For valid soot particle measurements: Portable calibrating system for measuring instruments in accordance...
Water, the Natural Enemy of Watches
KNF’s swing piston compressor and Bürkert’s valve module test the waterproofness of watches
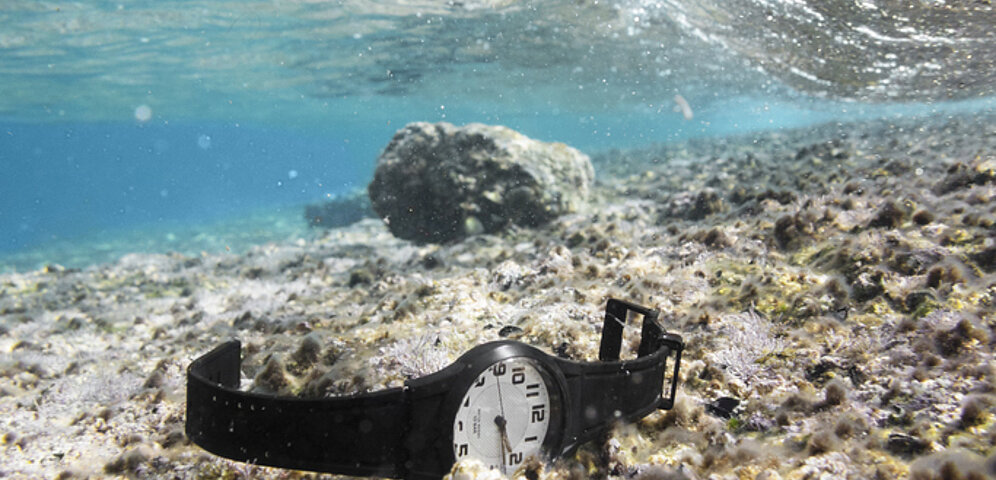
Waterproof up to 5 bar, 5 atm or 50 meters – almost all watches have an inscription of this kind.
But what does that actually mean? Was the watch actually submerged in water to check if it’s water tight?
Obviously not. The watch is tested non-destructively, using air. The integrated valve module combines the valve technology competence of Christian Bürkert GmbH & Co. KG with the compressor know-how of KNF.
Waterproof according to test standards ISO 2281 and ISO 6425
The leaflet states whether a watch is watertight and how much pressure it can resist. But how long it will actually stay watertight is difficult to predict. The reference point for its waterproofness, which is determined according to test standards, is therefore always its new condition.
Regular watches are tested for waterproofness according to the ISO 2281 standard, while diver’s watches are tested following the ISO 6425 standard. The watch is subjected to a pre-determined pressure for a certain amount of time. If the watch withstands the pressure, it is tight – at least at the point of testing.
3, 5, 10 or 20 – the number on the watch case back tells the watchmaker how much overpressure must be applied to meet the test standards.
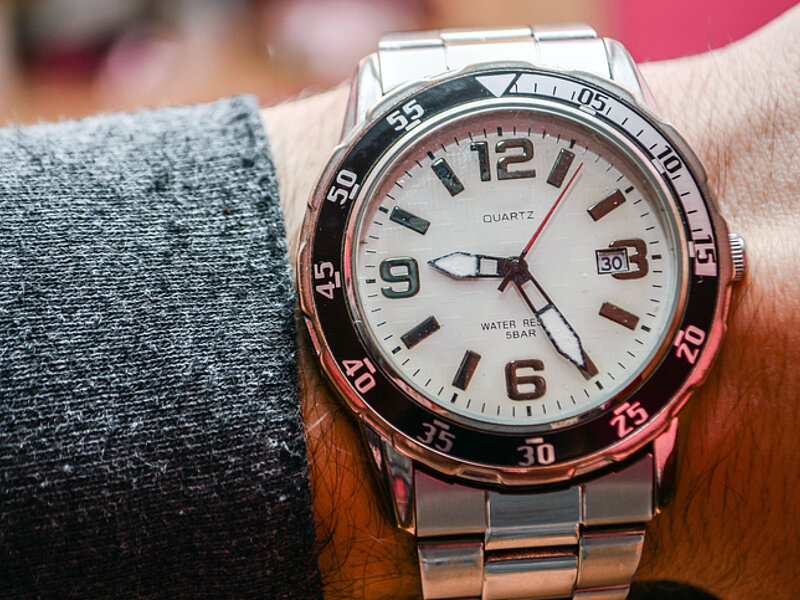
Periodic water-pressure testing
The information provided in bar, atm or meters is nothing more than a snapshot and therefore only intended as an indication. The specification of 3 bar, 3 atm or 30 meters means that the watch is resistant to sweat or splash water. Only watches with the specification of 5 bar, 5 atm or 50 meters remain watertight during bathing or swimming.
Nevertheless, a watch’s waterproofness should be tested about once per year, as the sealing elements age and become brittle. The water-pressure test with compressed air is therefore a standard step during service and repairs or when the battery is replaced.
