KNF’s swing piston compressor and Bürkert’s valve module test the waterproofness of watches
Leak Detectors – Report Leaks Before Damage to the Environment Occurs
With their longevity and low maintenance requirements, KNF compressors are the ideal component for pressure leak detectors.
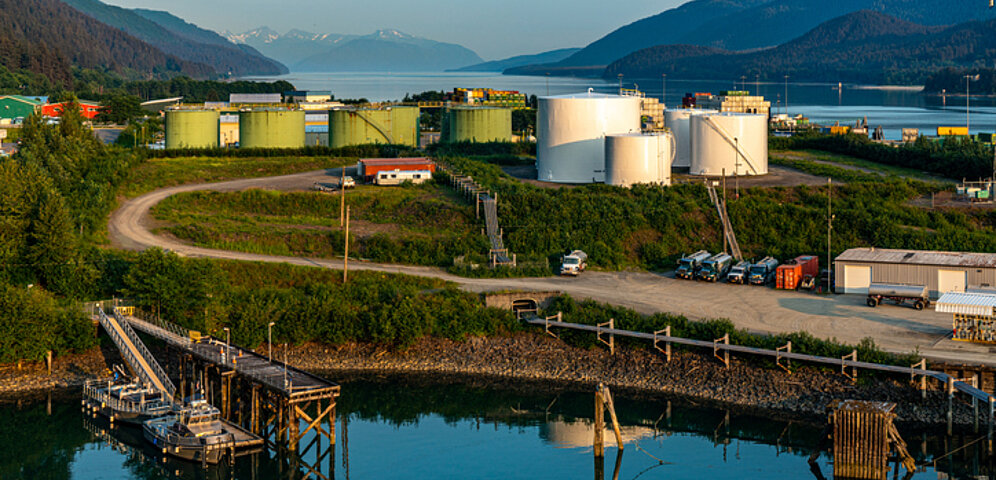
SGB leak detectors offer maximum protection for the environment and shield water against contamination. When it comes to pressure testing with air, KNF compressors are the company’s trusted option.
SGB Leak Detectors with KNF Compressors
SGB GmbH in Siegen, Germany develops and produces leak detection technology for environmentally sensitive applications, such as at commercial and private fuel depots, refineries, chemical plants, and at gas stations. These systems have jacketed pipelines. SGB pressure and vacuum leak detectors monitor the annular space for leaks.
For pressure testing with air, SGB utilizes KNF NPK 06 and NPK 09 compressors in their DLR-P series leak detectors. The KNF pumps use dried air to generate a maximum test pressure of 7.5 bar in the annular space between the pipes. With SGB pressure monitoring, gas station operators can be secure in knowing the integrity of the jacketed pipelines to their underground fuel tanks at all times.
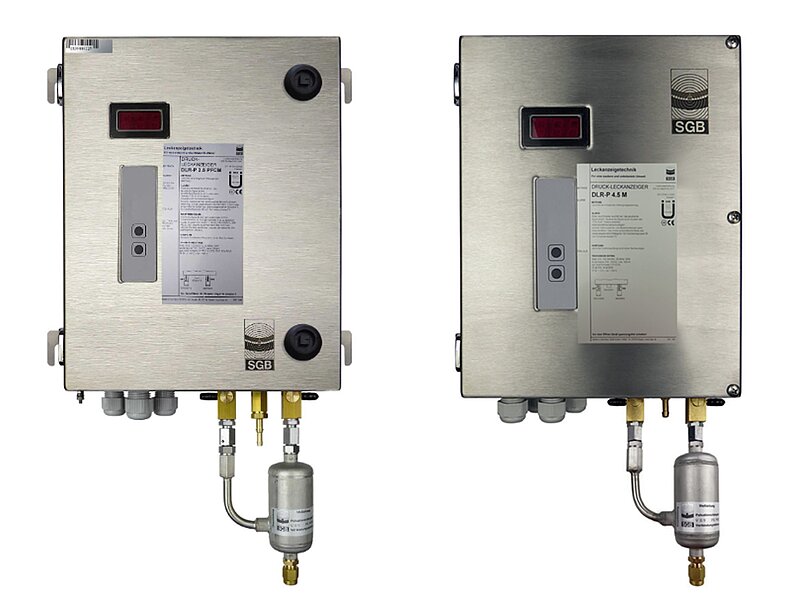
Test Pressure in Underground Fuel Tank Pipelines – Three Key Functions:
- An accelerating, repeated drop in test pressure is an early and reliable indication of the onset of leaks.
