Any company that has been in business for more than 70 years has valuable traditions and experiences. But when it comes to the competitive international market, you can’t rest on your laurels. By taking a critical look at its established production processes, KNF has been able to discover tremendous untapped potential. At KNF, long-established structures have been replaced with holistic process and organizational technologies. Workplace ergonomics and efficiency were the main focus of the changes made to the pump assembly process at KNF’s German manufacturing location.
“Each pump is only handled once” – this is the new standard for assembly at the KNF Group’s pump manufacturing site in Freiburg-Munzingen, Germany. After recently having nearly doubled the floor space of the assembly facility, the employees began the transition to the so-called one-piece flow method, which increases both productivity and employee motivation. KNF’s production line employees have spent two years intensively working on improving processes and creating their own ideal work environment. Even after just a few weeks, the feedback has been positive all around.
Motivating teamwork and self-management
KNF is a global market leader for diaphragm pumps and has been recognized as an excellent employer. A highly qualified, motivated team is key to the continued success of the company. With the new one-piece-flow in lean production, employees are no longer responsible for the same, repetitive steps, but for a variety of different steps within the process. Employees work in independent teams at workstations stocked with the necessary material and equipped with the most cutting-edge production technologies to fill each order. Every step of the pump assembly process is accompanied by the same employee, including the final quality inspection.
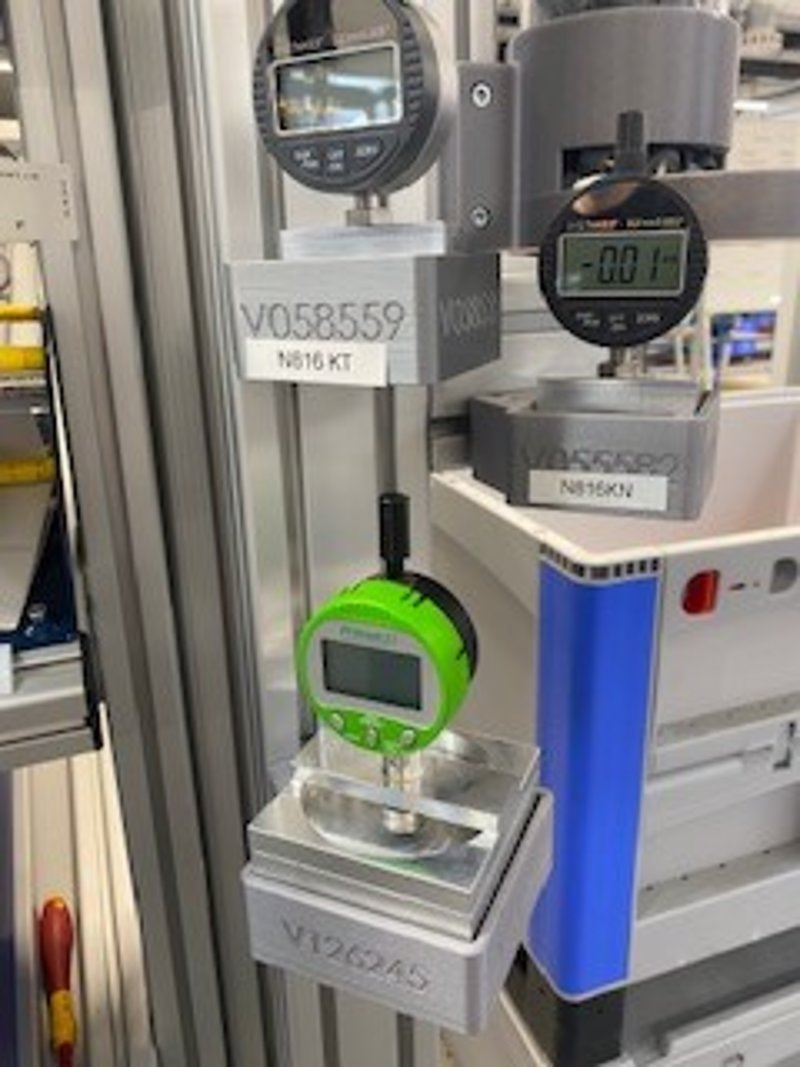
Complete flexibility and workplace ergonomics
KNF’s unique selling point are customized pump solutions starting from a lot size of one. The assembly line has been planned down to the smallest detail to give it the flexibility it needs. Each production line is a u-shaped setup of moveable shelves, and can cover various pump types. When starting a new order, the assembly team adjusts the shelves with the necessary materials to the ergonomically appropriate height for working.
