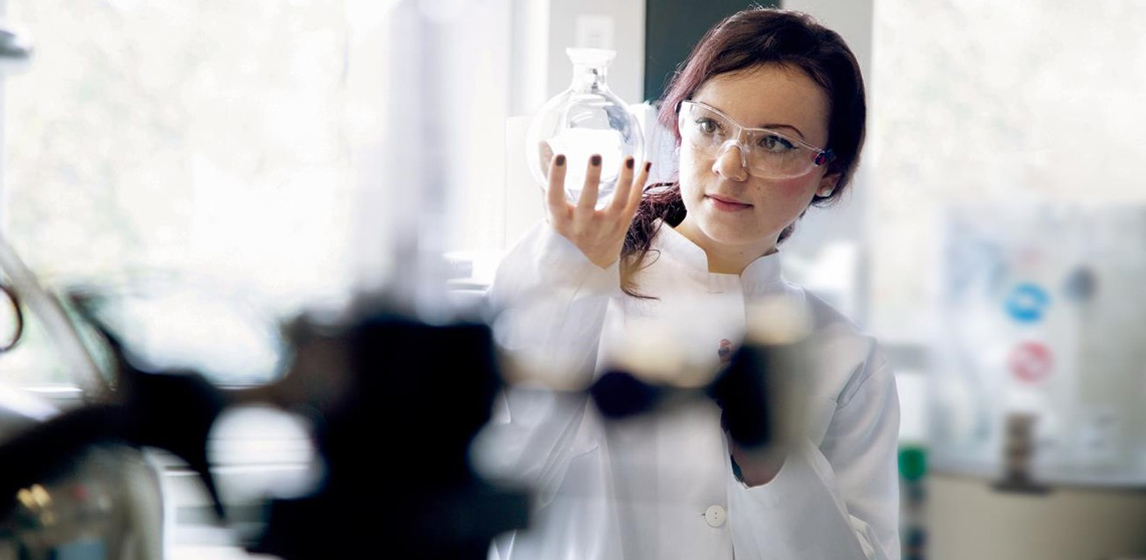
Die beste Vakuumpumpe für den Rotationsverdampfer
Destillationsversuche gehören im Chemielabor zu häufigen Anwendungen. Doch welche ist die geeignete Vakuumpumpe für den Rotationsverdampfer? Und wenn es schon eine Pumpe gibt, ist diese die Richtige? In vier Schritten lässt sich die passende Pumpe bestimmen.
Which solvents should be used?
This is important because of the different boiling points of different solvents. Solvents with a low boiling point, such as acetone, methylene chloride and pentane, don’t need as low an ultimate vacuum for evaporation as others, such as acetonitrile, benzene and chloroform. A relatively low ultimate vacuum is required to remove solvents with high boiling points, such as water, dimethyl sulfoxide (DMSO), dimethylformamide (DMF) and toluene.
So, it’s important to ensure that the pump reaches a low enough ultimate vacuum to efficiently remove the target solvent. This aspect goes hand in hand with the need for chemical compatibility. Suitable materials are chosen depending on the type of solvent vapors passing through the pump — this is essential for smooth operation over long periods of time.
How big is the evaporating flask?
Bigger isn’t always better. If the pump is too big and its flow rate is too high for the application in question, not only will it be hard to regulate, it will also be inefficient and expensive, both to purchase and to operate. On the other hand, if the pump is too small or the flow rate is insufficient, evaporation will be slowed down, leading to longer processing times. For instance, a pump intended for a 250 mL flask should not be used for a 20-liter evaporation flask and vice versa.
How high is the temperature of the heating bath?
The key is to establish whether the pump can provide the necessary vacuum and handle the steam temperatures. The smaller the difference between the bath temperature and the solvent’s boiling point, the higher the rate of Evaporation. If the mixture isn’t sensitive to high temperatures, raising the bath temperature will speed up the process and reduce the need for a deep vacuum pump. This can help determine which pump is best suited for the task at hand.
How should the vacuum be controlled?
Manual, two-step or adaptive control? Vacuum regulation makes it possible to optimize the vacuum level in the system. An optimum vacuum level reduces evaporation times and ensures a better product yield. Controlling the vacuum also reduces the build-up of oscillation and improves solvent recovery and reproducibility.
Manual vacuum control uses a stopcock or a manual valve and the vacuum level is adjusted by sight. With this method, the whole process must be closely monitored as the level of vacuum required can change during evaporation.
Two-step or on/off vacuum control makes it possible to switch the vacuum in the system back and forth between a high and a low setpoint by turning the pump on and off. This method means that the process can be left to run unsupervised once the minimum and maximum limits have been set.
Adaptive vacuum regulation delivers the best results in terms of separation, speed and solvent recovery, and also means that the process can be left to run unsupervised after configuration of the settings. This control method changes the rotational speed of the pump automatically and adjusts it to meet the process requirements exactly. It is also the most precise method, enabling the system to work with a particular vacuum level and simultaneously react to changing conditions with no need for the operator to monitor and adjust the settings.
Although it is relatively easy to find the right pump for rotary evaporators, we recommend getting the advice of experts. They can ensure that special applications and individual processes are also considered.
Based on How to Select a Pump for Rotary Evaporation, The Pump Post, 2014
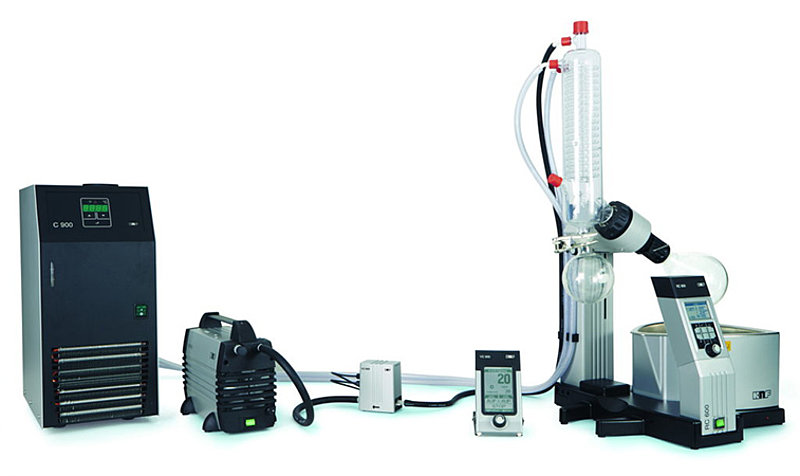
75 Years: KNF Celebrates Company Anniversary
A treasure chest filled with memories, facts and stories. Learn more about KNF’s company history.
