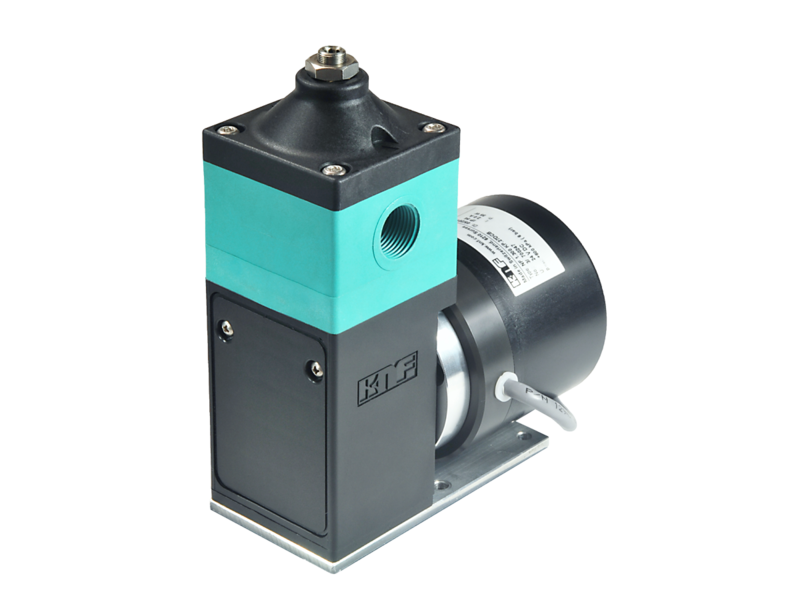
Vacuum pump for a maximum number of test cycles on the electrolyzer test system
The N 838 series diaphragm gas pump evacuates the tank containing the sample. The tank is evacuated at an absolute pressure of 100 mbar, and subsequently filled with water. The suction line is designed as an upward stub line. Although water droplets are occasionally drawn in, this does not interfere with the operation of the vacuum pump. The process takes about 30 to 40 seconds and is carried out several times per day.
The N 838 evacuates the tank very quickly. The faster the tank is refilled with water, the sooner testing begins, and the more test cycles can be completed. The vacuum performance of the N 838 affects the time it takes to complete a test series on the test system and how quickly the test system is ready for the next sample.
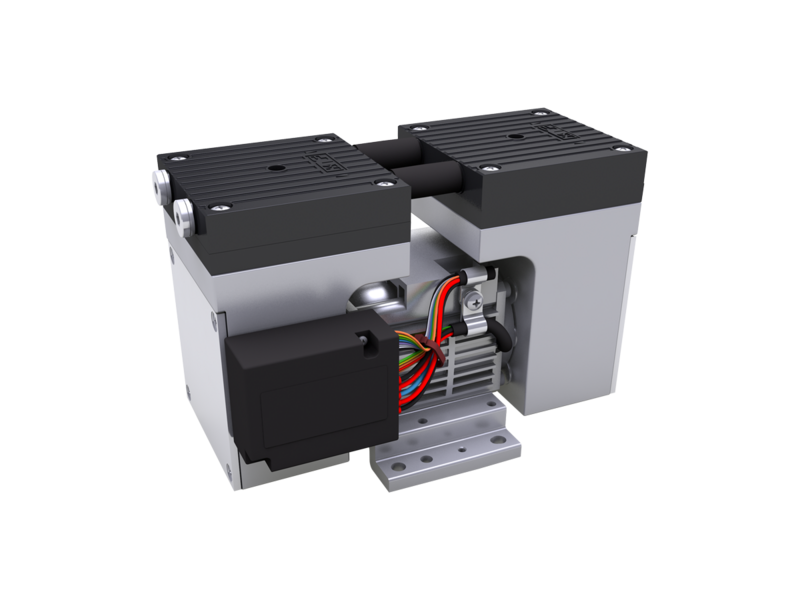
Micro gas pump on the test station for process quality analysis
Following electrolysis, an NMP 830 series micro gas pump extracts a defined volume from the humid hydrogen and guides it across the humidity sensor. The moisture value measured provides insights into the quality of the water splitting. In addition, comparing the moisture content of the hydrogen after electrolysis with that after gas drying shows the effectiveness of the purification and drying stages. These measured values are the basis for adjustments. Changes in the moisture value may also be an indicator for technical failures, such as a broken diaphragm.
The gas sample extracted by the KNF micro gas pump on the HORIBA FuelCon electrolyzer test system can reach temperatures of up to 60 degrees Celsius. Neither the temperature nor the accruing condensate interferes with the pump’s functioning.
