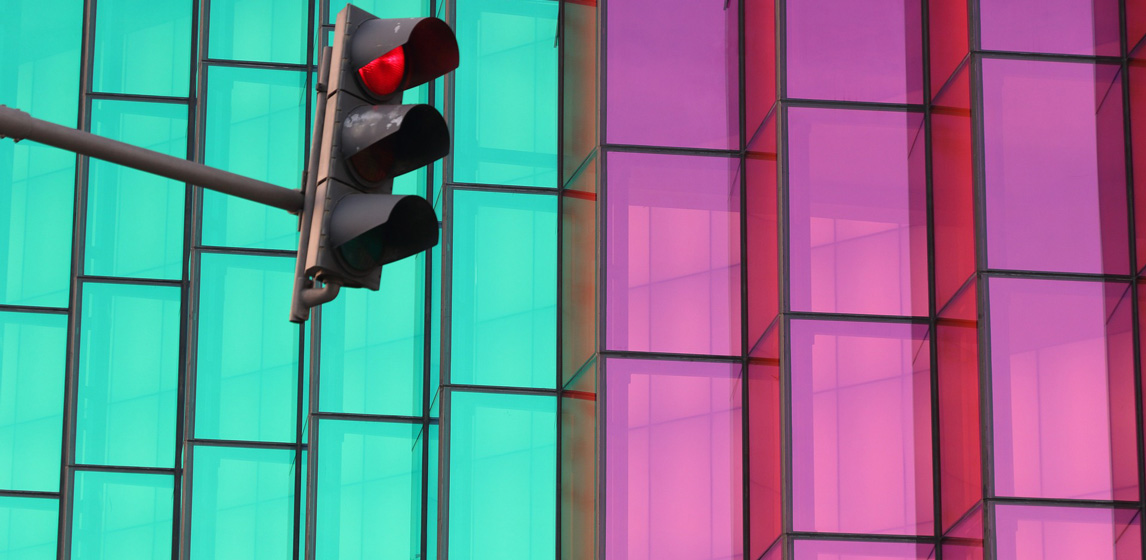
Five Signs of Alarm Before the Pump Fails
A pump in a machine or in a system is naturally expected to provide maximum longevity and reliability. It is no surprise that this component is quickly neglected because it is often only one of many and, in comparison to other laboratory instruments, it is also a cheap component. Added to this is the fact that there is no general information available about maintenance intervals because they are extremely variable depending on the field of application. The pump does require attention now and then.
Laboratory personnel should know how to identify pump wear since, if specific signs make their presence known and nothing is done to follow up on them, this can lead to significant downtimes, costly repairs and total replacement. Even if the maintenance intervals turn out to be variable depending on the application, it may be a good idea to draw up a schedule. This should contain and consider all information about the application and the operating cycle. Some institutions maintain their pumps regularly once a year, while others wait until the pump no longer delivers any pneumatic output or when noise appears. There are some possibilities regarding maintenance; either the pump is sent back to the manufacturer and repaired there, or the pump is repaired in house. Instructions for the replacement of wearing parts are described in detail in our instruction manuals or within special service videos. In any event, it is recommended that regular attention be paid to the following five symptoms during operation:
1. Increased bearing, motor or air noise
Over time every pump shows signs of wear, parts age and fail. Damaged bearings or shaft imbalances, for example, lead to increased operating noise levels. If the pump becomes louder, this is always an indication that the pump needs to be maintained and cleaned. During standard maintenance, the pump’s wearing parts are replaced. In most cases, this involves the elastomer parts, that is, diaphragm(s), valve plates and seals. Elastomer parts can be independently maintained by the customer. A recommendation as to which maintenance intervals should be followed at which time cannot be given since the service life of wearing parts differs completely from application to application: The pneumatic relationships (excess pressure or final vacuum), the conveyed medium and, for example, the media temperature are important indicators for wearing part strain. The operating cycle also plays a role. This differs from laboratory to laboratory. Some pumps are used only once a day or once a week, others run almost around the clock. For this reason, it is important to keep an eye on pump use when it comes to maintenance.
When bearing, motor or air noise is heard, the pump must be sent back to the manufacturer. These symptoms are indicative of problems beyond the expected abilities of the customer and the diagnosis and maintenance of the problems should be performed by the manufacturer.
2. Longer processing or drying times
Diaphragms and valves do have a long service life, but they are wearing parts. In case of dirt, for example, the pump’s conveying capacity and the final vacuum are affected. If there is dirt in the inner areas of valves, this will compromise valve performance and reduce the pump’s total efficiency. The pump needs more time to carry out standard applications than when it is new. In this case, diaphragms and valves should be replaced and dirty surfaces cleaned to re-establish the customary output. If the pump’s inner areas had to be cleaned, one should investigate the source of the dirt that reached the pump’s inlet side. A diaphragm vacuum pump draws in the conveyed medium and if it contains particles or other chemical substances, these can settle on the valves and affect operation adversely. A solution would be to connect an upstream particle filter. Once the dirt source is eliminated, the pump will return to its usual output.
3. Overheating with shutdown and restart after pump cool-down
Overheating can have different causes: poor ventilation, incompatible current source or wrong motor assembly. First, it is good if the pump manufacturer has outfitted its laboratory pumps with an over temperature safety switch to prevent damage and to ensure safety. Overheating is a sign that a pump is incorrectly cooling, incorrectly working or attempting to deliver the required output in a specific application. The first thing to check, therefore, is the ventilation openings on the pump housing. Are they blocked or too close to a wall? If the pump is properly ventilated and the power supply is suitable for the device, overheating is an indication of motor problems. This pump should be sent to the manufacturer for a more detailed repair analysis.
4. Blown-out fuses
Due to overload or power failure the pump switches off and does not restart. If a fuse burns out, the pump was either exposed to an uncontrolled power surge or the power supply is incompatible because the selected voltage was too high, for example. If these two factors do not apply, a short circuit or a motor malfunction is the cause. If the fuses blow out regularly, the pump should be sent to the manufacturer for further assessment.
5. Slow start or standstill
If a pump exceeds its capabilities when started against vacuum or pressure and the pump even comes to a standstill, there may be a flow restriction or blockage at the pump inlet and outlet opening. Another cause could be a weak or damaged motor or motor capacitor.
Depending on the pump model, starting a pump against an inlet vacuum or an outlet pressure can be an improper application. Under these conditions the pump can come to a standstill or start up slowly, the fuses overheat and burn out. Make sure that inlet and outlet lines are vented before start-up and the valves and connections have no obstructions or dirt. If the device is normally able to work in this application, this can be a sign of a weakened motor or start capacitor.
The diaphragm pump is an extremely reliable and durable component. With a little attention and maintenance, the user can keep it that way.
Based on Five Signs You Should Service or Replace Your Diaphragm Vacuum Pump, The Pump Post, 2013
75 Years: KNF Celebrates Company Anniversary
A treasure chest filled with memories, facts and stories. Learn more about KNF’s company history.
Anniversary Blog