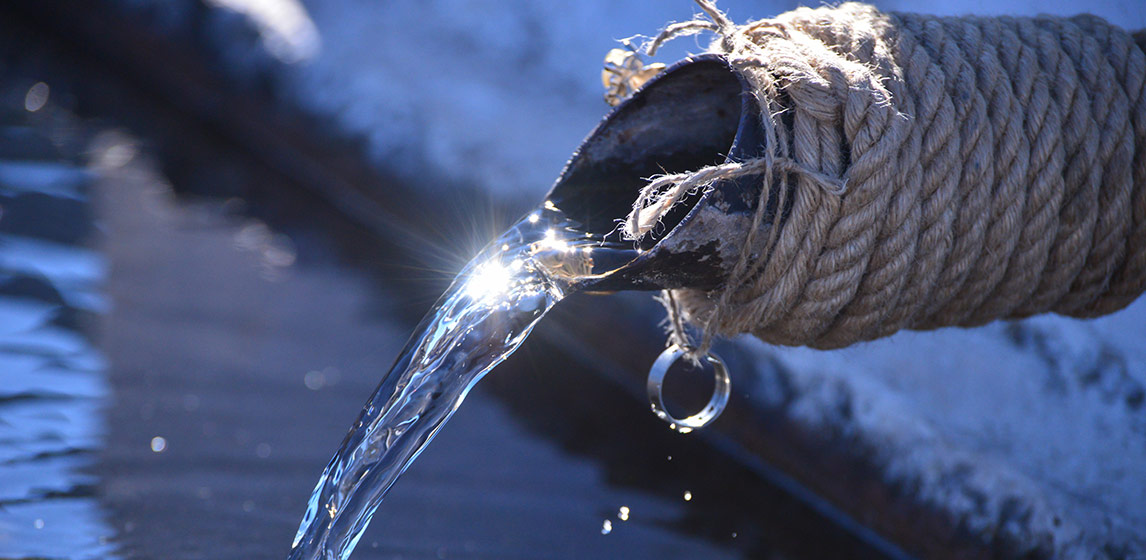
Liquid Transfer With Low Pressure Pulsation
Diaphragm pumps clearly offer many advantages to users, such as durability, dry-running safety, and suitability to transport abrasive liquids. However, diaphragm liquid pumps with only one working diaphragm may sometimes cause significant pressure pulsation. High pressure peaks may not only result in decreased service life of the pump and its components, but may also limit the system efficiency.
As a technology leader, KNF is always looking to continuously improve existing pumps and to develop new pump technologies. Therefore, KNF has developed the low pulsation FP pump series in response to market needs.
In the following blog post, you will learn more about possible KNF technologies enabling particularly gentle liquid transfer at low pressure pulsation.
Stop-and-go traffic – or: Why pressure pulsation occurs
Liquid diaphragm pumps belong to the so-called volumetric displacement pumps category. The flow rate is generated by periodic volume changes inside the diaphragm chamber. Due to hydraulic resistances between the diaphragm chamber and the final load, the volume pulse turns into a pressure pulse. Hydraulic resistances like this can be found inside the pump, e.g. valves, but also as components inside the customer system (tubes, filters, constrictions, branches, etc.). You can think of this as being similar to the flow of traffic in a movie theater parking garage: After the end of a movie, many visitors are leaving the parking garage intermittently. If there were no barriers at the exit, the traffic would flow without backup (pressure). However due to obstacles such as a single-lane exit road, the volume pulse (many people leaving the movie theater simultaneously) turns into a pressure pulse (backup of cars). After all the cars have left the parking garage, it gets quiet until the end of the next movie (analogous to the suction stroke of the diaphragm pump).
For some applications or areas of use, the pressure pulsation can be significantly reduced by interconnecting several diaphragms in parallel or by using dampeners.
Why pressure pulsation should be avoided
In many pump applications, pressure pulsation or volume pulsation is not desired. Especially in the inkjet area, pressure fluctuations affect the quality of the printed image. On top of this, small tube diameters are frequently used in this application which results in high pressure losses. High pressure pulsation reduces the lifetime of system components, generates strong vibrations and thus a higher noise level. This may also lead to foaming of the liquid and, in the worst case, even cause damage to the transferred medium. Unfortunately, nearly all volumetric pumps, such as peristaltic, gear, piston or diaphragm pumps generate some pulsation.
As a leading manufacturer of diaphragm pumps, KNF has developed solutions for low pulsation liquid transfer to enable optimal application functionality: The FP pump series is based on two different operating principles. These are discussed in more detail below.
Principle 1: Utilization of multi-diaphragm pump technology
For many years, the portfolio of proven KNF diaphragm pumps has included both a single-headed and a double-headed version, the so-called boxer-style pump. With this, the connecting rod drives two 180° phase-shifted diaphragms simultaneously (analogous to a two-cylinder motor). While one diaphragm draws liquid from the suction line, the other diaphragm discharges it into the pressure line. This 180° phase-shifted mode of operation leads to pulsation-reduced transfer of the liquid. Figure 1 shows the instantaneous flow rate of multi-diaphragm pumps, such as double diaphragm pumps, compared to a single-headed pump. It impressively shows that flow rate peaks can be heavily reduced if several diaphragms are interconnected out-of-phase. From three diaphragms in use, peaks are reduced by a factor of 3. Due to this reduction of the maximum instantaneous flow rate, the pressure pulsation caused by the hydraulic resistances inside the system can be reduced significantly.