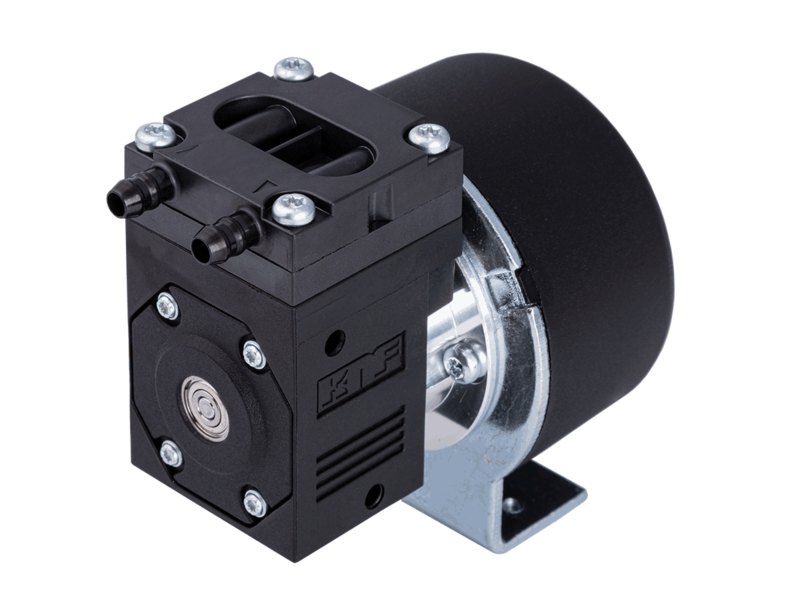
Test system with Ex-version gas sampling pump for gas analysis
What is the quality of the generated hydrogen? This question cannot be answered through function tests, but by analyzing the gas produced on the test system.
A KNF gas sampling pump is part of the online gas analysis. There is a risk of explosive gas mixtures developing, which necessitates an explosion-proof version of the N 87 pump series. As a continuously working gas sampling pump, the N 87 Ex extracts a volume of about two liters per minute – depending on which electrolysis method is being tested. The sample gas is dry – the KNF gas sampling pump is installed behind the gas dryer. High gas tightness is crucial for a reliable analysis of the sample gas. This important requirement is fully met by the KNF gas sampling pump. HORIBA FuelCon’s choice of material was EPDM for the diaphragm and stainless steel for the pump head. These were selected from KNF’s modular system to guarantee a very high leak-tightness and media compatibility.
Two N 87 Ex pumps extract sample gas, one on the hydrogen side and the other on the oxygen side. The subsequent analysis shows to what extent hydrogen and oxygen are mixing. To prevent an oxyhydrogen explosion, the volume fraction of hydrogen in oxygen and oxygen in hydrogen is measured. This process is facilitated by the N 87 Ex gas pump, which continuously takes samples.
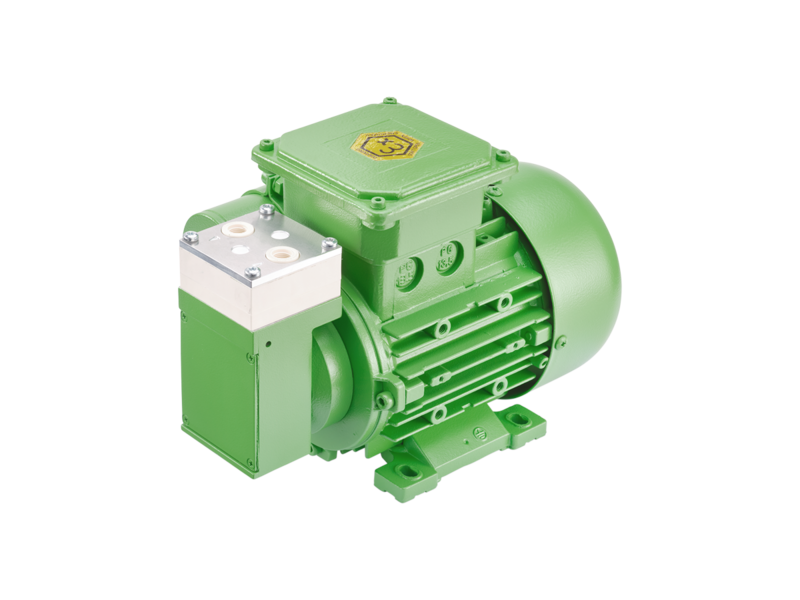
KNF gas sampling pumps operate 24/7, or about 8,000 hours per year.