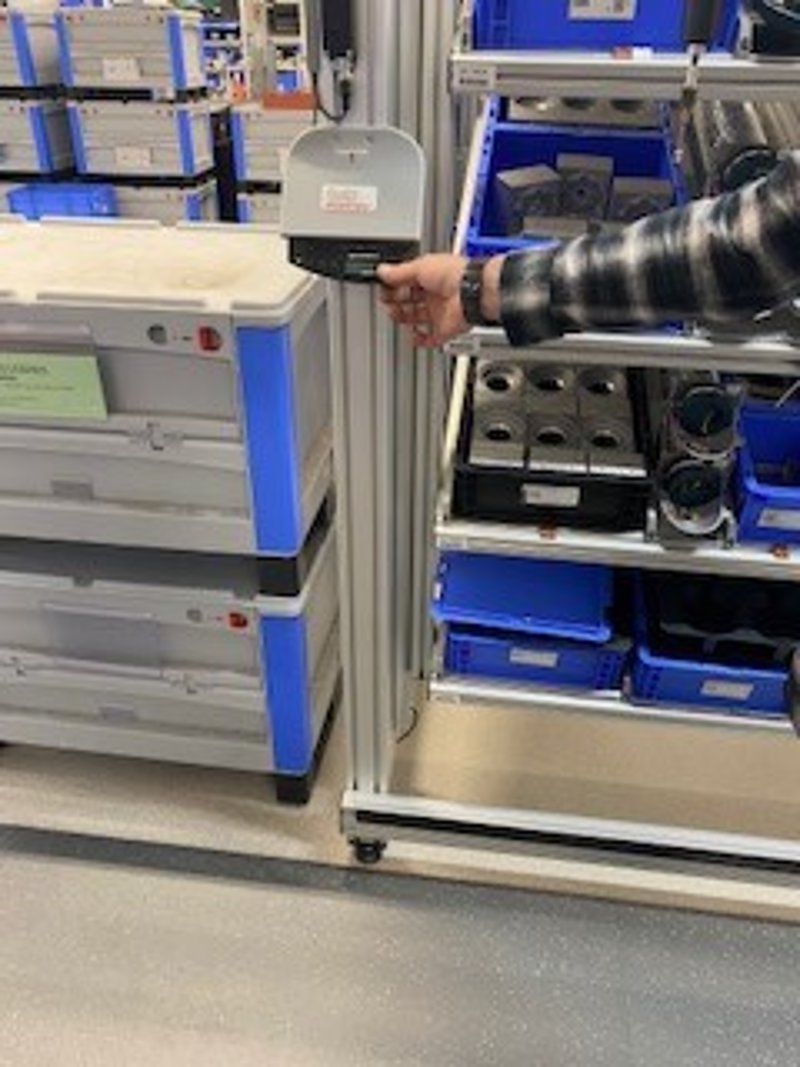
But that’s not all. A moveable, adjustable assembly bench has completely replaced the standard work bench. Employees are able to take this assembly bench with them from the first to last step in the production process. Labor-saving tools, such as an adjustable rotary table with locking mechanism, can be used to position the pump for comfortable assembly. This supports fatigue-free, concentrated working.
