KNF pompen recyclen lucht aan boord van het ISS
KNF-pompen in 3D-zandprinting
Smart Slab ontwikkeld in een innovatief architectuurproject door onderzoekers van ETH Zürich
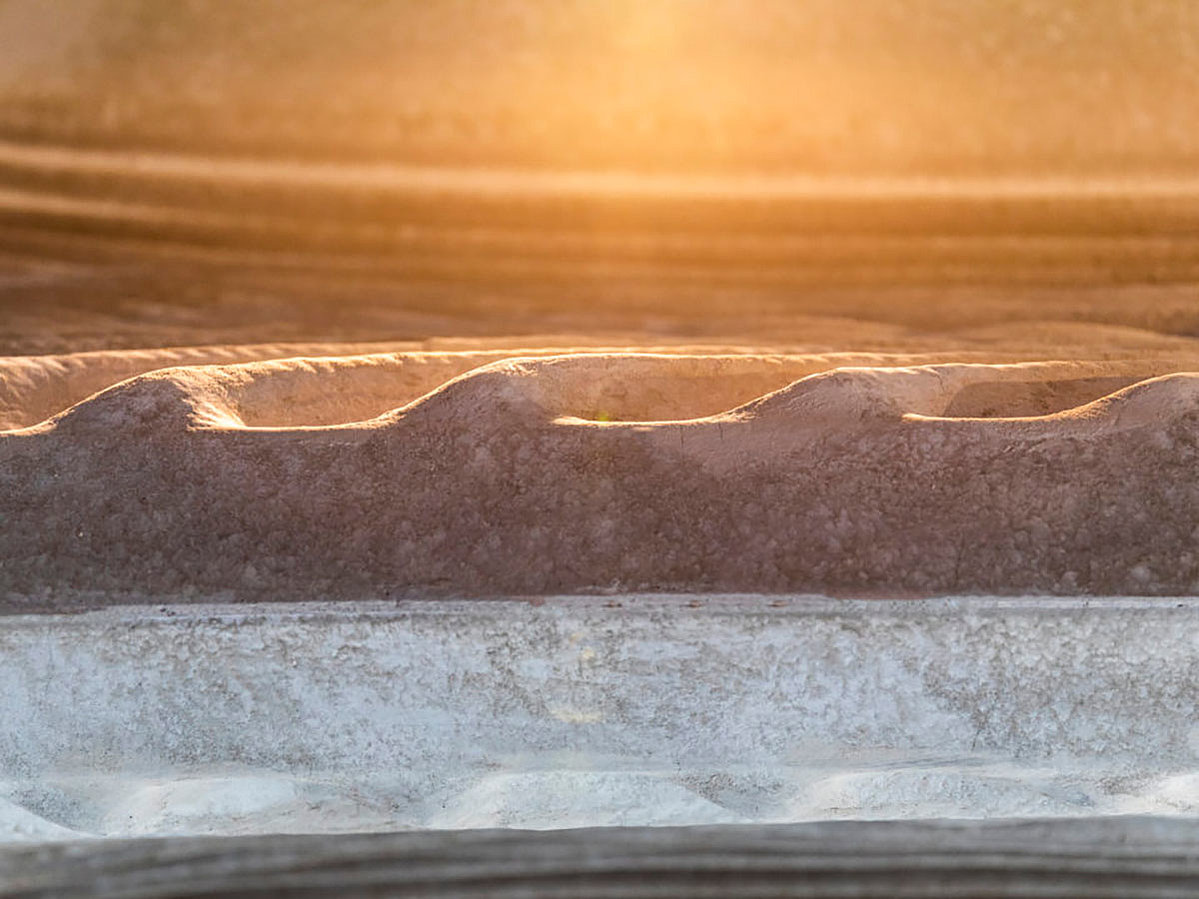
Onderzoekers van ETH Zürich produceren in het kader van het architectuurproject Smart Slab een lichtgewicht, intelligent betonnen plafond. De Zwitserse universiteit gebruikt een innovatieve productiemethode om de bekisting van de platen te maken met een 3D-zandprinter van Voxeljet AG, Friedberg (Duitsland), uitgerust met KNF-pompen.
De voordelen van digitale productie
Het Smart Slab intelligente plafond combineert de structurele sterke punten van beton met de flexibele ontwerpmogelijkheden van 3D-printing. Deze digitale productiemethode is veel kostenefficiënter en milieuvriendelijker dan de constructie van massieve plafonds. Op zijn dunst is de Smart Slab slechts 20 millimeter dik, zonder verlies van stabiliteit. Dit betekent dat het gewicht van de schalen minder dan 50 procent bedraagt van het gewicht van een conventioneel plafond, wat resulteert in een lager materiaalverbruik. Dit verlaagt niet alleen de productiekosten, maar zorgt ook voor een kleinere ecologische voetafdruk.
