Membranpumpen und Zahnradpumpen im Vergleich
Bei der Auswahl der idealen Pumpe für eine bestimmte Anwendung kommen Zahnrad- und Membranpumpen häufig in die engere Wahl. Jeder dieser Pumpentypen hat seine eigenen Eigenschaften, Vorteile und Anwendungsgrenzen.
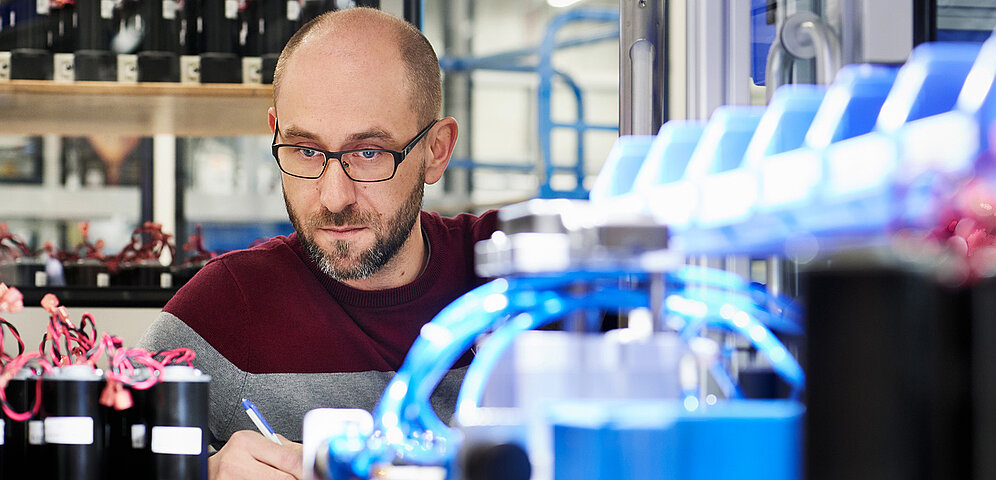
Insbesondere für Flüssigkeitsanwendungen können sowohl Zahnrad- als auch Membranpumpen geeignete Optionen darstellen. Durch den Vergleich der Membran- und Zahnradpumpentechnologie und die Kenntnis ihrer Eigenschaften wie Wartungsanfoderungen, Förderrate und Zuverlässigkeit lässt sich die für die jeweilige Aufgabe am besten geeignete Pumpe ermitteln.
Wie funktioniert eine Zahnradpumpe?
Zahnradpumpen arbeiten nach einem einfachen Prinzip. Sie verwenden rotierende Zahnräder, um die Flüssigkeit durch die Kammern zwischen den Zähnen zu befördern. Durch das Ineinandergreifen der Zahnräder entsteht ein Sog und Druck, der die Flüssigkeit vom Saugstutzen zum Druckstutzen befördert. Im Allgemeinen gibt es zwei Arten von Zahnradpumpen: Innenzahnradpumpen, die für viskose Flüssigkeiten mit Feststoffanteilen geeignet sind, und Außenzahnradpumpen, die besser Flüssigkeiten mit niedriger Viskosität fördern.
Sie decken ein breites Spektrum von Anwendungen in verschiedenen Branchen ab, von der medizinischen Diagnostik wie der Durchflusszytometrie bis hin zu Druck- und Industrieanwendungen. In der chemischen Industrie werden sie beispielsweise zum Transfer von Harzen, Pigmenten und Polymeren eingesetzt. Auch Branchen wie die Lackindustrie und das Baugewerbe verlassen sich auf ihre Fähigkeit, viskose Medien zu bewegen. In der Mineralölindustrie transportieren Zahnradpumpen Öle und Kraftstoffe. Und selbst in der Lebensmittelindustrie kommen Zahnradpumpen zum Einsatz – zum Beispiel um Sirup, Cremes und Melasse zu transportieren.

Funktionsweise von Membranpumpen
Membranpumpen arbeiten ebenfalls nach einem einfachen Prinzip: Ein Pleuel bewegt eine Elastomermembran auf und ab. Beim Absenken der Membran wird die Flüssigkeit durch das Einlassventil angesaugt und beim Aufwärtshub durch das Auslassventil ausgestoßen. Diese Konstruktion macht sie selbstansaugend, trockenlaufsicher und äußerst vielseitig, so dass sie eine breite Palette von Flüssigkeiten und Gasen fördern können.
