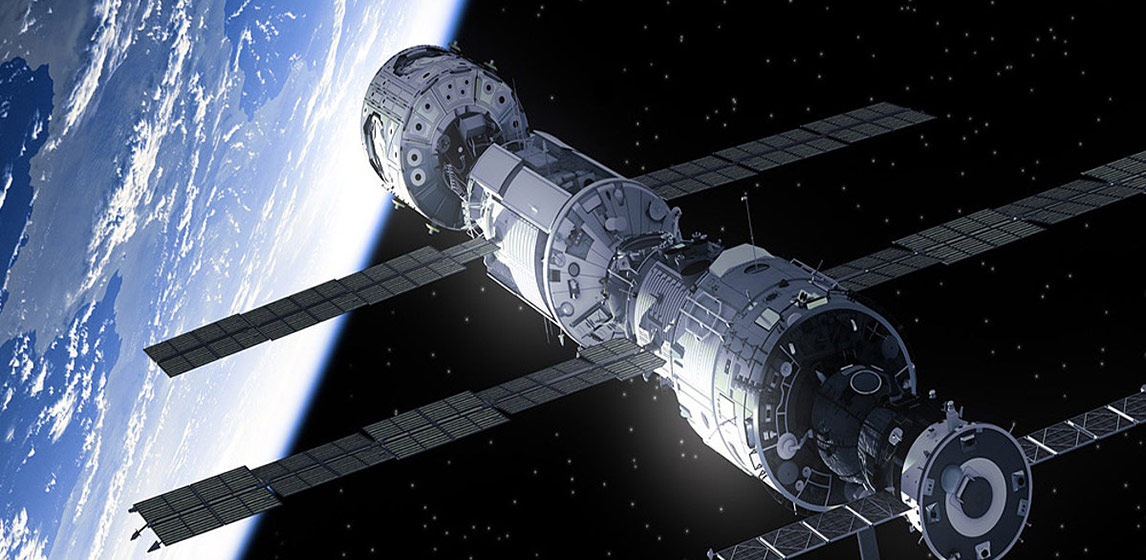
A Challenging Job in Space
The International Space Station (ISS) has been operated and enhanced by 16 countries for more than 20 years. It is the only existing space station, the largest human-engineered object in space and it orbits the earth once every 93 minutes at a speed of 28,000 kilometers per hour – that’s 16 times a day.
Since 2000, two to six astronauts have been on board the ISS at any given time. The well-being of the crew in these inhospitable conditions fully depends on the smooth and reliable functionality of the onboard systems. The shell and the glass windows of the station ensure its stability and protect against heat, cold and pressure loss while the supply facilities create a suitable living and working environment for the ISS crew.
Everything that the astronauts need in their speeding home is transported into space via shuttles – apart from the air they breathe. Oxygen is generated on board through water electrolysis and spent air is recycled. Reliable pumps are needed for this cycle, and the technical requirements of this unusual project are truly unique.
For four years, a team of KNF engineers worked with Airbus Defence and Space to develop a custom-fit liquid pump. The top priority was that the pump be reliable, to ensure that all processes run safely at all times. The pump design had to be highly precise because a broken part can’t just be exchanged so easily at a height of 400 kilometers. This is why the developers opted for the extremely small, powerful, long-lasting and efficient KNF liquid pump, which had to be made space-proof through a range of both minor and major modifications.
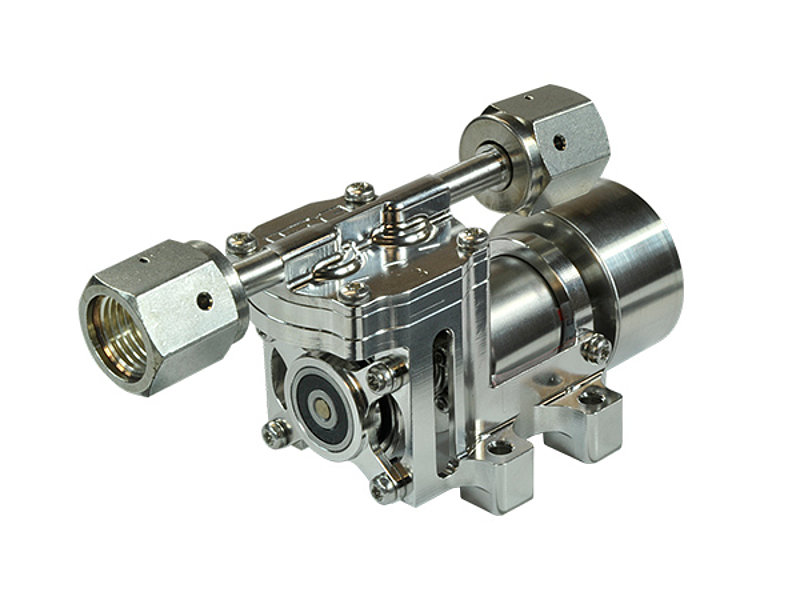
In 2018, two of these pumps were fitted into the life support rack (Advanced Closed Loop System – ACLS) and taken into operation by Alexander Gerst, the German ESA astronaut on board the ISS. The ACLS recovers carbon dioxide from the air and converts it into oxygen using electrolysis. The two diaphragm pumps built into the electrolyzer help in the generation of oxygen and hydrogen from water by transferring the supply water from a plastic bag into the system. In full operation, the ACLS uses up 3 kilograms of CO2 per day and generates 2.5 kilograms of oxygen as well as 1.5 kilograms of water. Oxygen recycling saves up to 450 kilograms of water load per year, which – at a price of 33,000 euros per kilogram – saves approximately 15 million euros.
KNF in space: a success story which benefits all of our customers. As challenges grow, so does our expertise. The development of the space pump design moved the goalposts in terms of what is possible – to boldly go where no man has gone before.
KNF Blog Knowledge Flows
Follow the latest trends and stories on how diaphragm pump technology drives evolution in the market.
