Las bombas KNF renuevan el aire de la Estación Espacial Internacional (ISS)
Bombas KNF para impresión 3D con arena
Smart Slab desarrollada por investigadores de la ETH de Zúrich (Suiza) en un innovador proyecto arquitectónico
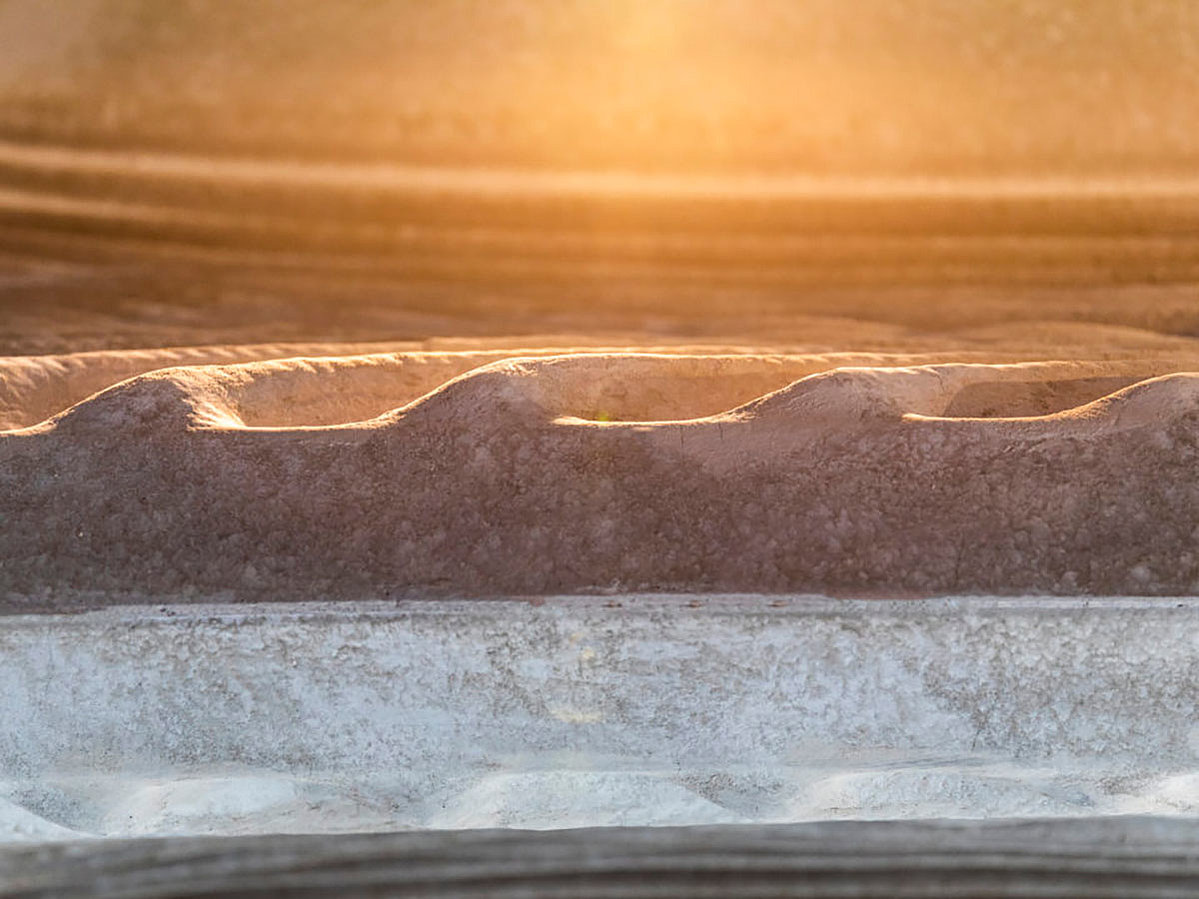
Investigadores de la universidad ETH de Zúrich están fabricando una cubierta de hormigón inteligente y ligera como parte del proyecto arquitectónico Smart Slab. Esta universidad suiza utiliza un innovador método de fabricación para crear el molde para las losas con una impresora 3D de arena de la empresa alemana Voxeljet AG en la que hay montadas bombas KNF.
Las ventajas de la fabricación digital
La cubierta inteligente Smart Slab combina la resistencia estructural del hormigón con la flexibilidad de diseño de la impresión 3D. El método de fabricación digital es mucho más económico y ecológico que construir cubiertas macizas. En su punto más delgado, Smart Slab solo mide 20 milímetros, sin que ello le haga perder estabilidad. Esto significa que se reduce el peso a menos de la mitad que una cubierta convencional, por lo que el consumo de material es menor, lo que no solo reduce los costes de fabricación, sino también la huella de carbono.