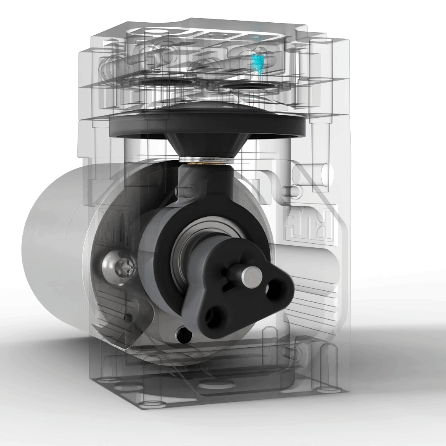
Sie eignen sich hervorragend für die Förderung einer Vielzahl gasförmiger und flüssiger Medien, einschließlich viskoser, abrasiver oder scherempfindlicher Flüssigkeiten. Ihre hohe Betriebssicherheit durch die vollständige Trennung des Fördermediums von den mechanischen Teilen macht sie ideal für den Einsatz in anspruchsvollen Umgebungen oder für Anwendungen mit aggressiven oder gefährlichen Medien. Branchen, die vielseitige Pumplösungen benötigen, entscheiden sich aufgrund ihrer Flexibilität und Zuverlässigkeit häufig für Membranpumpen.
Membranpumpen und Zahnradpumpen im Vergleich: Kosten und Zuverlässigkeit
Beim Vergleich von Zahnradpumpen und Membranpumpen spielen neben dem Anschaffungspreis mehrere Faktoren eine entscheidende ökonomische Rolle. Insbesondere der Wartungsaufwand und der Energieverbrauch sind entscheidend. So müssen herkömmliche Zahnradpumpen in der Regel häufiger gewartet werden, da ihre rotierenden Zahnräder, die in ständigem Kontakt mit der Flüssigkeit stehen, verschleißen. Mit fortschreitender Abnutzung der Zahnräder sinkt der Wirkungsgrad der Pumpe, was zu schwankenden Fördermengen, internen Leckagen oder Ausfällen führen kann. Die Wartung einer Zahnradpumpe kann zudem komplexer sein und insbesondere für den Austausch von Zahnrädern oder Dichtungen spezielle Kenntnisse oder geschultes Personal erfordern, was zu längeren Ausfallzeiten führen kann.
Membranpumpen arbeiten mit weniger Reibung, da die Flüssigkeit durch eine flexible Membran bewegt wird und nicht durch mechanische Teile, die sich direkt berühren. Auch Membranen und Ventile können je nach Medienverträglichkeit mit der Zeit verschleißen, sind aber bei einem modularen Pumpenaufbau leicht austauschbar. Die Möglichkeit einer detaillierten kundenspezifischen Anpassung und die Auswahl aus verschiedenen Membran- und Ventilwerkstoffen gewährleisten eine bestmögliche Kompatibilität auch bei aggressiven oder abrasiven Fördermedien. Das Risiko interner Leckagen oder Leistungsschwankungen ist daher geringer.
Förderrate und Pulsationseigenschaften
Sowohl Zahnrad- als auch Membranpumpen sind in der Lage, hohe Förderraten zu liefern, unterscheiden sich jedoch erheblich hinsichtlich Pulsation und der Gleichmäßigkeit ihrer Förderrate. Zahnradpumpen liefern einen gleichmäßigen, kontinuierlichen Förderstrom mit sehr geringer Pulsation, da die Zahnräder kontinuierlich ineinandergreifen und so einen gleichmäßigen, nicht schwankenden Flüssigkeitsstrom erzeugen. Dies macht Zahnradpumpen ideal für Anwendungen, bei denen ein gleichmäßiger Förderstrom entscheidend ist.

Membranpumpen können zwar hohe Förderraten erreichen, neigen aber aufgrund der Hubbewegung ihrer Membranen zu stärkerer Pulsation. Diese lässt sich jedoch durch innovative Konzepte wie Mehrmembrankonfigurationen oder integrierte Dämpfer minimieren. Mit der Smooth Flow Technology von KNF wird die Pulsation auf ein kaum wahrnehmbares Maß reduziert, so dass Membranpumpen in vielen Anwendungen Zahnrad- und Schlauchpumpen ersetzen können, wobei die einzigartigen Vorteile von Membranpumpen erhalten bleiben. Sie können auch in so wichtigen Bereichen wie der Durchflusszytometrie eingesetzt werden, wo ein besonders gleichmäßiger Fluss erforderlich ist.
Druck- und Ansaugfähigkeit
Standardausführungen von Membranpumpen wie der KNF FP 1.400 erreichen einen maximalen Druck von 6 bar (rel.). Daher werden Membranpumpen meist in Anwendungen eingesetzt, bei denen ein hoher Maximaldruck nicht die primäre Anforderung ist. Zahnradpumpen zeichnen sich hingegen dadurch aus, dass sie höhere Förderdrücke zwischen 100 und 300 bar erreichen können, wodurch sie sich für Anwendungen wie Hydrauliksysteme und Kraftstoffeinspritzung eignen.

