KNF Pumpen bereiten Luft an Bord der ISS auf
3D-Sanddruck mit KNF Pumpen
Forschende der ETH Zürich haben im Rahmen eines innovativen Architekturprojekts „Smart Slab“ entwickelt
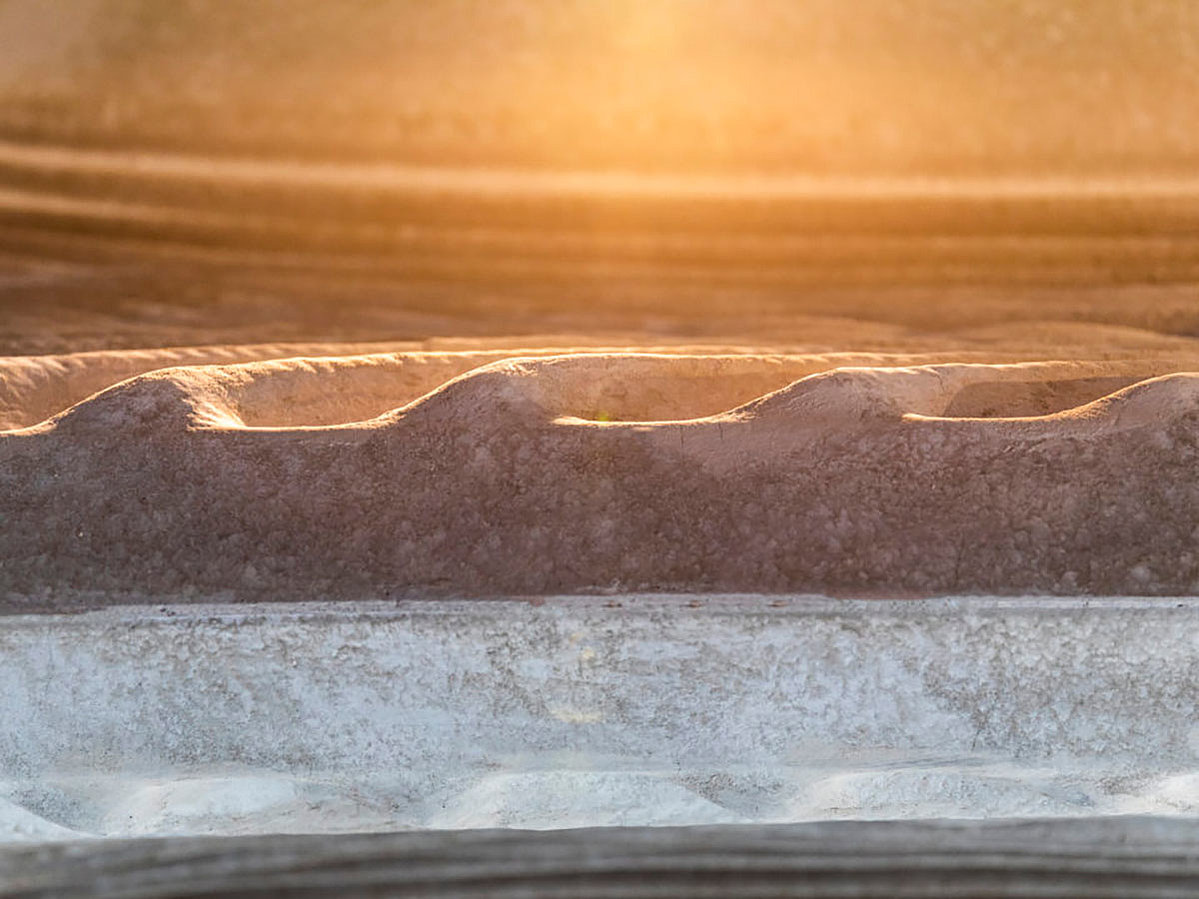
Forschende der ETH Zürich haben im Rahmen des „Smart Slab“-Architekturprojekts eine „intelligente“ Leichtbau-Geschossdecke aus Beton entwickelt. An der Schweizer Universität kam eine innovative Fertigungsmethode zum Einsatz, um die Schalung der Decke herzustellen. Dabei wurde ein 3D-Sanddrucker der Voxeljet AG (Friedberg) verwendet, der mit KNF Pumpen ausgestattet war.
Die Vorteile der digitalen Fertigung
Die Decke kombiniert die bautechnischen Stärken von Beton mit den flexiblen Gestaltungsmöglichkeiten des 3D-Drucks. Die digitale Fertigungsmethode ist deutlich kosteneffizienter und umweltfreundlicher als der Bau von Massivdecken. An den dünnsten Stellen ist die Smart Slab gerade einmal 20 Millimeter dick, ohne dabei etwas von ihrer Stabilität einzubüßen. Das bedeutet, dass sie weniger als halb so schwer ist wie eine konventionelle Decke und damit auch einen geringeren Materialverbrauch aufweist – was nicht nur die Kosten senkt, sondern auch die CO2-Bilanz verbessert.