De oorsprong van het project
De Smart Slab is ontwikkeld bij ETH Zürich in opdracht van Benjamin Dillenburger, assistent-professor voor digitale constructietechnologie. Het is een van de kernelementen van het DFAB-huis en werd in de zomer van 2018 geïnstalleerd in het onderzoeks- en innovatiegebouw NEST van Empa en Eawag in Dübendorf. Het plafond, dat uit elf betonnen segmenten bestaat die de kelder met de twee verdiepingen tellende houten structuur erboven verbinden, meet 80 m2 en weegt 15 ton..
Zo weinig mogelijk beton
De Smart Slab-onderzoekers gebruikten 3D-printing niet om de constructie-elementen zelf te produceren, maar hun bekisting - d.w.z. de negatieve mal. Ze werkten met een grootformaat 3D-zandprinter van Voxeljet. Deze bevat twee KNF-membraanvloeistofpompen, die elk verantwoordelijk zijn voor de aanvoer van koud bindmiddel (NF 60 KT DC) en de afvoer van overtollige grondstof (NF 60 KT DC). De vervaardiging van de bekisting is de meest arbeidsintensieve stap in de betonbouw, met name voor niet-standaard onderdelen.
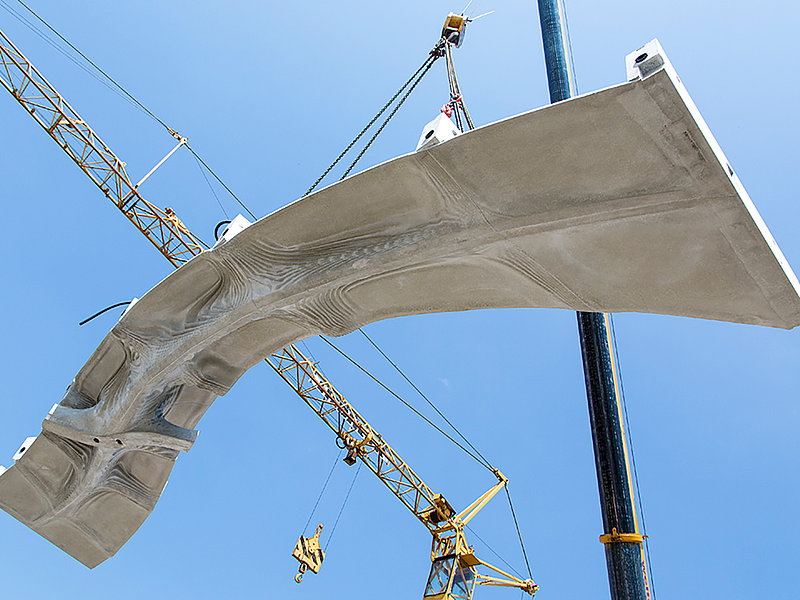
Vervaardiging met een druk op de knop
Nadat de computerplanning was afgerond, kwamen de industriële partners van de Smart Slab-onderzoekers in actie. Een van hen produceerde de hoge-resolutie 3D-zandprintbekisting, terwijl een andere partner CNC-lasersnijders gebruikte om de houten bekisting te maken. Dit geeft de bovenzijde van de Smart Slab zijn vorm en omvat ook holtes om het materiaalgebruik en het gewicht te verminderen en ruimte te maken voor elektrische kabels. De twee soorten bekisting kwamen vervolgens bijeen bij het derde partnerbedrijf voor het storten van beton. Dit bedrijf injecteerde eerst het vezelversterkte beton in de zandprintbekisting om het fijn geribbelde oppervlak van de onderste betonschaal te produceren, waarna het de rest van de Smart Slab met behulp van de houten bekisting stortte.
Uitstekende resultaten dankzij pre-planning
Na twee weken uitharding waren de elf afzonderlijke betonsegmenten klaar voor transport naar het DFAB-huis. De zorgvuldige planning en pre-fabricage, evenals de keuze van deskundige partners en betrouwbare technologieën, zorgden ervoor dat het project zonder enige vertraging met succes werd afgerond. "Het was overweldigend om te zien hoe naadloos onze elementen op de bouwplaats en op de bestaande onderdelen van het DFAB-huis op elkaar aansloten", aldus Dillenburger. "Dit zou niet mogelijk zijn geweest zonder de uitstekende interdisciplinaire samenwerking met onze partners."