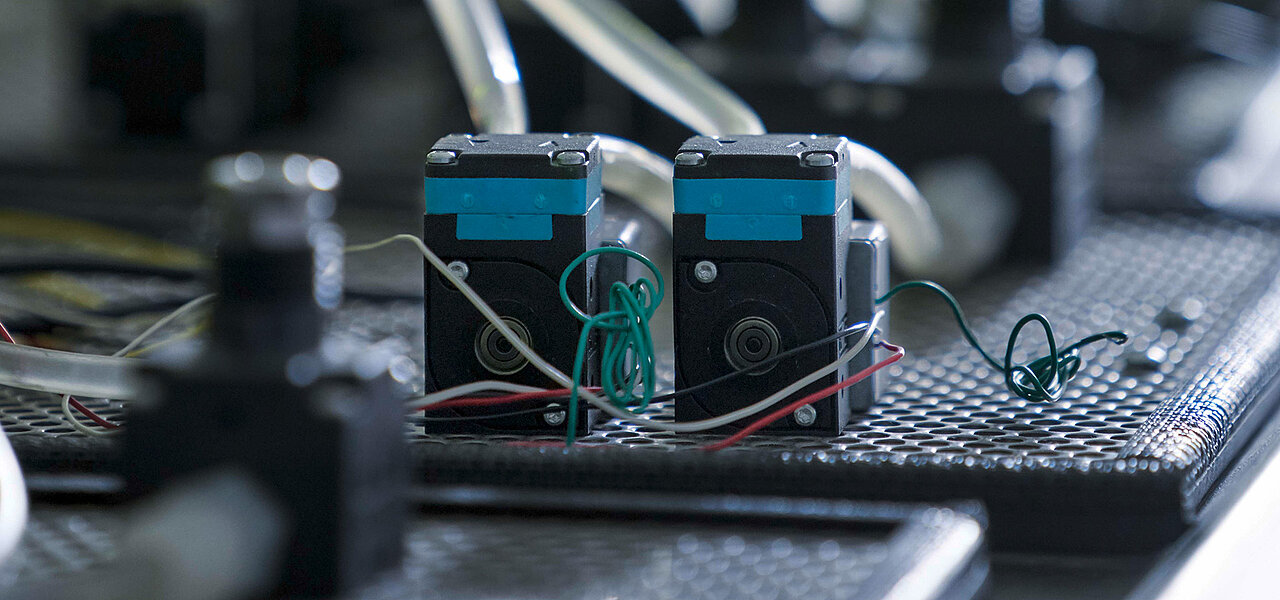
Making the Choice: Diaphragm vs. Peristaltic Pumps
Choosing a pump can be difficult as there are many factors to consider, and some challenges come along with a wide variety of pump technologies from which to choose. Two of the more frequently employed liquid pump technologies are diaphragm and peristaltic pumps. Both pump types are used in a variety of applications. In the following, we discuss the advantages and disadvantages of these distinct pump technologies.
How Diaphragm and Peristaltic Pumps Work
Diaphragm and peristaltic pumps are both commonly used in liquid transfer applications. While they are often used in similar applications, the principles behind these technologies are very different. Diaphragm pumps operate by driving a flexible diaphragm up and down. This motion displaces media, in this case liquid, within a working chamber to generate flow. Peristaltic pumps, sometimes called tubing pumps or roller pumps, use tubes fitted inside a cartridge. Rollers compress the tubing as they rotate, forcing liquid through.
Which Pump Technology is Best For Liquid?
Both pump types are common in a variety of applications including medical, laboratory, chemical/petrochemical, inkjet printing and agriculture. When choosing a pump, a variety of factors need to be considered. Some of the most important are:
- Lifetime costs
- Use of tubing
- Cleaning and sterilizing
- Flow and pulsation
- Use with particulates and shear sensitive media
- Use with dangerous liquids
But how do the two pump technologies compare in terms of these factors? Which has the advantage in each of them?