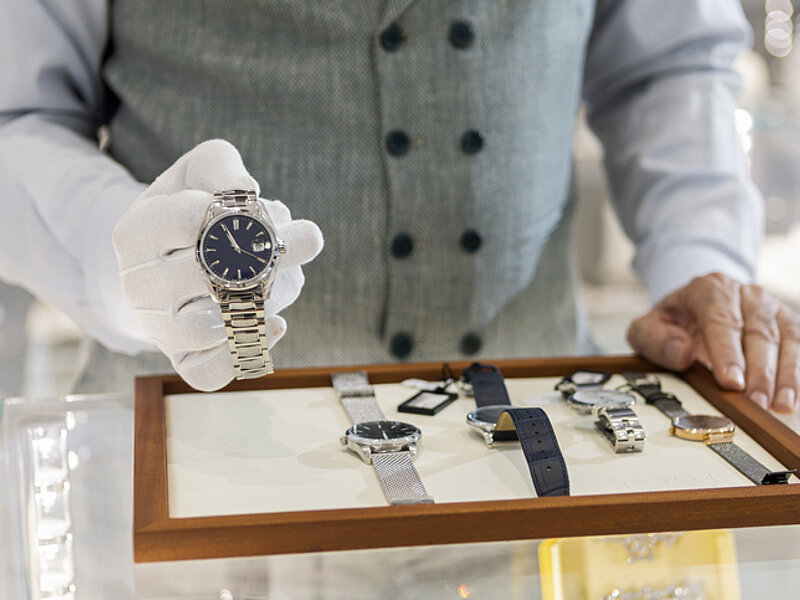
Measuring the watch case’s deformation
The water-pressure test involves measuring the deformation of the watch case. Its re-expansion depends on the free volume of the watch. If there is a leak, it means the correlation between re-expansion and deformation is disturbed and the measuring process is interrupted.
Bürkert’s valve module for water-pressure testing of up to 5 bar overpressure
A pneumatic module in the tester is used to control the leak test. This module, which is made of customer-specific injection molded plastic parts as well as 2/2-way valves and a compressor, is produced by Bürkert.
The individual valves control the process and, among other things, switch the compressor to a loadless state. The compressor starts up smoothly, and once the maximum pressure has been reached, the valve blocks the test chamber, taking the load off the compressor.
Using the tester, the pressure is regulated to the defined pressure level of, e.g., 5 – 3 – 1 bar. These pressure levels adhere to the different requirements for water-pressure tests. The measured values are recorded at the respective pressure level.
The pressure vessel is made of aluminum. This light metal is a good heat conductor and quickly dissipates the heat generated by the overpressure.