Die Ursprünge des Projekts
Die Smart Slab wurde an der ETH Zürich unter Leitung von Benjamin Dillenburger, Assistenzprofessor für Digitale Bautechnologien, entwickelt. Es ist eines der Kernelemente der Wohneinheit des DFAB House und wurde im Sommer 2018 im Forschungs- und Innovationsgebäude NEST der Empa und Eawag in Dübendorf montiert. Die 80 m2 große und 15 Tonnen schwere Decke setzt sich aus insgesamt elf Betonsegmenten zusammen und verbindet das Untergeschoss mit dem darüber liegenden zweistöckigen Holzbau.
So wenig Beton wie möglich
Bei der Smart Slab fertigten die Forschenden nicht die Bauelemente selbst mit 3D-Druck, sondern deren Schalung, also die Negativform. Sie arbeiteten dafür mit einem großformatigen 3D-Sanddrucker von Voxeljet. Dieser enthält zwei KNF Membran-Flüssigkeitspumpen, die für die Bereitstellung von Kaltbindemittel (NF 60 KT DC) beziehungsweise für die Entfernung überschüssigen Rohmaterials (NF 60 KT DC) sorgten. Die Produktion der Schalung ist der arbeitsintensivste Schritt im Betonbau, insbesondere bei nicht-standardisierten Bauteilen.
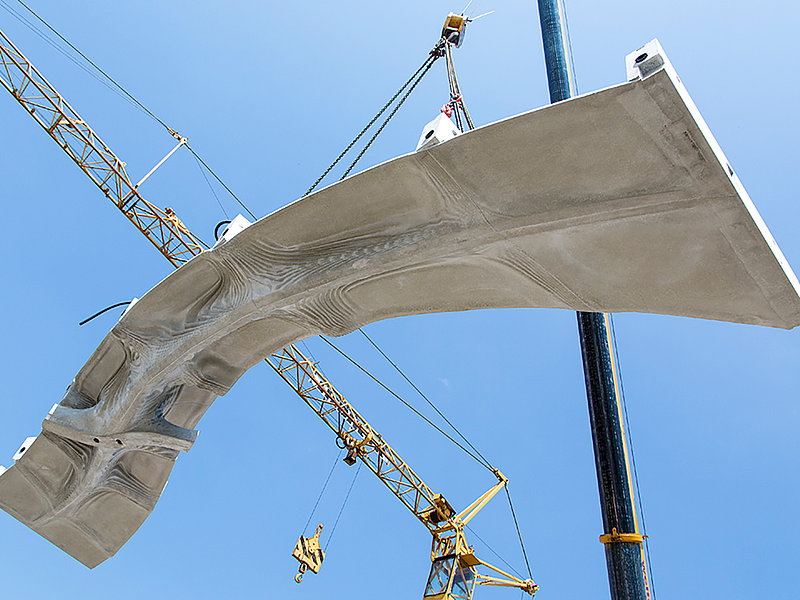
Fertigung auf Knopfdruck
Sobald die Planung am Computer abgeschlossen war, kamen die Industriepartner der Smart Slab-Forschenden ins Spiel: Einer produzierte die hochaufgelösten 3D-Sanddruckschalungen, ein anderer die Holzschalung mittels CNC-Lasercutter. Letztere gibt der oberen Seite der Smart Slab-Decke die Form und spart Hohlräume aus, um Material und Gewicht zu sparen und gleichzeitig Platz für elektrische Leitungen zu schaffen. Anschließend kamen die beiden Schalungstypen für die Betonierung bei einer dritten Firma zusammen. Diese spritzte erst den faserverstärkten Beton in die Sanddruckschalungen, um die fein gerippte Oberfläche der unteren Betonschale herzustellen, und goss danach den Rest der Smart Slab-Decke in die Holzschalung.
Außergewöhnliche Ergebnisse dank Planung im Vorfeld
Nach zweiwöchiger Aushärtung waren die elf individuellen Betonsegmente bereit für den Transport zum DFAB House. Dank der präzisen Planung und Vorfertigung und der Auswahl fachlich versierter Partner und zuverlässiger Technologien konnte das Projekt ohne Verzögerungen erfolgreich abgeschlossen werden. „Zu sehen, wie nahtlos sich unsere Elemente auf der Baustelle aneinander und an die bereits bestehenden Bestandteile des DFAB House fügten, war überwältigend“, sagt Dillenburger. „Ohne die großartige interdisziplinäre Zusammenarbeit mit unseren Partnern wäre das nicht möglich gewesen.“