Las raíces del proyecto
La cubierta Smart Slab ha sido desarrollada en la ETH de Zúrich bajo la dirección de Benjamin Dillenburger, profesor de tecnologías de construcción digitales. Es uno de los elementos fundamentales de la unidad residencial DFAB House que se levantó en el edificio NEST, un centro de investigación e innovación de los institutos Empa y Eawag, en Dübendorf (Suiza) en el verano de 2018. Formada por once segmentos de hormigón que conectan el sótano con la estructura de madera de dos plantas que se levanta sobre él, la cubierta mide 80 m2 y pesa 15 toneladas métricas.
El mínimo de hormigón posible
Los investigadores del proyecto Smart Slab utilizaron impresoras 3D no para fabricar los elementos constructivos en sí, sino el encofrado, es decir, su molde negativo. Para ello trabajaron con una impresora 3D de arena de gran formato de Voxeljet. La impresora cuenta con dos bombas de diafragma para líquidos de KNF; una de ellas se encarga de suministrar aglutinante frío (NF 60 KT DC) y la otra de retirar la materia prima sobrante (NF 60 KT DC). La elaboración del encofrado es el paso más laborioso de la construcción en hormigón, sobre todo si se trata de componentes no estandarizados.
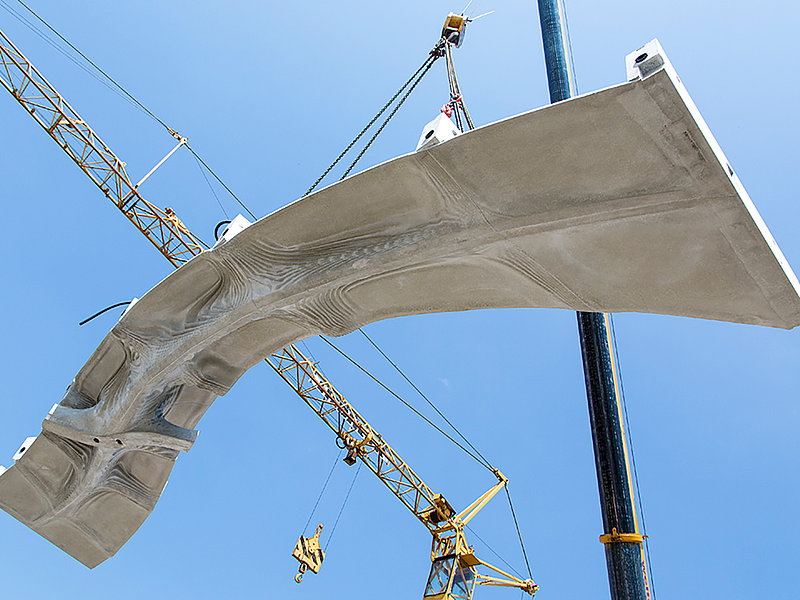
Producción pulsando un botón
Una vez realizada la planificación por ordenador, los socios industriales de los investigadores de Smart Slab se pusieron en acción. Uno se encargó de elaborar el encofrado en 3D de alta resolución de arena a presión, mientras que otro utilizó cortadoras láser CNC para crear el encofrado de madera. Esto es lo que da a la parte superior de Smart Slab su forma, pero también se incluyen cavidades para reducir el peso y la cantidad de material utilizado y crear espacio para los cables eléctricos. A continuación, el tercer socio juntó los dos tipos de encofrado para proceder al hormigonado. Esta empresa primero inyectó el hormigón reforzado con fibra en el encofrado de arena a presión para obtener la superficie finamente estriada del casco de hormigón inferior, y después moldeó el resto de la cubierta Smart Slab con el encofrado de madera.
Sólidos resultados gracias a la planificación previa
Tras dos semanas de curado, los once segmentos de hormigón estaban listos para ser transportados a la DFAB House. Gracias a un meticuloso proceso de planificación y prefabricación, así como a la elección de unos socios expertos y tecnologías fiables, se pudo garantizar que el proyecto se terminara con éxito y sin retrasos. «Era abrumador ver lo perfectamente que encajaban los elementos entre sí y con los demás componentes de la DFAB House», dice Dillenburger. «Esto no habría sido posible sin el extraordinario nivel de colaboración interdisciplinar que conseguimos con nuestros socios».