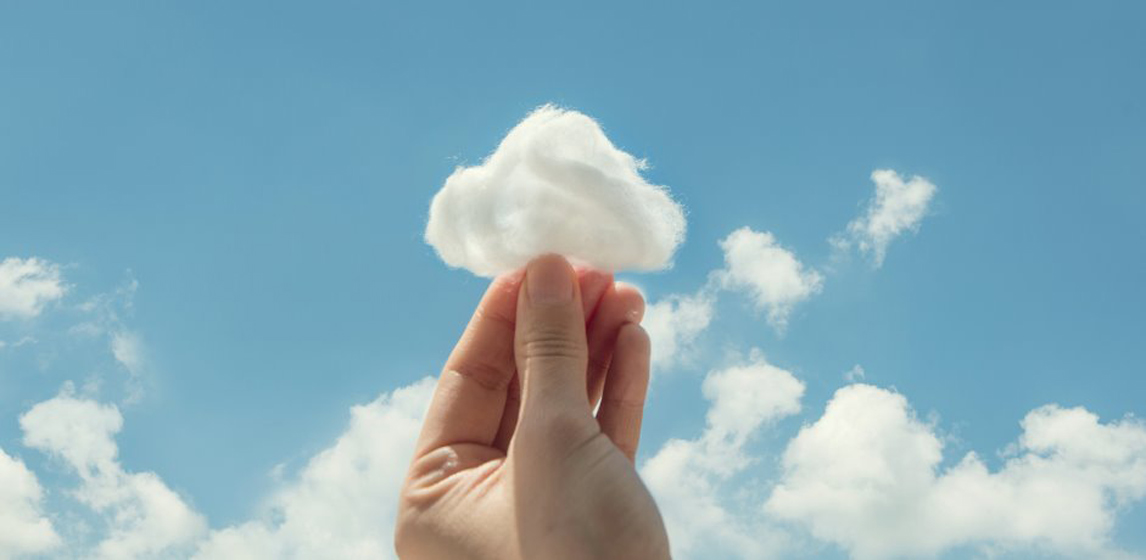
Improving Air Quality – With Pumps in Continuous Emission Monitoring
We can’t live without air. We breathe in and out constantly. The pollutants emitted by industrial plants include sulfur dioxide, carbon dioxide, particulate matter and volatile organic compounds (VOC). Why does industry contribute so much to air pollution? The main reason is its enormously high energy demand. Many companies even operate their own power plants to meet this demand. There are also specific processes within certain industries, such as coal mining and metallurgy, which generate direct emissions.
Emissions are monitored in power plants, waste incinerators and motor testing facilities, on offshore ships and, of course, in industrial production plants, as well as in gas analysis in chemistry. In addition to the goal of protecting the environment and ensuring safety, there is also a focus on optimizing combustion processes. This means greater efficiency and lower energy consumption, as well as protecting the components used in production and giving them a longer service life. In short, it is a win-win situation in which the environment benefits just as much as the companies that save money through sophisticated flue gas monitoring with continuous emission measurement.
Volatile organic compounds (VOCs) are key factors in the formation of the photochemical smog which leads to the Chinese pollution phenomenon “haze”
The phenomenon of smog has existed for quite some time in China’s major cities and the government has been fighting it with numerous plans of action. In the last two years, factories have been closed and driving bans imposed; in 2017, a transition from coal-fired heating to gas and electricity was ordered. There are further government regulations regarding VOCs in China.
VOCs are key factors in the formation of photochemical smog, which is responsible for the infamous “haze” – known in China as “wu mai.” This is a serious pollution phenomenon. Public policy is now trying to improve the environment by controlling VOC emissions, and the first step is to monitor these emissions.
VOC emission monitoring devices can use one of several different methods. In this blog post we focus on online high–temperature VOC monitoring, where the flue gas is not cooled down but is fed to the analyzer while still hot. This prevents the condensation of individual components within the flue gas.