- The integrated KNF pumps automatically compensate for those minor pressure irregularities in the intermediate space that inevitably occur due to fluctuations in temperature, for example.
- If a leak occurs, the positive pressure prevents the fuel from escaping into the environment for a limited period of time.
Pressure Testing with Air Protects the Environment
Monitoring the annular space between jacketed pipelines at gas stations is required by law. SGB leak detectors meet the requirements for Class I leak detection systems as stipulated by the EN 13160 standard, meaning they offer the highest level of protection for the environment and, in particular, for bodies of water. SGB is a pioneer in leak detection technology and has played a decisive role in shaping this standard.
Continuous leak testing using positive pressure requires KNF compressors to reach the operating point – and, in turn, the specified test pressure – very precisely, every time. Exceeding the values specified in the standard, i.e. too high a pressure output, is also not permitted.
How Does the Pressure Leak Detector Work?
The NPK compressor integrated within the leak detector builds up the required test pressure in the jacketed pipe’s annular space by drawing in air and then passing it through a dry filter. This reduces the moisture content in the air, and thus that of the leak detection medium, to 10%.
A pressure sensor measures and regulates the positive pressure. The pump switches to “OFF” mode when the NPK compressor reaches the nominal pressure. The test pressure slowly drops again due to unavoidable leaks in the leak detection system. When the “Pump ON” value is reached, the KNF compressor switches itself on and builds up the test pressure again. If the compressor begins switching on and off more and more frequently, this is an initial indication of an increasing leak within the system.
If a leak occurs in the inner or outer wall, air will escape from the gap. The pressure will then drop until the KNF compressor is switched on to restore the test pressure. If the volume flow rate escaping through the leak is greater than the compressor’s flow rate, the pressure in the system drops causing the pump to operate continuously. If the pressure drops low enough to trigger the “Alarm ON” setting, the unit emits visual and audible warnings.
As both the test pressure and alarm pressure are higher than the pressure of the fuel or the groundwater against the pipe walls, if one of the pipe walls has a leak, only air can escape and not the water-hazardous liquids. An alarm is triggered before any damage to the environment can occur.
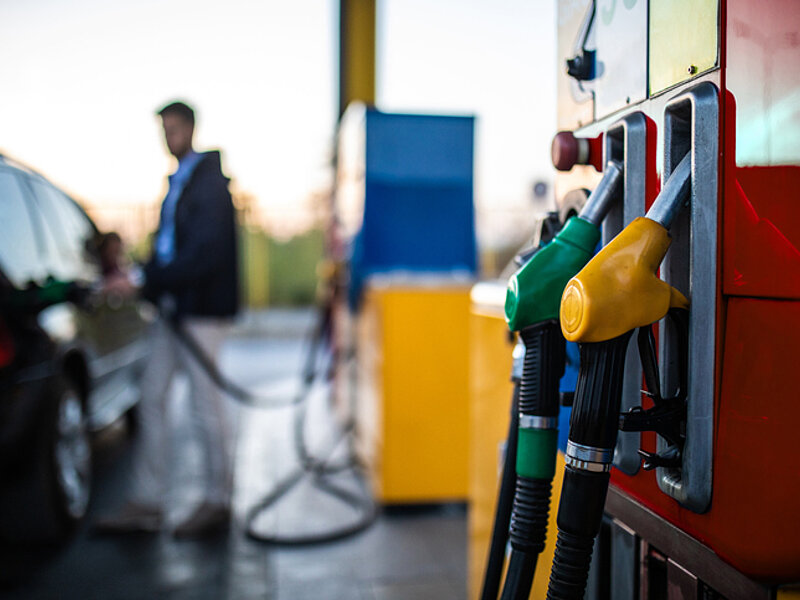
The Benefits of KNF Compressors for SGB Leak Detectors:
- In order to save space and meet customer requirements, SGB strives to keep the construction dimensions of its pressure leak detectors to a minimum. KNF supports these efforts and optimizes the size-to-output ratio of its compressors continuously.