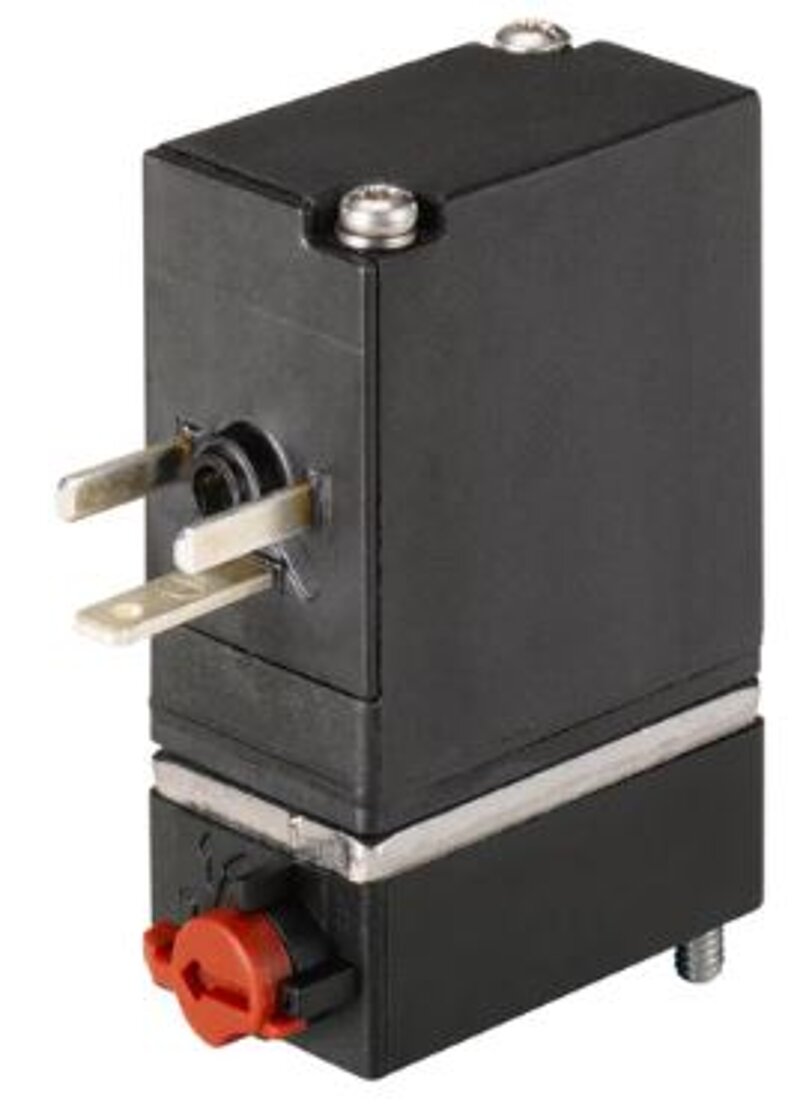
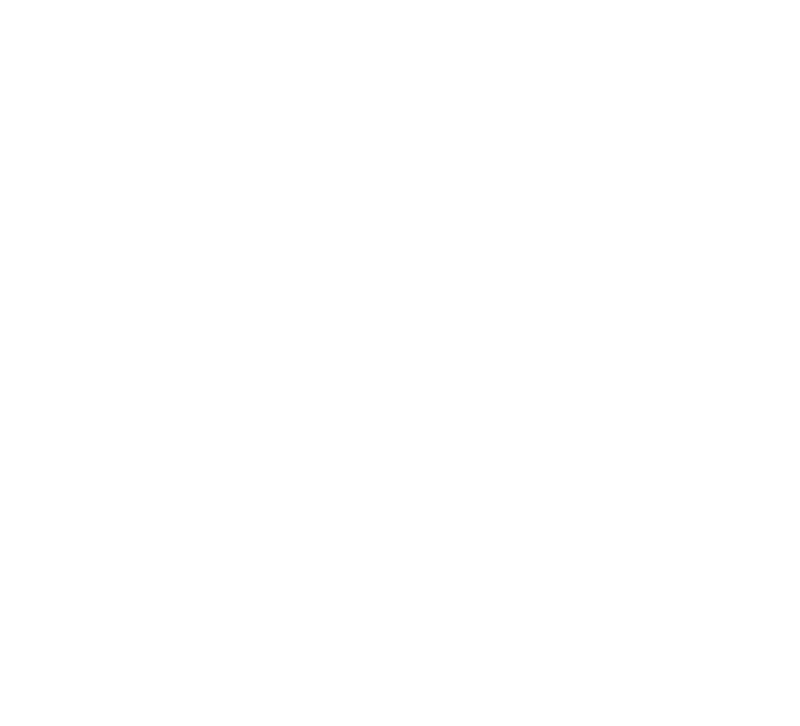
KNF’s compressor replaces external compressed air for the pressure test
Performing water-pressure tests in a watch repair shop or retail store requires an independent compressed air supply. Since an external compressed air connection is usually too expensive, Bürkert relies on KNF’s high-performing NPK 06 series compressor for this application.
The pump is flanged directly to the Bürkert valve module via a manifold, making hose connections and ports, which could leak during the measurement, dispensable. The connection via the manifold is an application-specific modification of the pump’s series model.
When used for this application, the pump fulfills further requirements. The test pressure of 5 bar must be reached within a specified short period, which is no problem for the NPK 06. Although it is small and compact, it is a true mighty mite. Its brushless, durable motor with an optimal torque for this task gives it a special advantage.
Furthermore, the dead volume of the NPK 06’s suction chamber was enlarged, and a reduced eccentric was installed. This modification prevents the motor from overheating and avoids load cut-offs.
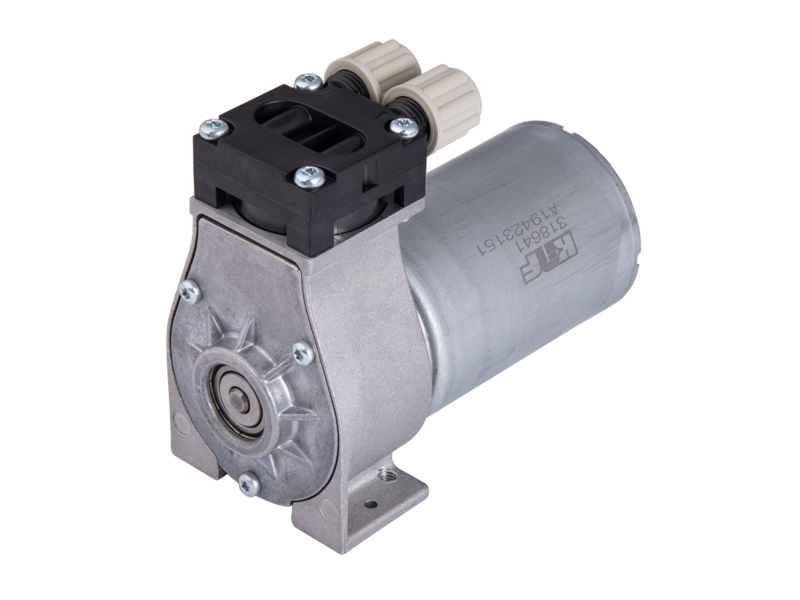