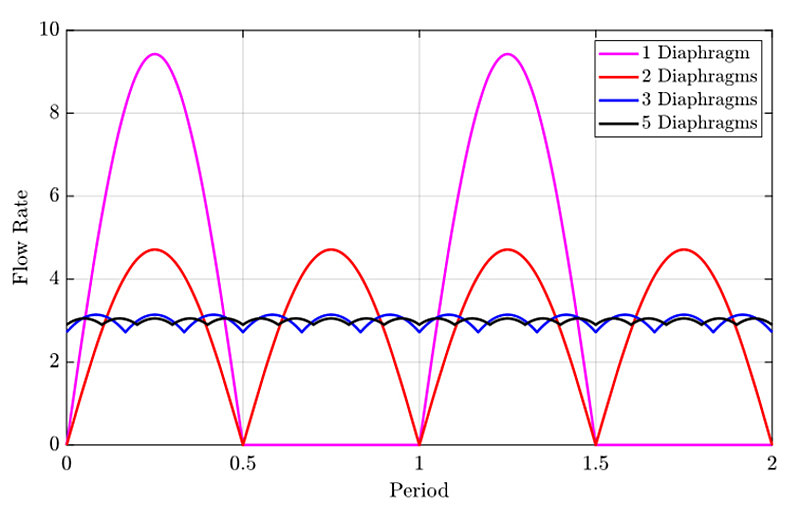
Joining the two separate inlets and outlets of a double diaphragm pump together is relatively cost and time-consuming for customers, requires more space, and poses the risk of potential leakage at the respective fittings. This is why KNF took it one step further with its FP pump series and developed low pulsation pumps with up to five phase-shifted pump diaphragms. The individual flow volumes are joined inside the pumps. This way, customers strongly benefit from having only one connection on the suction as well as on the pressure side. This considerably simplifies handling for the customer, reduces the space required, and eliminates additional tube connections.
Principle 2: Utilization of pulsation dampers and hydraulic accumulators
Another approach to reduce the pressure pulsation of a single-headed diaphragm pump is the use of a so-called pulsation damper that is usually mounted in the fluid system on the pressure side of the pump. This approach has also been successfully used by KNF for years in various flow and pressure rates. As already mentioned in the context of the boxer version, however, additional connections may lead to potential leakage points. Increased space requirements associated with the use of a pulsation damper are not always ensured in the customer’s system. In addition, the installation of a pulsation damper is associated with additional costs for the user.
In response to current market needs, KNF developed the world’s first liquid diaphragm pump featuring an integrated pulsation damper within the pump head on both the suction and pressure sides. This feat was accomplished in a very short time using state-of-the-art simulation and manufacturing tools. The video below shows the operation of such a pump. When the pump diaphragm moves downwards during suction, it not only draws liquid from the suction line, but also from the pulsation damper on the suction side. This only works because the damper diaphragm can also move downward due to the negative pressure. When the pump diaphragm is expelled, the liquid in the suction line can refill the damping chamber on the suction side. This can be easily recognized by the upward moving damper diaphragm. This way, an almost continuous volume flow is achieved in the suction line.
On the pressure side, the pulsation damper absorbs part of the volume expelled by the pump. This can be easily seen from the upward moving damper diaphragm. If the pump diaphragm now starts sucking in again, the volume stored in the damper on the pressure side is released to the pressure line (damper diaphragm on the pressure side moves downward). Thus, a continuous volume flow inside the tube is also achieved on the pressure side. Thanks to the low volume flow fluctuations in the tubes, the pressure pulsation on the suction and pressure side is minimal due to the integrated dampers. This innovative design provides the customer with a low pulsation liquid diaphragm pump that, except for back pressure, operates virtually independently of the customer’s system. Depending on the pump type and operating point, the pulsation can be reduced by up to a factor of 20. Furthermore, additional interfaces are eliminated for the customer.
Advantages of pumps with low pressure pulsation
Regardless of whether steady, low pulsation liquid transfer is achieved by means of a multi-diaphragm pump or pulsation damper, it offers many distinctive advantages for the customer. For a desired flow rate, a pressure drop occurs that is up to ten times lower. This is particularly important for media with higher viscosity such as ink. At the same time, the power consumption of the pump motor is reduced which means less heating of the motor. In addition, preventing high pressure pulsation may reduce the formation of micro-bubbles. It may also prevent foaming, especially for liquids with low surface tension. The controllability of the pump is also significantly increased as the flow rate is very linear to the speed and is independent of the customer system. Finally, the workload inside the pump is reduced and all components in the customer system are put under less stress due to the reduced pressure pulsation. This can increase the service life of the pump and other system components. As an additional effect, the vibration of the tubes is reduced which contributes to noise reduction.
To learn more about low pulsation liquid diaphragm pumps and how they may fit your application, contact our KNF experts. We can offer you a solution that can be specifically tailored to your needs.
75 Years: KNF Celebrates Company Anniversary
A treasure chest filled with memories, facts and stories. Learn more about KNF’s company history.