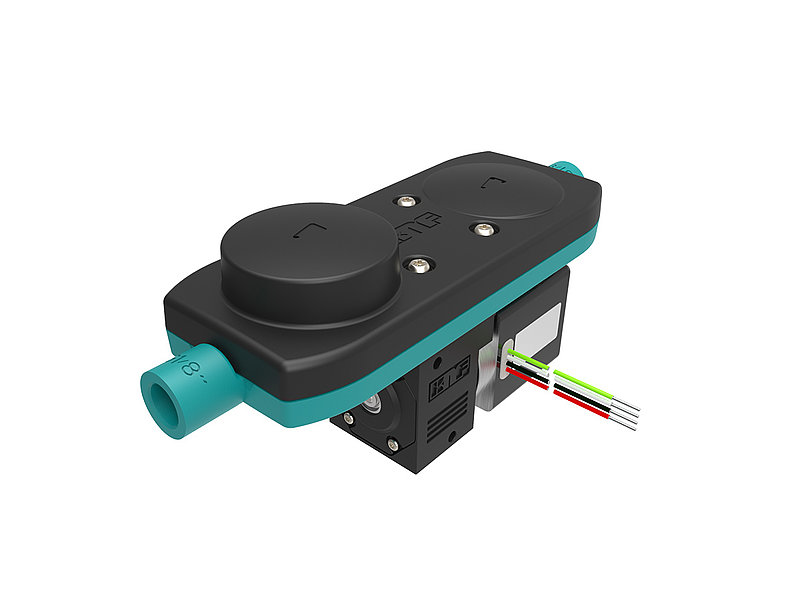
Lifetime Costs
Regardless of the pump technology used, costs other than the purchasing price are going to be a factor. Maintenance and energy consumption are two of the most critical in determining lifetime costs. Diaphragm pumps tend to require less frequent maintenance. Removing and replacing the diaphragm or valves is a relatively simple and cost-effective process. Most general maintenance on diaphragm pumps can be performed in-house without the need for, and added cost of, maintenance visits.
Although both technologies use tubing to transport media to and from the pump, only peristaltic pumps place tubing under physical stress by the inherent pinching motion by the rollers. These issues are unavoidable by design with peristaltic pumps. Diaphragm pumps do not rely on rollers and pinched tubing to move fluid, thus avoiding tubing degradation. Because they lack such an extreme reliance on tubing, diaphragm pumps have the advantage.
Peristaltic pumps typically have a lower upfront cost. However, the cost of operating them over time rises quickly. Their tubes need to be replaced frequently, which can drive up costs. While replacing tubes is a relatively simple process, it is also required frequently, which drives up lifetime costs. Maintenance of rotors and other internal parts also tends to be more complex and expensive. In general, the lifetime cost of a diaphragm pump is going to be lower than that of a peristaltic pump.
Reliability
Peristaltic pumps are completely reliant on tubing to transport media. Over time, the constant movement of a peristaltic pump’s rotor and pinching will degrade these tubes, gradually reducing their elasticity and wearing them down. This inevitably leads to reduced flow rates, as well as other complications. Therefore, tubes need to be replaced at regular intervals, driving up costs. At best, worn tubes can reduce efficiency. At worst, they can crack or rupture leading to leaking media, down time, and damage to the pump. This can be catastrophic if the liquid being pumped is dangerous or caustic. Diaphragm pumps have parts that can degrade as well, but not nearly as quickly or dramatically.
Peristaltic tubing needs to be replaced frequently, several times each year in some cases. It can be expensive, and depending on the application, tubing made from specialty materials may be required, potentially driving up costs even further.
Cleaning and Sterilizing
Diaphragm pumps can be cleaned in a variety of ways, depending on the application and liquid being pumped. For many applications, pumping cleaning liquids through is sufficient. But some applications require the head to be disassembled completely. Once disassembled, the pumps can be difficult to clean out thoroughly.
With peristaltic pumps, the tubes can be removed, discarded, and replaced, saving time and streamlining the cleaning process. As long as the tubes are replaced regularly and have not leaked or ruptured, the rest of the pump does not need to be cleaned to maintain media integrity. In addition to a more streamlined cleaning process, peristaltic pumps are also much easier to sterilize. This is important for some lab and other applications where frequent sterilization is required. Because the media only comes in contact with the tubes, only the tubes need to be sterilized.
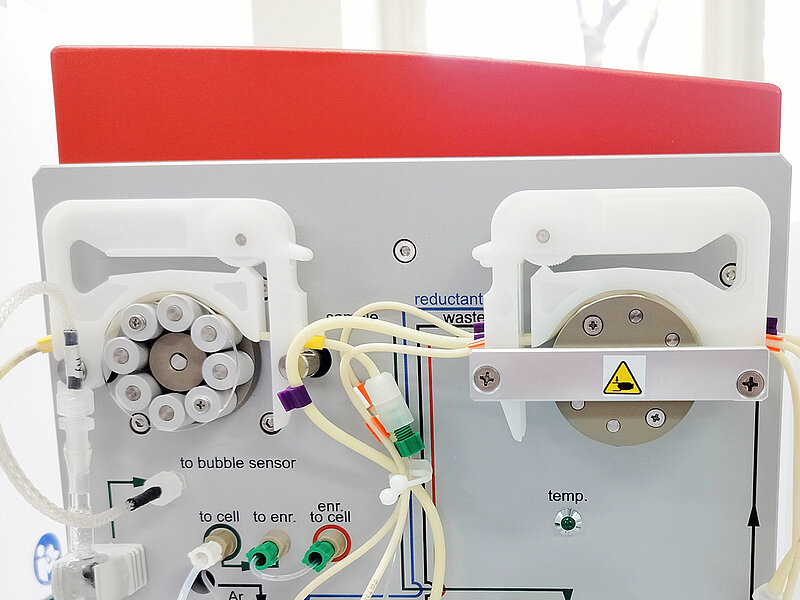
Flow and Pulsation
Both peristaltic and diaphragm pumps can reach impressive flow rates. However, diaphragm pumps are much better at providing smoother flow and low pulsation. The pinching of tubes required by peristaltic makes it difficult to attain the steady flow required for some applications. This can be mitigated somewhat by buying a more expensive peristaltic pump with more rollers. Additional rollers, however, can accelerate performance degradation, pinching and wearing tubes more quickly and impacting flow. Using different tubing material may help limit pulsation slightly, but again will likely drive up costs and impact flow rate.