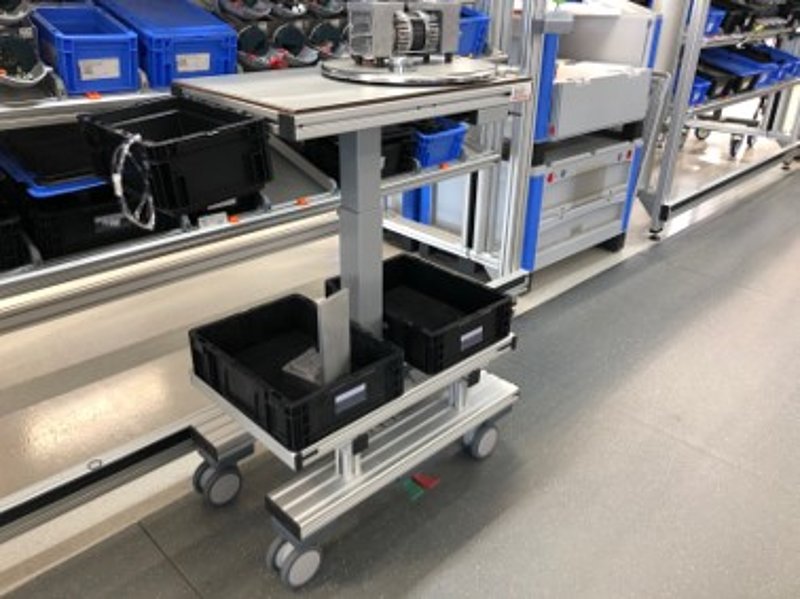
Behind the scenes, the logistics team ensures that enough materials are always available. Materials are easily re-stocked from the outside using filling tubes and storage boxes, while assembly continues inside.
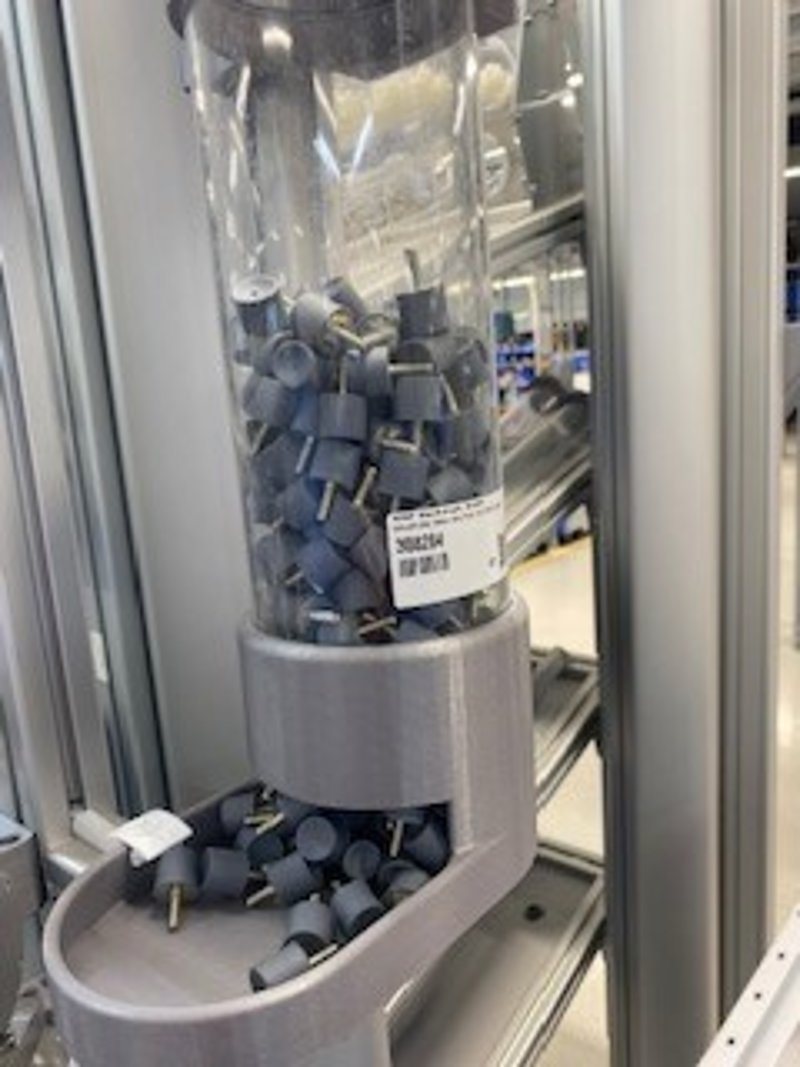
Color coding is used to prevent any mix-ups, and clear categories have been created to avoid any possible confusion. The tools are positioned at working height so that the employee can easily access the tool that is next in line within the assembly process. KNF’s internal production technology team has developed this and many other helpful elements, which have been produced using 3D printing.