- NPK compressors can be adapted flexibly at any time. The pumps’ features that are crucial for pressure testing with air have been constantly adapted to new technical requirements that have evolved over the many years of collaboration SGB and KNF have enjoyed. Some examples are the position of the gas connections, the materials the pump head and valves for changing operating temperatures are made from, the start-up behavior against pressure, the motor cables and the size of the eccentric. At KNF, this flexibility is a matter of course, even for small production numbers, which is KNF’s special advantage.
- SGB is justified in being proud of a turnover-related repair rate of less than 0.2 %. With their high durability and low maintenance requirements, KNF compressors are also a perfect fit here.
Pressure leak detectors are safety equipment – they have the extremely important task of protecting our environment from water-hazardous substances. Every effort to harness the latest findings and technological advances for even greater safety with engineering expertise has paid off. KNF has been proud to follow SGB’s philosophy for many years and hugely values the trust and collaboration they have built up.
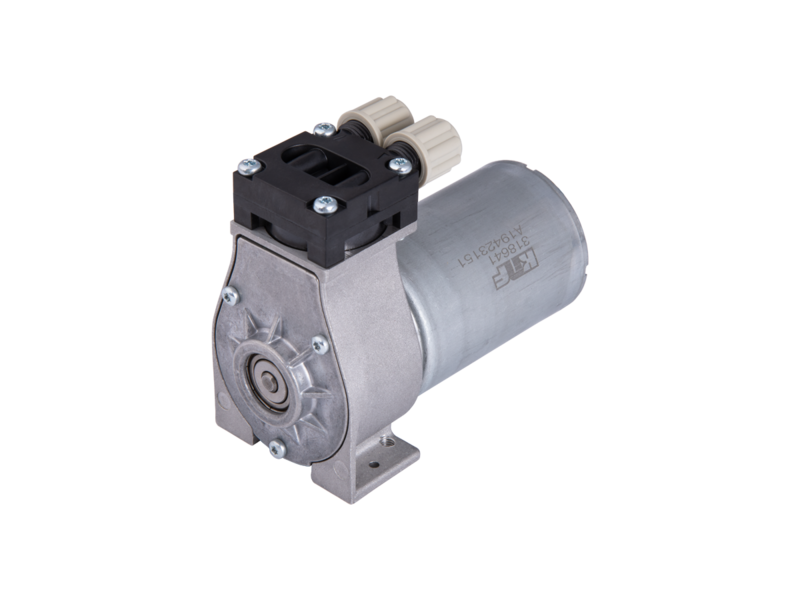
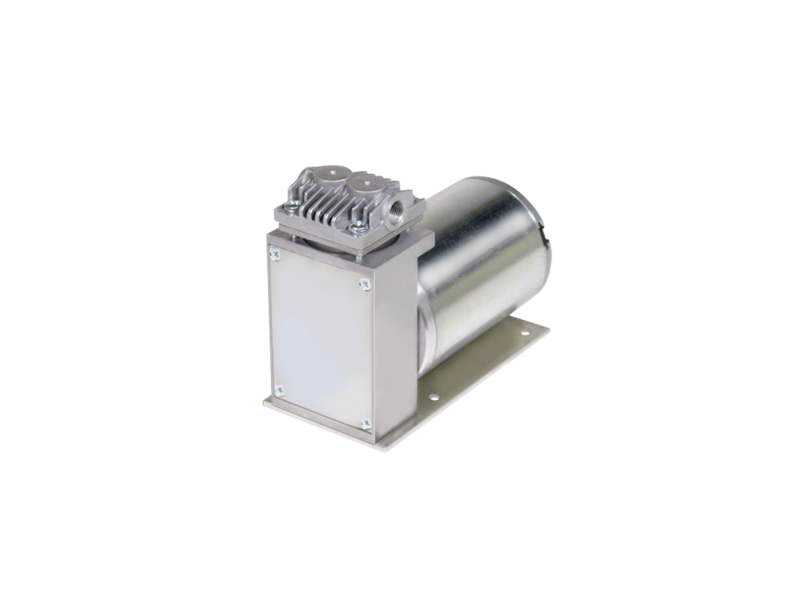
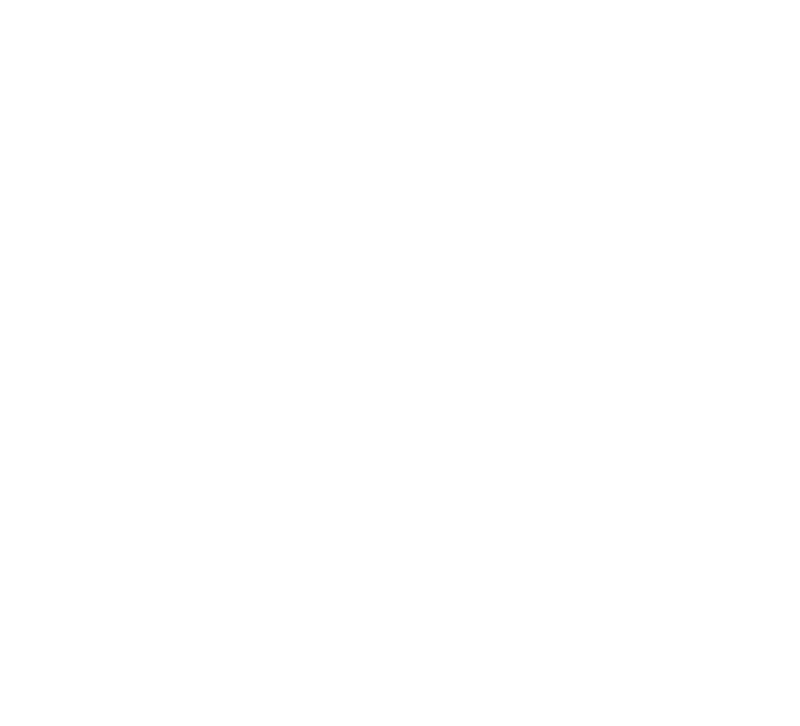
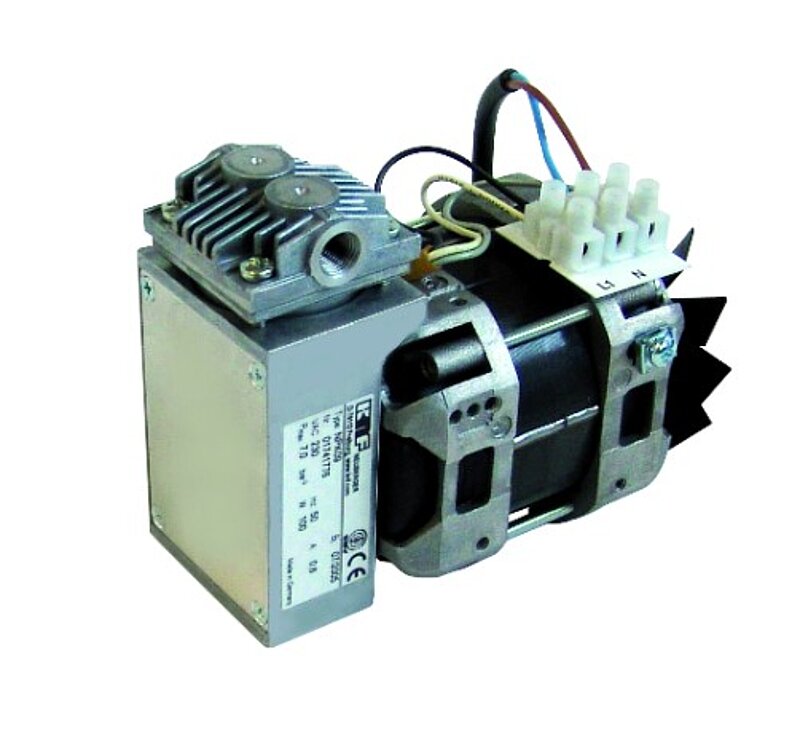