The stroke of a diaphragm pump is much more consistent over time making flow more even. For even smoother, low-pulse flow, some diaphragm pump manufacturers offer multi-diaphragm configurations arranged out of phase so individual pulse waves are mostly eliminated. Newer diaphragm pump offerings also include integrated dampers and resonance chambers, further reducing pulsation. These options make diaphragm pumps better suited for applications where smooth flow is required.
Peristaltic pumps do have other advantages in terms of flow, particularly for applications requiring bi-directional flow. They are capable of quickly changing flow direction without major alterations, making them ideal for applications where that is required. Bi-directional flow can be achieved by simply changing the direction of the rotation. Peristaltic pumps are also preferable in applications that require a single pump to provide multiple different flow rates or multiple channels of flow. However, these features may come at a cost by requiring additional cartridges or even larger pumps with more cartridge capacity.
Which pump technology better meets flow needs depends on the specific application. Peristaltic pumps are a better option requiring multi-directional flow. Diaphragm pumps are preferable for applications requiring consistent, smooth flow and low pulsation.
Use With Particulates and Shear Sensitive Media
Many applications require the transfer of liquids with particulates. Diaphragm pumps perform well with particulates up to a certain size. They are common in inkjet printing applications and can handle most inks without issue. However, they can struggle with longer particulates, fibers and pasty media. Diaphragm pumps rely on check valves, which can become clogged by these particulates. Peristaltic pumps lack these valves, and thus do not have this issue. The pinching action of the roller also makes it easier to push particulates along.
Diaphragm pumps are good at handling most types of shear sensitive media. However, peristaltic pumps are a better option for extremely shear sensitive media, like blood or cells. Because their pumping action is relatively easy on the liquid, peristaltic pumps have a lower chance of damaging or agitating suspensions being pumped.
Use with Dangerous or Extreme Temperature Liquids
Caustic and corrosive liquids can break down peristaltic pump hoses quickly, leading to increased risk of leakage. This risk can be reduced by using chemically resistant tubing materials, but this will lead to increased cost and possibly impact performance. The already frequent maintenance required becomes even more critical and frequent for safety reasons, as having these liquids leak can be catastrophic.
Diaphragm pumps are routinely offered with chemically resistant flow path materials. As with peristaltic pumps, these materials can drive up cost. But diaphragm pumps require infrequent preventive maintenance, unlike the frequency required for safe handling of dangerous liquids with peristaltic pumps. Diaphragm pumps are also better for handling liquids of extreme temperature. Most tubing available for peristaltic pumps is not suitable for transporting excessively hot or cold media. Extremely hot liquid can make tubing too soft, impacting flow rate and increasing the potential of tubes bursting. Similarly, extremely cold liquids can make tubing too rigid for good flow performance. While diaphragm pumps may require special materials for these processes, they are far more suited to transferring hot and cold media.
Choosing a Pump
Peristaltic pumps are a little more limited in scope, but they are the ideal choice for a variety of applications. They are preferable for pumping extremely viscous or muddy liquids, as well as extremely shear sensitive media. Diaphragm pumps are easy to clean, which is sufficient for most applications. However, peristaltic pumps can be cleaned and sterilized quickly, as their tubes can be removed and discarded after use. This makes them the better option for applications where very frequent cleaning is required.
While diaphragm pumps tend to be a better fit for more applications, that is not always the case. The choice between pump technologies depends on the individual requirements of an application. Diaphragm pumps are less expensive over their lifetime to maintain, have a lower overall cost of operation, and last longer. They are easy to maintain and repair and provide a variety of options for a more consistent and smoother flow as well as low pulsation. They are also the better choice for applications dealing with harsh, caustic, and extreme temperature liquids.
Get in touch with KNF to learn more about out custom diaphragm pump solutions
75 Years: KNF Celebrates Company Anniversary
A treasure chest filled with memories, facts and stories. Learn more about KNF’s company history.