Ein großer Vorteil von Membranpumpen ist ihre hohe Ansaugleistung. Dadurch kann die zu transportierende Flüssigkeit ohne externe Unterstützung in die Pumpe gesaugt werden – die Pumpe ist also selbstansaugend. Diese Eigenschaft macht sie ideal für Anwendungen, bei denen die Pumpe trocken anlaufen oder einen unregelmäßigen Förderstrom bewältigen muss. Außerdem sind Membranpumpen weniger anfällig für Kavitation, die in einigen Anwendungen ein Problem darstellen kann. Zahnradpumpen hingegen haben im Allgemeinen ein geringeres Saugvermögen und sind daher oft nicht selbstansaugend. Sie sind auch anfälliger für Kavitation, da ihre oft schnell drehenden Zahnräder ähnlich einer Turbine interne Turbulenzen in der Flüssigkeit erzeugen können.
Flüssigkeitsqualität während des Transports aufrechterhalten
Zahnradpumpen können bei bestimmten Anwendungen aufgrund des möglichen Verschleißes ihrer internen Komponenten eine problematische Kontamination der Flüssigkeit auslösen. Im Laufe der Zeit können die Zahnräder verschleißen, wodurch sich Partikel oder kleine Fragmente davon lösen und die Flüssigkeit oder das System verunreinigen können. Dies kann die Qualität der gepumpten Flüssigkeit beeinträchtigen und zu einem Leistungsabfall oder sogar zum Ausfall des Systems führen.
Membranpumpen hingegen haben keine beweglichen Dichtungen oder inneren Teile, die aneinander reiben können, wodurch das Risiko von Verunreinigungen minimiert wird. Dies gewährleistet eine sauberere und zuverlässigere Förderung und macht Membranpumpen ideal für Anwendungen, bei denen die Reinheit des Fördermediums von entscheidender Bedeutung ist.
Einsatz bei partikelhaltigen und scherempfindlichen Medien
Zahnradpumpen sind in der Regel nicht für die Förderung von partikelhaltigen oder scherempfindlichen Flüssigkeiten geeignet. Durch die engen Toleranzen zwischen den Zahnrädern können Partikel eingefangen und zerquetscht werden, was zu Beschädigungen und Leistungseinbußen führen kann. Die mechanische Wirkung der Zahnräder setzt die Flüssigkeit außerdem Scherkräften aus, so dass Zahnradpumpen für Anwendungen mit scherempfindlichen Medien wie bestimmten Chemikalien, Emulsionen oder biologischen Materialien weniger geeignet sind. In Anwendungen wie der Übertragung von UV-Tinte für die Inkjet-Industrie kann die bei Zahnradpumpen häufiger auftretende Kavitation zu einer vorzeitigen Aushärtung der Tinte führen, die anschließend im System aushärtet oder verklumpt. Diese Wechselwirkungen können langfristig die Integrität der Flüssigkeit beeinträchtigen oder zu Verschleiß an der Pumpe selbst führen. Bei einigen Anwendungen, wie zum Beispiel bei der Förderung von wachsbasierten Farben, können diese hohen Scherkräfte jedoch auch von Vorteil sein, da der Pumpvorgang einer Zahnradpumpe wie ein zusätzliches Rührwerk wirkt.
Membranpumpen eignen sich besser zur Förderung von partikelhaltigen und scherempfindlichen Medien. Ihre Konstruktion minimiert den Kontakt zwischen Flüssigkeit und beweglichen Teilen und verhindert so, dass Feststoffpartikel zerquetscht oder beschädigt werden. Darüber hinaus erzeugt der Pumpvorgang nur geringe Scherkräfte, was ideal für Anwendungen mit sensiblen oder scherempfindlichen Materialien ist. Durch diese schonende Behandlung wird außerdem Kavitation vermieden, wodurch Membranpumpen äußerst zuverlässig bei der Förderung von Flüssigkeiten sind, die während des gesamten Fördervorgangs intakt bleiben müssen.
Die richtige Pumpe für jede Anwendung finden
Bei der Wahl zwischen Zahnrad- und Membranpumpen sind mehrere Faktoren zu berücksichtigen, wie beispielsweise die Eigenschaften der zu fördernden Medien, einschließlich ihrer Viskosität, Abrasivität und Scherempfindlichkeit. Darüber hinaus ist es wichtig, die Betriebsbedingungen zu bestimmen – insbesondere die Notwendigkeit des Trockenlaufs. Außerdem ist zu berücksichtigen, ob ein konstanter Förderstrom erforderlich ist oder ob die Pumpe in der Lage sein muss, variable Förderströme zu bewältigen.
Durch die Bewertung dieser Faktoren und die Kenntnis der Stärken und Grenzen jedes Pumpentyps, lässt sich die beste Option für bestimmte Anwendungen ermitteln.