Fortunately, there has been a worldwide rethink of these processes, and the resulting measures are helping to reduce emissions without sacrificing production efficiency. KNF is pleased that our pumps are helping to achieve the goal of a sustainable improvement in air quality. For example, they are used in various systems in conjunction with sensors and analyzers that measure industrial gas emissions.
The Chinese manufacturer Focused Photonics Inc. (FPI) in Hangzhou has built a nonmethane hydrocarbon (NMHC) analyzer, which uses our pumps to transfer flue gas from a chimney to the analyzer. The company offers two product lines, suitable for temperatures up to 60°C and up to 240°C respectively.
To prevent the gas from cooling, the pump head is placed in a box which is heated up to 140–180°C. The company uses our heat–resistant pumps for this purpose. Depending on the customer’s needs, we can deliver various project options with different mechanical designs, such as an elevated head which can also be rotated by 180° and, insulating material to reduce heat loss, holes in the pump head for heaters and sensors, rubber feet to reduce vibration, or special mounting plates.
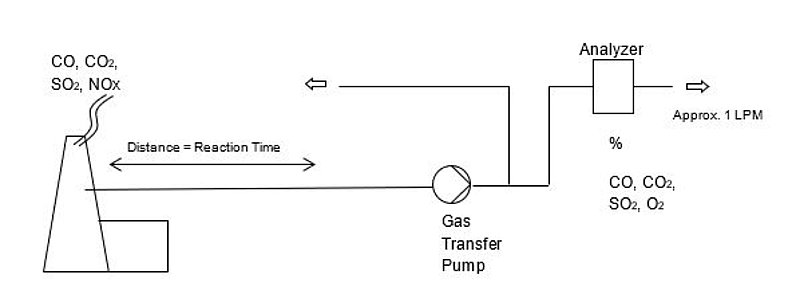
A sensor at the inlet of the analyzer helps to measure the pressure, while a flow meter at the outlet determines the flow. Usually the flow rate (1 LPM) is controlled manually via a needle valve. This data is important to ensure that the monitoring takes place under constant conditions.
Our gas pumps offer a range from 6 LPM to 32 LPM, depending on the quantities to be analyzed and the scale of the application
For transferring the sample from the chimney or exhaust system to the analyzer, we offer heat–resistant pumps ranging from 6 LPM to 32 LPM, depending on the analysis requirements and the scale of the application. Our pumps designed for this application allow gas temperatures of up to 240°C. They are also leak tight and condensate–proof.
The diaphragm pump requires minimal maintenance and offers greater flexibility thanks to its connection options. We recommend the use of a BLDC motor as this can be intelligently integrated into the control processes via speed control, which allows the pump to cover any operating condition which is to be analyzed.
With a BLDC motor, the following control options are possible.
- Standard flow rate: If a 24 V supply voltage is applied to the BLDC motor, the pump delivers its nominal flow rate.
- Preadjusted flow rate: We can adjust the nominal flow rate of the pump beforehand. The pump will then deliver a specific flow if the supply voltage is applied to the BLDC motor.
- Adjustable flow: It is possible to change the flow of the pump by adjusting the motor speed using one of the following options:
- Analog signal: In addition to the voltage supply, a control voltage is applied to the motor. This can be, for example, 0…5 V, where the motor rotates at full speed at 5 V and reaches its minimum speed at 0
- Current control: A current control signal is applied in addition to the voltage supply. The current value regulates the motor speed. The current signal can, for example, be 0–20
- PWM signal: In addition to the supply voltage, a pulse width modulation (PWM) signal is applied to the pump. This is generated by a PWM generator — a fast–switching electronic controller. This on-off signal controls the speed of the motor via the length of the pulses.
If an AC motor is preferred, we can also design this for all common voltages.
The pumps used for continuous emission measurement contribute to the accuracy and reliability of the analysis methods and help manage the optimization of combustion processes. Further optimization of the pump’s function within the application can be achieved through the superior speed and signal controls available with BLDC motor technology.
75 Years: KNF Celebrates Company Anniversary
A treasure chest filled with memories, facts and stories. Learn more about KNF’s company history.
