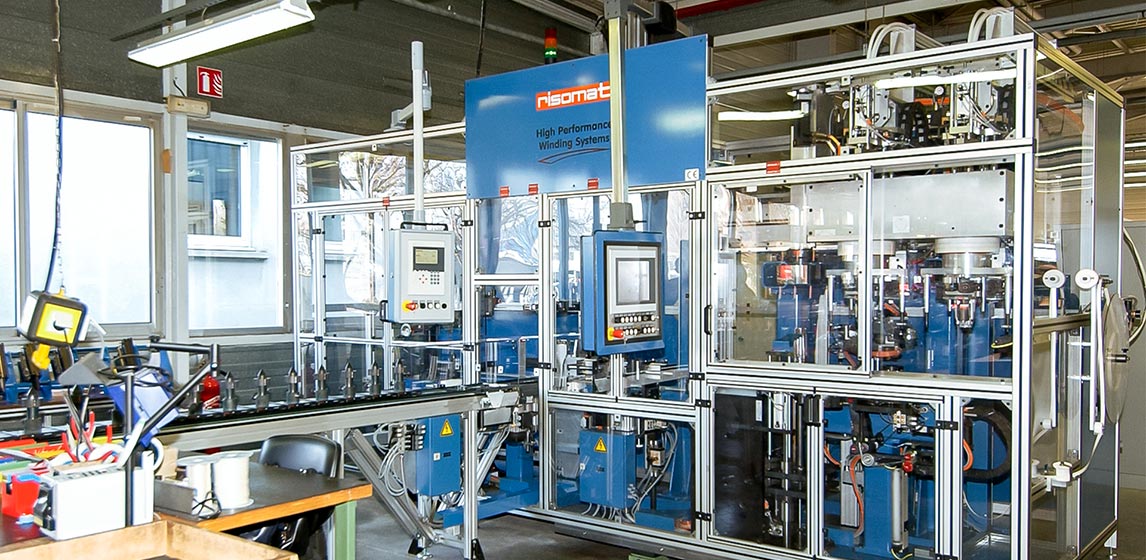
KNF’s Electric Motors
Drives are an essential part of every pump and need to be as flexible, fault-free and durable as possible. Electric motors have been used ever since the first diaphragm pumps and compressors were developed, and KNF has been manufacturing them in France for the entire Group since the 1970s. There are two practical reasons behind KNF’s decision to develop its own skills in producing motors. The first is that the purchase price for the small quantities the company requires is simply too high. And the second is that motors are sometimes impossible to acquire in such low numbers. So KNF France started to manufacture its own coils, stators and motors. A stator is the stationary part of a motor and includes its housing. At first, everything had to be produced by hand – it took 15 to 20 minutes to make a single stator.
In 1993, the first taping machine is used to tape the ends of the coils together. This is followed by the first winding machine for wire coils in 2000. Then, after three years of planning, the winding center is put into operation in 2003. This huge machine operates for 18 hours a day, producing stators of uniform quality at a rate of one part per minute. 400 different coils in six sizes and with 30 different wire diameters can be made at the push of a button. This marks a huge leap forward, as instead of laboriously changing tools every time a different model needs to be manufactured, staff can reconfigure the winding center in less than an hour. This means that parts no longer have to be manufactured in greater numbers than needed and stockpiled. Customizing drives becomes quite easy and the production process is more efficient and flexible, even when low production numbers are required.

The brushless motor has many advantages. Easy to control electronically, durable, compact, powerful and very energy efficient, it combines the benefits of an AC motor with those of a conventional DC motor. KNF’s motor team is currently focusing its efforts on a brushless digital motor.
Digital customization means that this new generation of configurable motors can be flexibly adapted to meet specific requirements – and can even be adjusted by users themselves! The DC motor is unique in its flexibility to define sets of operating parameters. Users have complete freedom to customize their diaphragm pumps by setting up highly complex operating profiles. Digital customization makes it easy to control digital signals through the precise management of target values. For example, in case of a malfunction, the pump normally would shut down. However, an alternative response can now be programmed, which prompts the pump to adapt its behavior to the source of the fault and compensate for it. The device then continues to operate. The pump’s flow rate can, for instance, be set as an unchangeable target value that is achieved regardless of the operative environment’s technical behavior.
KNF Blog Knowledge Flows
Follow the latest trends and stories on how diaphragm pump technology drives evolution in the market.