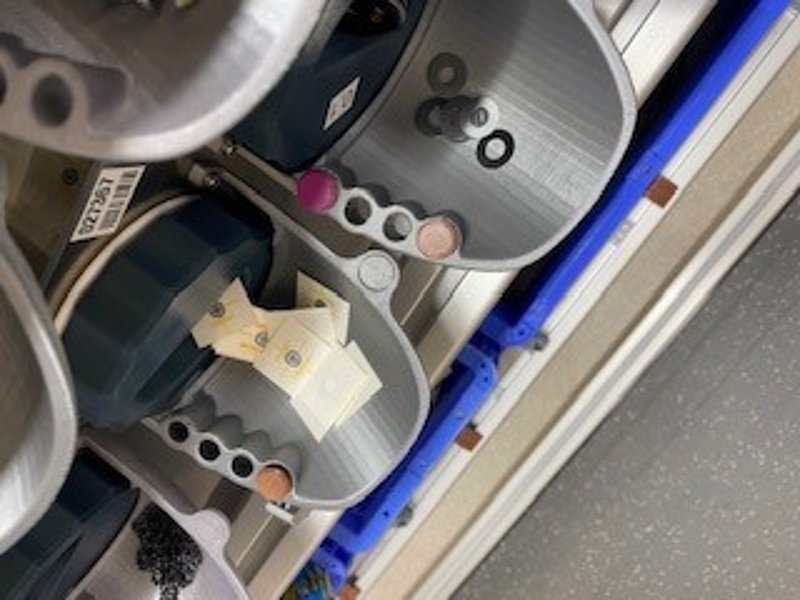
Digitalization – an integral part of the team
Digital protocols are shown on screens which are always in view from anywhere along the assembly line; the production team no longer uses paper. After successful completion of the quality check, each pump is scanned and counted toward the total output. While each assembly team has a daily target, the decision on how to reach this goal is taken within the team. In addition to the simultaneous production of different orders on one line, lot splitting may be used to allow for smaller orders to be fit in at short-notice. The team can work together to complete an order, or assign one team member to be responsible for it. The assembly team actively shapes its own workday by independently planning the completion of the orders assigned to it. The supervisor always keeps an eye on the dashboard to ensure that nothing gets in the way of meeting the daily target.
Built-in efficiency
Staying at the top of a competitive international market requires leveraging local resources. At its German manufacturing site, KNF has implemented the one-piece flow method to arrange everything in the most efficient and resourceful manner, saving time at every step along the way.
Efficiency for employees and customers has been increased though an ergonomically designed material supply, the automatic refilling of materials, independent production teams as well as digital support for working processes. In this way, KNF is able to meet the high demand for customized pump solutions, even as the company continues to grow in the future.
Team spirit that works
After the first few weeks, the assembly teams are enthusiastic about the changes: “We can’t imagine it any other way now,” says one employee. “Being able to stand and move around, or to work more quickly or more slowly, that makes the job a lot more interesting.” The fact that the team has designed and tested its own assembly line and processes has played an important role in how well the changes were received.
KNF’s customers also profit from the new production conditions in Freiburg-Munzingen: shorter delivery times, partial delivery and reliable, excellent quality speak for themselves. By making the transition to lean production, KNF is living up to its reputation as a global market leader and re-defining itself as one of the top employers in the region.